Building 6, Zone 3, Yuekang Road,Bao'an District, Shenzhen, China
+86-13923401642Mon.-Sat.08:00-20:00
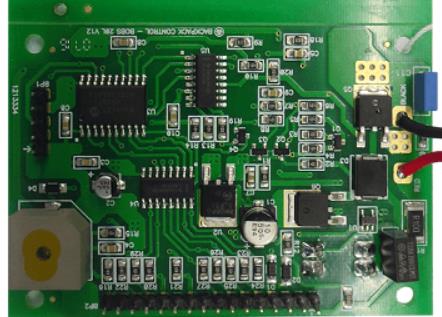
Understand the hard knowledge of SMT chip processing
High assembly density, small volume and light weight of electronic products The volume and weight of the chip module is only about 1/10 of that of the traditional chip module Generally, the volume of electronic products is reduced by 40%~60% and the weight is reduced by 60%~80% High reliability and strong anti vibration capability Low solder joint defect rate Good high frequency characteristics Reduce electromagnetic and radio frequency interference. It is easy to realize automation and improve production efficiency Reduce cost by 30% - 50% Save data, energy, equipment, man power, time, etc â Why use surface mount technology (SMT)? Electronic products are pursuing miniaturization, and the previously used perforated plug-in components can no longer be reduced Electronic products have more complete functions The integrated circuits (IC) used no longer have prefabricated components, especially large-scale and highly integrated integrated circuits, so surface mount components have to be used Mass production of products and automation of production. The factory must produce high-quality products with low cost and high output to meet customer needs and enhance market competitiveness The development of electronic components, the development of integrated circuits (IC), multiple applications of semiconductor materials
No cleaning can reduce the damage caused by the PCB There are still some components that cannot be cleaned The flux residue has been controlled and can be used according to the product appearance requirements to avoid visual inspection of the cleaning state The residual magnetic flux continuously improves its power efficiency to avoid leakage of finished products and any damage
No cleaning process has passed many international safety tests, proving that the chemical substances in the flux are stable and non corrosive - reflow defect analysis: solder ball: reason: 1. The screen hole and pad are not in the correct position, and the printing is not accurate, which makes the solder paste dirty the PCB. 2. Solder paste is exposed too much in the oxidation environment, and there is too much water in the air. 3. The heating is inaccurate, too slow and uneven. 4. The heating speed is too fast and the preheating interval is too long. 5. Solder paste dries too fast. 6. Insufficient flux activity. 7. Too much small tin powder. 8. The flux fluctuation in the reflux process is inappropriate. The process approval standard for solder balls is: when the distance between pads or printed wires is 0.13mm, the diameter of solder balls shall not exceed 0.13mm, or there shall not be more than five solder balls within 600mm square area.
Bridging: Generally speaking, the reason for solder bridging is that the solder paste is too thin, including low metal or solid content in the solder paste, low thixotropy, solder paste is easy to squeeze, solder paste particles are too large, and the surface tension of the flux is too small. There is too much solder paste on the bonding pad, and the reflow peak temperature is too high.
Open: Reason: 1. Insufficient solder paste. 2. Component pin coplanarity is insufficient. 3. Tin is not wet enough (not enough to melt, poor fluidity), and the solder paste is too thin, resulting in tin loss. 4. The contact pin absorbs tin (such as rushes) or there is a connection hole nearby. Coplanarity of pins is particularly important for fine pitch and ultra-fine pitch pin assemblies. One solution is to tin the pad in advance. Needle suction can be prevented by slowing the heating rate and heating the bottom surface on the top surface. You can also use flux with slow wetting speed and high active temperature or solder pastes with different tin/lead ratios to slow down the melting, so as to reduce the tin absorption of the needle. SMT related technologies constitute the design and manufacturing technology of electronic components and integrated circuits. Circuit design technology of electronic products. Circuit board manufacturing technology. Design and manufacturing technology of automatic placement equipment. Circuit assembly and manufacturing technology. Development and production technology of auxiliary materials for assembly and manufacturing. Mounter: arched (rack): the component feeder is fixed to the PCB of the base plate, and the placement head (with multiple vacuum suction nozzles installed) moves back and forth between the feeder and the base plate to take out the component from the feeder. After adjusting the position and direction of the components, place them on the base plate. Since the placement head is installed on the arch X/Y coordinate moving beam, it is named after it.
