Building 6, Zone 3, Yuekang Road,Bao'an District, Shenzhen, China
+86-13923401642Mon.-Sat.08:00-20:00
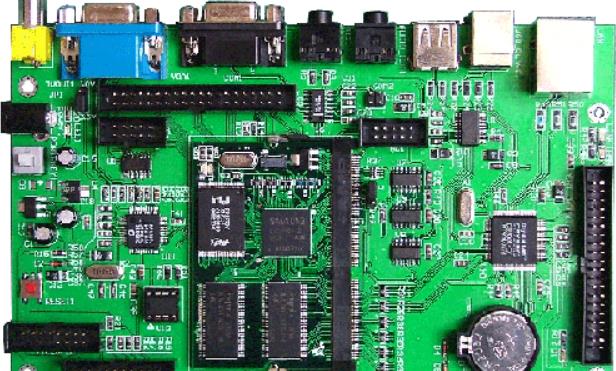
First inspection system for SMT manufacturing process
In SMT manufacturing technology, there is a practical error prevention method that can reduce the risk of wrong parts, reduce the error probability, and effectively improve the quality of the entire production process This approach is the first mechanism
The so-called first article mechanism is to make prototypes before formal production and processing. The committee will conduct a comprehensive inspection. After all inspections are passed, formal production and processing will begin. The first production is usually carried out under the following conditions:
Once at the beginning of each class
2. Replace the operator
3. Replace or adjust equipment and process equipment. (Replace the mold, replace the model)
4. Change technical conditions, process methods and process parameters
5. After selecting new or alternative materials. (such as data changes during processing)
A reasonable first article mechanism can ensure that the components to be installed on the mounter are correct, and there is no problem with the solder paste status and furnace temperature. It can effectively prevent batch defects. The first mechanism is a means of controlling the product manufacturing process in advance, an important method of product process quality control, and a practical and indispensable method for enterprises to ensure product quality and improve economic benefits.
Here are some common first inspection methods. According to different production and processing requirements, enterprises generally choose different detection methods. Although the methods used are different, the final actual effect is the same.
First article inspection system
It is a complete integrated system, which can directly input the BOM of production and processing products into the system The inspection device attached to the system will automatically detect the first sample and check the input BOM data to confirm the first part of production and processing Does the model meet the quality requirements? The system is more convenient and the detection process is automatic, which can reduce the error detection caused by human factors It can save labor costs, but the initial investment is relatively large At present, there is a certain market for SMT industry Recognized by some companies
LCR measurement
This test method is applicable to some simple PCB circuit boards. The number of components on PCB is reduced, and there is no inherited circuit. Only some PCB boards have components. After printing, there is no need to reheat the PCB circuit. Measure the components on the circuit board and compare them with the component ratings on the BOM. If there is no abnormality, formal production and processing can be started. Due to its low cost (only one LCR can operate), this method is widely used in many SMT plants.
3AOI test, which is very common in the SMT industry and can be used for all PCB production. The key is to determine the welding problem of electronic components by their shape characteristics, or to determine whether the electronic components on the PCB have wrong parts by checking the color and silk screen on the IC. Most SMT production lines will be equipped with one or two AOI devices as standard.
Flying needle detection
This test standard is usually used for some small batch production. Its advantages are convenient testing, strong program variability and good versatility. Most of them can test all types of PCB boards. However, the inspection efficiency is relatively low, and the inspection time of each plate will be very long. This inspection shall be carried out after the product passes through the reflow furnace. The key is to measure the resistance between two fixed points to determine whether the electronic components in the PCB have short circuit, empty solder and wrong parts.
ICT test
This inspection method is usually used for models that have been mass produced, and the production is usually relatively large. The detection efficiency is high, but the manufacturing cost is relatively high. Each type of PCB requires a special fixture. The service life of the fixture is not long, and the detection cost is high. The detection principle is similar to the flying probe detection. It also measures the resistance between two fixed points to determine whether the electronic components on the circuit have short circuits, empty soldering and wrong parts.
