Building 6, Zone 3, Yuekang Road,Bao'an District, Shenzhen, China
+86-13923401642Mon.-Sat.08:00-20:00
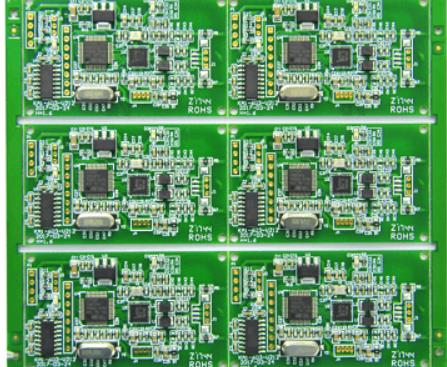
How to solder PCB chip components?
PCB SMD assembly welding steps:
1. Clean and fix PCB (printed circuit board)
Before PCB welding, check the PCB to be welded to ensure it is clean. The oily fingerprints and oxides on the surface shall be removed to avoid affecting the tin. When welding a PCB by hand, you can use a welding station or similar equipment to fix it if conditions permit, so as to facilitate welding. Generally speaking, it is best to fix it by hand. It is worth noting that your fingers should not touch the pads on the PCB, thus affecting the welding.
2. Securing SMD components
Fixation of PCB chip assembly is very important. According to the number of pins of the patch assembly, the fixing methods can be roughly divided into two types: single pin fixing method and multi pin fixing method. For SMD components with a few pins (usually 2-5), such as resistors, capacitors, diodes, triodes, etc., the single pin fixing method is usually used. In other words, first, tin a bonding pad on the circuit board.
Then hold the PCB assembly with tweezers, place it in the installation position, and gently press it against the circuit board. Use the soldering iron in the right hand to close the tin pad and melt the solder to solder the pins. After welding the pad, the component will not move, and the tweezers can be loosened at this time.
It is worth emphasizing that the pin of the chip must be correctly judged. For example, sometimes we will carefully fix the chip, or even complete the welding. During the inspection, we found that the pin corresponds to the error. A pin that is not the first pin is used as the first pin to be soldered! Too much regret! In this regard, these meticulous preliminary work must not be sloppy.
3. Solder the remaining pins
After that, the PCB assembly is fixed, and the other pins should be welded For components with a small number of pins, you can take soldering tin with your left hand and soldering iron with your right hand, and then spot weld in sequence For wafers with multiple dense pins, except for spot welding, drag welding can be used. That is, put enough tin on one pin, and then use a soldering iron to melt the solder to the other pins on the side The melted solder can flow. Sometimes, the circuit board can be tilted properly to remove excess solder It should be noted that no matter spot welding or resistance welding, adjacent pins are easily shorted by tin Don't worry about this, because it is available It should be noted that all pins are well connected to the pad, and there is no virtual soldering
4. Remove excess solder
In step 3, we mentioned the short circuit caused by welding. Now, let's talk about how to deal with this excess solder. In general, you can use the suction cups above to suck away excess solder. The method of using tin strip is very simple. Add a proper amount of flux (such as rosin) to the tin strip, and then stick it on the bonding pad. Put the clean soldering head on the tin strip and wait for the tin strip to heat up to absorb the bonding pad. After the upper solder melts, slowly push and pull from one end of the pad to the other, and the solder is sucked into the tape. It should be noted that after welding, the soldering head and tin strip should be drawn out from the pad at the same time. Then add flux to the solder strip or reheat it with a soldering iron head, and then gently pull the solder strip to separate it from the bonding pad to prevent the surrounding PCB components from burning. If there is no special sucker on the market, you can use the thin copper wire in the wire to make the sucker. The self-made method is: after stripping the outer layer of the wire, the inner thin copper wire is exposed. At this time, use a soldering iron to melt some rosin on the copper wire. In addition, if you are not satisfied with the welding results, you can use the suction cups again to remove the solder and weld the parts again.
