Building 6, Zone 3, Yuekang Road,Bao'an District, Shenzhen, China
+86-13923401642Mon.-Sat.08:00-20:00
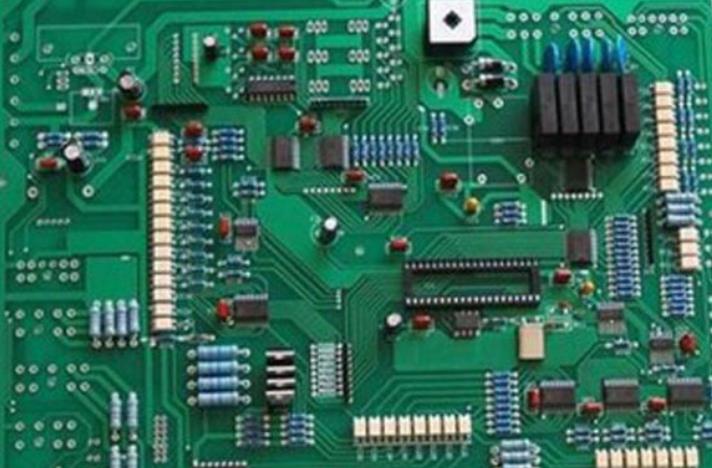
SMT production line and SMT mounter and their quality control
The following describes the nine main equipment supporting the system: SMT production line and smt mounter
1、 Solder paste mixer
The solder paste mixer can effectively evenly mix solder powder and solder paste. Achieve more perfect printing and reflow effect, save manpower and standardize operation. In this way, there is no need to open the tank, reducing the opportunity to absorb water vapor.
Second, oven
If necessary, bake the PCB to remove moisture from the PCB.
3. SMT board
It is used as a PCB and placed in the rack (turnbox) to automatically send the circuit board.
Solder paste printing machine
It is used for soldering printed PCB circuit board and is installed in front of the mounter
SPI solder paste thickness gauge
As a solder paste printer, it is a device for measuring the thickness, area and volume of solder paste (red glue) printed on PCB.
6、 Reflux furnace
7、 AOI detector
After being used as smt mounter, this is called pre welding inspection, which is used to detect the poor placement of components before welding, such as offset, reverse rotation, missing parts, reverse whitening and side standing of electronic components; It can also be used as the back of the reflux furnace. This is called post weld inspection, which is used to detect poor welding, offset, missing parts, reverse re inspection and solder joints with more or less tin of electronic components after reflow. Void welding and other defects.
8. SMT connection station
It is used as an intermediate connection device for connecting SMT production equipment.
SMT separator
It is mainly used to receive and store PCB boards after reflow soldering.
SMT production line is divided into automatic production line and semi-automatic production line. If the manufacturer wants to build a complete automatic placement production line, the placement machine is the most important equipment. The other nine devices are also indispensable. The manufacturer can also provide some as required. Other SMT peripheral equipment (such as: turnover machine, plate dropping machine, parallel transplanter, etc.).
Quality Control in SMT Production
Although the SMT production has implemented standardized and standardized processing procedure management, some undesirable phenomena that do not meet the processing process requirements are often found in the actual production process on site. According to the requirements of standard specifications and total quality control, it is necessary to classify these defective products, and conduct in-depth analysis and treatment of these defective products.
1) Establish archives standard system for quality control in SMT production and processing
Formulate SMT product quality inspection rules and regulations.
Formulate SMT product quality inspection standards and specifications.
Develop operation specifications for visual inspection, AOI inspection, ICT inspection and FCT inspection.
To standardize the use guide of test equipment (AOI tester, ICT tester and FCT tester).
Prepare inspection record report or label.
Common precautions for standard equipment operation.