Methods for adjusting the position and direction of components: 1). Mechanical centering adjusts the position and nozzle rotation adjusts the direction. This method can achieve limited accuracy and will not be used in future models. 2) Laser identification, X/Y coordinate system adjustment position, nozzle rotation adjustment direction, this method can realize identification during flight, but cannot be used for ball grid array element BGA. 3) Camera recognition, X/Y coordinate system adjustment position, nozzle rotation adjustment direction. Generally, the camera is fixed. The placement head flies over the camera for imaging recognition, which is slightly longer than laser recognition, but it can identify any component. Some camera recognition systems that achieve recognition in flight have other sacrifices in mechanical structure. In this form, the speed of the placement head is limited due to long back and forth movement. At present, multiple vacuum nozzles are usually used to take materials at the same time (at most ten), and a double beam system is used to improve the speed, that is, the placing head on one beam takes materials, while the placing head on the other beam places parts, which is almost twice the speed of the single beam system. However, in practical applications, it is difficult to achieve the condition of simultaneous recovery, so different types of components need to be replaced with different vacuum nozzles, and there is a time delay in replacing the nozzle. The advantages of this model are that the system has a simple structure and can achieve high accuracy. It is suitable for components of various sizes and shapes, even for special-shaped components. Feeders are in the form of belts, tubes and trays. It is suitable for small and medium-sized batch production, and can also be used for mass production by combining multiple machines.
Turret type (Turret): The component feeder is placed on a single coordinate moving cart When working, the material transport vehicle moves the part feeder to the recovery position, places the part at the recovery position by the vacuum nozzle on the placement head, and rotates to the placement position (180 degrees with the recovery position) through the torque, and aligns the part during rotation Adjust the position and orientation of the components and place the components on the base plate
High assembly density, small volume and light weight of electronic products The volume and weight of the chip module is only about 1/10 of that of the traditional chip module Generally, the volume of electronic products is reduced by 40%~60% and the weight is reduced by 60%~80% High reliability and strong anti vibration capability Low solder joint defect rate Good high frequency characteristics Reduce electromagnetic and radio frequency interference. It is easy to realize automation and improve production efficiency Reduce cost by 30% - 50% Save data, energy, equipment, man power, time, etc â Why use surface mount technology (SMT)? Electronic products are pursuing miniaturization, and the previously used perforated plug-in components can no longer be reduced Electronic products have more complete functions The integrated circuits (IC) used no longer have prefabricated components, especially large-scale and highly integrated integrated circuits, so surface mount components have to be used Mass production of products and automation of production. The factory must produce high-quality products with low cost and high output to meet customer needs and enhance market competitiveness The development of electronic components, the development of integrated circuits (IC), multiple applications of semiconductor materials
No cleaning can reduce the damage caused by the PCB There are still some components that cannot be cleaned The flux residue has been controlled and can be used according to the product appearance requirements to avoid visual inspection of the cleaning state The residual magnetic flux continuously improves its power efficiency to avoid leakage of finished products and any damage
No cleaning process has passed many international safety tests, proving that the chemical substances in the flux are stable and non corrosive - reflow defect analysis: solder ball: reason: 1. The screen hole and pad are not in the correct position, and the printing is not accurate, which makes the solder paste dirty the PCB. 2. Solder paste is exposed too much in the oxidation environment, and there is too much water in the air. 3. The heating is inaccurate, too slow and uneven. 4. The heating speed is too fast and the preheating interval is too long. 5. Solder paste dries too fast. 6. Insufficient flux activity. 7. Too much small tin powder. 8. The flux fluctuation in the reflux process is inappropriate. The process approval standard for solder balls is: when the distance between pads or printed wires is 0.13mm, the diameter of solder balls shall not exceed 0.13mm, or there shall not be more than five solder balls within 600mm square area.
