Building 6, Zone 3, Yuekang Road,Bao'an District, Shenzhen, China
+86-13923401642Mon.-Sat.08:00-20:00
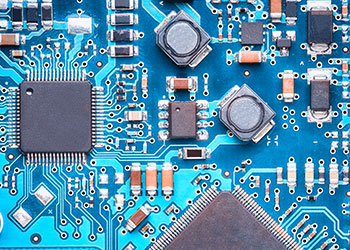
How to Design PCB of SMT Electronic Products
In order to facilitate customers to realize efficient and high-quality electronic assembly, Desheng provides customized printed circuit board services, including rapid proofreading of circuit boards, copying of circuit boards, and batch production of circuit boards As long as the PCB design files are provided and relevant requirements are met, Xunde will timely produce high-quality PCB that meets the design requirements
Therefore, how do SMT processing manufacturers usually implement PCB design for SMT electronic products? This paper will reveal
Step 1: Determine the overall objectives of electronic product functions, performance indicators, costs and overall dimensions.
When developing and designing new products, we must first position the efficiency, quality and cost of products. Generally speaking, any product design requires tradeoffs and compromises between efficiency, manufacturability and cost. At the beginning of design, the purpose and grade of the product must be accurately positioned.
Draw the process outline drawing SMT printed board, mark the length, width, PCB thickness, position and size of structural components, assembly holes, and reserve the edge size, so that the circuit designer can design the wiring within the effective range
Step 3: Determine the PCB process plan.
1. Determine the assembly form
The selection of assembly form depends on the type of components in the circuit, the size of the circuit board and the equipment conditions of the production line.
The principle to determine the PCB assembly form is usually to follow the principle of optimizing process, reducing cost and improving product quality. For example, whether it is possible to use a single panel instead of a double panel; Whether the double panel can be replaced by the welding method as much as possible; Plug in components shall be replaced with installed components as far as possible; Try not to use manual welding.
2. Determine process flow
The selection of process flow is mainly based on the assembly density of printed boards and the equipment conditions of SMT production lines of SMT manufacturers. When SMT production line has two welding equipment, reflow welding and wave soldering, the following matters can be considered:
a. Try to use reflow soldering because it has the following advantages over wave soldering:
– Small thermal shock to components;
-Good solder composition consistency and good solder joint quality;
Surface contact, good welding quality and high reliability;
Self alignment effect is suitable for automatic production with high production efficiency;
The process is simple, and the workload of repairing the circuit board is very small, which is conducive to saving manpower, power and data.
B. Under the mixed assembly condition of general density, when SMD and THC are on the same side of the PCB, the A-side printing solder paste, reflow soldering and b-side wave soldering processes are used: when THC is on the A-side of the PCB, the SMD is on the b-side of the PCB, and the b-side glue and wave soldering processes are used.
c. Under the condition of high-density mixed assembly, when there is no THC or only a small amount of THC, double-sided printing solder paste, reflow soldering process and a small amount of THC can be used as the post adhesion method; When there are many THCs on the A side, the A side printing solder paste, reflow soldering, B side dispensing and wave soldering processes are used.
Note: In PCB, it is forbidden to use flow soldering SMD process first, and then wave soldering THC
In order to facilitate customers to realize efficient and high-quality electronic assembly, Desheng provides customized printed circuit board services, including rapid proofreading of circuit boards, copying of circuit boards, and batch production of circuit boards As long as the PCB design files are provided and relevant requirements are met, Xunde will timely produce high-quality PCB that meets the design requirements
Therefore, how do SMT processing manufacturers usually implement PCB design for SMT electronic products? This paper will reveal
Step 1: Determine the overall objectives of electronic product functions, performance indicators, costs and overall dimensions.
When developing and designing new products, we must first position the efficiency, quality and cost of products. Generally speaking, any product design requires tradeoffs and compromises between efficiency, manufacturability and cost. At the beginning of design, the purpose and grade of the product must be accurately positioned.
Draw the process outline drawing SMT printed board, mark the length, width, PCB thickness, position and size of structural components, assembly holes, and reserve the edge size, so that the circuit designer can design the wiring within the effective range
Step 3: Determine the PCB process plan.
1. Determine the assembly form
The selection of assembly form depends on the type of components in the circuit, the size of the circuit board and the equipment conditions of the production line.
The principle to determine the PCB assembly form is usually to follow the principle of optimizing process, reducing cost and improving product quality. For example, whether it is possible to use a single panel instead of a double panel; Whether the double panel can be replaced by the welding method as much as possible; Plug in components shall be replaced with installed components as far as possible; Try not to use manual welding.
2. Determine process flow
The selection of process flow is mainly based on the assembly density of printed boards and the equipment conditions of SMT production lines of SMT manufacturers. When SMT production line has two welding equipment, reflow welding and wave soldering, the following matters can be considered:
a. Try to use reflow soldering because it has the following advantages over wave soldering:
– Small thermal shock to components;
-Good solder composition consistency and good solder joint quality;
Surface contact, good welding quality and high reliability;
Self alignment effect is suitable for automatic production with high production efficiency;
The process is simple, and the workload of repairing the circuit board is very small, which is conducive to saving manpower, power and data.
B. Under the mixed assembly condition of general density, when SMD and THC are on the same side of the PCB, the A-side printing solder paste, reflow soldering and b-side wave soldering processes are used: when THC is on the A-side of the PCB, the SMD is on the b-side of the PCB, and the b-side glue and wave soldering processes are used.
c. Under the condition of high-density mixed assembly, when there is no THC or only a small amount of THC, double-sided printing solder paste, reflow soldering process and a small amount of THC can be used as the post adhesion method; When there are many THCs on the A side, the A side printing solder paste, reflow soldering, B side dispensing and wave soldering processes are used.
Note: In PCB, it is forbidden to use flow soldering SMD process first, and then wave soldering THC
Just upload Gerber files, BOM files and design files, and the KINGFORD team will provide a complete quotation within 24h.