2) On site management of product quality inspection in SMT production
Professionally trained quality control and inspection personnel strictly abide by SMT product quality inspection rules and regulations Set visual inspection or AOI inspection after solder paste printing, visual inspection after placement, visual inspection or AOI inspection after reflow soldering, ICT and FCT inspection after wave soldering, appearance inspection and product quality inspection after assembly; All inspections are based on inspection standards and specifications to determine whether the products are good or bad, and the inspection results are recorded for future reference or labeled accordingly; Use all equipment correctly according to the instructions; All inspection processes shall be carried out according to the standard procedures, and corresponding records shall be made; wait. For example, the requirements for ICT testing (common precautions): the machine is operated by dedicated personnel. Without approval and consent, non designers are not allowed to operate or modify the program, and irrelevant personnel are not allowed to use the machine computer; Operators must wear qualified electrostatic rings or gloves, and metal ornaments are not allowed; When placing the circuit board, hold it gently to avoid damaging the components; If the machine breaks down or the same bad condition is found three times in a row, the corresponding engineering and management personnel must be notified immediately for handling, and the next process can be carried out after inspection Operation steps of ICT test: check the data number, scan the operator code, hold the test board, open the socket cover, perform visual inspection, load the board, close the cover, scan the main screen, take the test results, open the cover, and take out the test board
The following describes the nine main equipment supporting the system: SMT production line and smt mounter
1、 Solder paste mixer
The solder paste mixer can effectively evenly mix solder powder and solder paste. Achieve more perfect printing and reflow effect, save manpower and standardize operation. In this way, there is no need to open the tank, reducing the opportunity to absorb water vapor.
Second, oven
If necessary, bake the PCB to remove moisture from the PCB.
3. SMT board
It is used as a PCB and placed in the rack (turnbox) to automatically send the circuit board.
Solder paste printing machine
It is used for soldering printed PCB circuit board and is installed in front of the mounter
SPI solder paste thickness gauge
As a solder paste printer, it is a device for measuring the thickness, area and volume of solder paste (red glue) printed on PCB.
6、 Reflux furnace
7、 AOI detector
After being used as smt mounter, this is called pre welding inspection, which is used to detect the poor placement of components before welding, such as offset, reverse rotation, missing parts, reverse whitening and side standing of electronic components; It can also be used as the back of the reflux furnace. This is called post weld inspection, which is used to detect poor welding, offset, missing parts, reverse re inspection and solder joints with more or less tin of electronic components after reflow. Void welding and other defects.
8. SMT connection station
It is used as an intermediate connection device for connecting SMT production equipment.
SMT separator
It is mainly used to receive and store PCB boards after reflow soldering.
SMT production line is divided into automatic production line and semi-automatic production line. If the manufacturer wants to build a complete automatic placement production line, the placement machine is the most important equipment. The other nine devices are also indispensable. The manufacturer can also provide some as required. Other SMT peripheral equipment (such as: turnover machine, plate dropping machine, parallel transplanter, etc.).
Quality Control in SMT Production
Although the SMT production has implemented standardized and standardized processing procedure management, some undesirable phenomena that do not meet the processing process requirements are often found in the actual production process on site. According to the requirements of standard specifications and total quality control, it is necessary to classify these defective products, and conduct in-depth analysis and treatment of these defective products.
1) Establish archives standard system for quality control in SMT production and processing
Formulate SMT product quality inspection rules and regulations.
Formulate SMT product quality inspection standards and specifications.
Develop operation specifications for visual inspection, AOI inspection, ICT inspection and FCT inspection.
To standardize the use guide of test equipment (AOI tester, ICT tester and FCT tester).
Prepare inspection record report or label.
Common precautions for standard equipment operation.
2) On site management of product quality inspection in SMT production
Professionally trained quality control and inspection personnel strictly abide by SMT product quality inspection rules and regulations Set visual inspection or AOI inspection after solder paste printing, visual inspection after placement, visual inspection or AOI inspection after reflow soldering, ICT and FCT inspection after wave soldering, appearance inspection and product quality inspection after assembly; All inspections are based on inspection standards and specifications to determine whether the products are good or bad, and the inspection results are recorded for future reference or labeled accordingly; Use all equipment correctly according to the instructions; All inspection processes shall be carried out according to the standard procedures, and corresponding records shall be made; wait. For example, the requirements for ICT testing (common precautions): the machine is operated by dedicated personnel. Without approval and consent, non designers are not allowed to operate or modify the program, and irrelevant personnel are not allowed to use the machine computer; Operators must wear qualified electrostatic rings or gloves, and metal ornaments are not allowed; When placing the circuit board, hold it gently to avoid damaging the components; If the machine breaks down or the same bad condition is found three times in a row, the corresponding engineering and management personnel must be notified immediately for handling, and the next process can be carried out after inspection Operation steps of ICT test: check the data number, scan the operator code, hold the test board, open the socket cover, perform visual inspection, load the board, close the cover, scan the main screen, take the test results, open the cover, and take out the test board
Just upload Gerber files, BOM files and design files, and the KINGFORD team will provide a complete quotation within 24h.