Bridging: Generally speaking, the reason for solder bridging is that the solder paste is too thin, including low metal or solid content in the solder paste, low thixotropy, solder paste is easy to squeeze, solder paste particles are too large, and the surface tension of the flux is too small. There is too much solder paste on the bonding pad, and the reflow peak temperature is too high.
Open: Reason: 1. Insufficient solder paste. 2. Component pin coplanarity is insufficient. 3. Tin is not wet enough (not enough to melt, poor fluidity), and the solder paste is too thin, resulting in tin loss. 4. The contact pin absorbs tin (such as rushes) or there is a connection hole nearby. Coplanarity of pins is particularly important for fine pitch and ultra-fine pitch pin assemblies. One solution is to tin the pad in advance. Needle suction can be prevented by slowing the heating rate and heating the bottom surface on the top surface. You can also use flux with slow wetting speed and high active temperature or solder pastes with different tin/lead ratios to slow down the melting, so as to reduce the tin absorption of the needle. SMT related technologies constitute the design and manufacturing technology of electronic components and integrated circuits. Circuit design technology of electronic products. Circuit board manufacturing technology. Design and manufacturing technology of automatic placement equipment. Circuit assembly and manufacturing technology. Development and production technology of auxiliary materials for assembly and manufacturing. Mounter: arched (rack): the component feeder is fixed to the PCB of the base plate, and the placement head (with multiple vacuum suction nozzles installed) moves back and forth between the feeder and the base plate to take out the component from the feeder. After adjusting the position and direction of the components, place them on the base plate. Since the placement head is installed on the arch X/Y coordinate moving beam, it is named after it.
Methods for adjusting the position and direction of components: 1). Mechanical centering adjusts the position and nozzle rotation adjusts the direction. This method can achieve limited accuracy and will not be used in future models. 2) Laser identification, X/Y coordinate system adjustment position, nozzle rotation adjustment direction, this method can realize identification during flight, but cannot be used for ball grid array element BGA. 3) Camera recognition, X/Y coordinate system adjustment position, nozzle rotation adjustment direction. Generally, the camera is fixed. The placement head flies over the camera for imaging recognition, which is slightly longer than laser recognition, but it can identify any component. Some camera recognition systems that achieve recognition in flight have other sacrifices in mechanical structure. In this form, the speed of the placement head is limited due to long back and forth movement. At present, multiple vacuum nozzles are usually used to take materials at the same time (at most ten), and a double beam system is used to improve the speed, that is, the placing head on one beam takes materials, while the placing head on the other beam places parts, which is almost twice the speed of the single beam system. However, in practical applications, it is difficult to achieve the condition of simultaneous recovery, so different types of components need to be replaced with different vacuum nozzles, and there is a time delay in replacing the nozzle. The advantages of this model are that the system has a simple structure and can achieve high accuracy. It is suitable for components of various sizes and shapes, even for special-shaped components. Feeders are in the form of belts, tubes and trays. It is suitable for small and medium-sized batch production, and can also be used for mass production by combining multiple machines.
Turret type (Turret): The component feeder is placed on a single coordinate moving cart When working, the material transport vehicle moves the part feeder to the recovery position, places the part at the recovery position by the vacuum nozzle on the placement head, and rotates to the placement position (180 degrees with the recovery position) through the torque, and aligns the part during rotation Adjust the position and orientation of the components and place the components on the base plate
Just upload Gerber files, BOM files and design files, and the KINGFORD team will provide a complete quotation within 24h.