5. Clean the welding position
After PCB welding, excess solder is removed, and the chip is basically welded However, due to the use of rosin for soldering and tin absorption tape, some rosin remains around the chip pins on the circuit board Although it does not affect the operation and normal use of the chip, it is not beautiful This may cause inconvenience during the inspection It is necessary to clean up these residues The common cleaning method can be to wash the board with water Here, alcohol is used for cleaning Cleaning tools can be cotton swabs or toilet paper with tweezers When cleaning and erasing, it should be noted that the amount of alcohol should be appropriate and its concentration should be high, so as to quickly dissolve residues such as rosin Secondly, the erasing force should be well controlled and not too large to avoid scratching the solder mask and damaging the chip pin At this time, you can use a soldering iron or a hot air gun to properly heat the alcohol to scrub the position, so that the residual alcohol can quickly evaporate At this point, the wafer welding is completed
PCB SMD assembly welding steps:
1. Clean and fix PCB (printed circuit board)
Before PCB welding, check the PCB to be welded to ensure it is clean. The oily fingerprints and oxides on the surface shall be removed to avoid affecting the tin. When welding a PCB by hand, you can use a welding station or similar equipment to fix it if conditions permit, so as to facilitate welding. Generally speaking, it is best to fix it by hand. It is worth noting that your fingers should not touch the pads on the PCB, thus affecting the welding.
2. Securing SMD components
Fixation of PCB chip assembly is very important. According to the number of pins of the patch assembly, the fixing methods can be roughly divided into two types: single pin fixing method and multi pin fixing method. For SMD components with a few pins (usually 2-5), such as resistors, capacitors, diodes, triodes, etc., the single pin fixing method is usually used. In other words, first, tin a bonding pad on the circuit board.
Then hold the PCB assembly with tweezers, place it in the installation position, and gently press it against the circuit board. Use the soldering iron in the right hand to close the tin pad and melt the solder to solder the pins. After welding the pad, the component will not move, and the tweezers can be loosened at this time.
It is worth emphasizing that the pin of the chip must be correctly judged. For example, sometimes we will carefully fix the chip, or even complete the welding. During the inspection, we found that the pin corresponds to the error. A pin that is not the first pin is used as the first pin to be soldered! Too much regret! In this regard, these meticulous preliminary work must not be sloppy.
3. Solder the remaining pins
After that, the PCB assembly is fixed, and the other pins should be welded For components with a small number of pins, you can take soldering tin with your left hand and soldering iron with your right hand, and then spot weld in sequence For wafers with multiple dense pins, except for spot welding, drag welding can be used. That is, put enough tin on one pin, and then use a soldering iron to melt the solder to the other pins on the side The melted solder can flow. Sometimes, the circuit board can be tilted properly to remove excess solder It should be noted that no matter spot welding or resistance welding, adjacent pins are easily shorted by tin Don't worry about this, because it is available It should be noted that all pins are well connected to the pad, and there is no virtual soldering
4. Remove excess solder
In step 3, we mentioned the short circuit caused by welding. Now, let's talk about how to deal with this excess solder. In general, you can use the suction cups above to suck away excess solder. The method of using tin strip is very simple. Add a proper amount of flux (such as rosin) to the tin strip, and then stick it on the bonding pad. Put the clean soldering head on the tin strip and wait for the tin strip to heat up to absorb the bonding pad. After the upper solder melts, slowly push and pull from one end of the pad to the other, and the solder is sucked into the tape. It should be noted that after welding, the soldering head and tin strip should be drawn out from the pad at the same time. Then add flux to the solder strip or reheat it with a soldering iron head, and then gently pull the solder strip to separate it from the bonding pad to prevent the surrounding PCB components from burning. If there is no special sucker on the market, you can use the thin copper wire in the wire to make the sucker. The self-made method is: after stripping the outer layer of the wire, the inner thin copper wire is exposed. At this time, use a soldering iron to melt some rosin on the copper wire. In addition, if you are not satisfied with the welding results, you can use the suction cups again to remove the solder and weld the parts again.
5. Clean the welding position
After PCB welding, excess solder is removed, and the chip is basically welded However, due to the use of rosin for soldering and tin absorption tape, some rosin remains around the chip pins on the circuit board Although it does not affect the operation and normal use of the chip, it is not beautiful This may cause inconvenience during the inspection It is necessary to clean up these residues The common cleaning method can be to wash the board with water Here, alcohol is used for cleaning Cleaning tools can be cotton swabs or toilet paper with tweezers When cleaning and erasing, it should be noted that the amount of alcohol should be appropriate and its concentration should be high, so as to quickly dissolve residues such as rosin Secondly, the erasing force should be well controlled and not too large to avoid scratching the solder mask and damaging the chip pin At this time, you can use a soldering iron or a hot air gun to properly heat the alcohol to scrub the position, so that the residual alcohol can quickly evaporate At this point, the wafer welding is completed
Just upload Gerber files, BOM files and design files, and the KINGFORD team will provide a complete quotation within 24h.