Function test
This detection method is usually used for some more complex PCB circuit boards. The PCB to be tested must be completed after welding. Through some specific fixtures, the formal use of the PCB is analogized. The PCB is placed in this analogy scene to observe whether the PCB can be used normally after power on. This test standard can accurately judge whether the PCB is normal. However, there are also problems of low detection efficiency and high detection cost.
7 X-ray inspection. For some people, the electronic components with BGA package on PCB need X-ray inspection for the first product produced X-rays have strong penetrability and are the first to be used for various types of PCB An instrument used for testing. X-ray fluoroscopy can display the thickness, shape and quality of solder joints, and solder density These specific quotas can fully reflect the welding quality of solder joints, including open circuit, short circuit, holes, internal bubbles and tin deficiency, which can be quantitatively analyzed
In SMT manufacturing technology, there is a practical error prevention method that can reduce the risk of wrong parts, reduce the error probability, and effectively improve the quality of the entire production process This approach is the first mechanism
The so-called first article mechanism is to make prototypes before formal production and processing. The committee will conduct a comprehensive inspection. After all inspections are passed, formal production and processing will begin. The first production is usually carried out under the following conditions:
Once at the beginning of each class
2. Replace the operator
3. Replace or adjust equipment and process equipment. (Replace the mold, replace the model)
4. Change technical conditions, process methods and process parameters
5. After selecting new or alternative materials. (such as data changes during processing)
A reasonable first article mechanism can ensure that the components to be installed on the mounter are correct, and there is no problem with the solder paste status and furnace temperature. It can effectively prevent batch defects. The first mechanism is a means of controlling the product manufacturing process in advance, an important method of product process quality control, and a practical and indispensable method for enterprises to ensure product quality and improve economic benefits.
Here are some common first inspection methods. According to different production and processing requirements, enterprises generally choose different detection methods. Although the methods used are different, the final actual effect is the same.
First article inspection system
It is a complete integrated system, which can directly input the BOM of production and processing products into the system The inspection device attached to the system will automatically detect the first sample and check the input BOM data to confirm the first part of production and processing Does the model meet the quality requirements? The system is more convenient and the detection process is automatic, which can reduce the error detection caused by human factors It can save labor costs, but the initial investment is relatively large At present, there is a certain market for SMT industry Recognized by some companies
LCR measurement
This test method is applicable to some simple PCB circuit boards. The number of components on PCB is reduced, and there is no inherited circuit. Only some PCB boards have components. After printing, there is no need to reheat the PCB circuit. Measure the components on the circuit board and compare them with the component ratings on the BOM. If there is no abnormality, formal production and processing can be started. Due to its low cost (only one LCR can operate), this method is widely used in many SMT plants.
3AOI test, which is very common in the SMT industry and can be used for all PCB production. The key is to determine the welding problem of electronic components by their shape characteristics, or to determine whether the electronic components on the PCB have wrong parts by checking the color and silk screen on the IC. Most SMT production lines will be equipped with one or two AOI devices as standard.
Flying needle detection
This test standard is usually used for some small batch production. Its advantages are convenient testing, strong program variability and good versatility. Most of them can test all types of PCB boards. However, the inspection efficiency is relatively low, and the inspection time of each plate will be very long. This inspection shall be carried out after the product passes through the reflow furnace. The key is to measure the resistance between two fixed points to determine whether the electronic components in the PCB have short circuit, empty solder and wrong parts.
ICT test
This inspection method is usually used for models that have been mass produced, and the production is usually relatively large. The detection efficiency is high, but the manufacturing cost is relatively high. Each type of PCB requires a special fixture. The service life of the fixture is not long, and the detection cost is high. The detection principle is similar to the flying probe detection. It also measures the resistance between two fixed points to determine whether the electronic components on the circuit have short circuits, empty soldering and wrong parts.
Function test
This detection method is usually used for some more complex PCB circuit boards. The PCB to be tested must be completed after welding. Through some specific fixtures, the formal use of the PCB is analogized. The PCB is placed in this analogy scene to observe whether the PCB can be used normally after power on. This test standard can accurately judge whether the PCB is normal. However, there are also problems of low detection efficiency and high detection cost.
7 X-ray inspection. For some people, the electronic components with BGA package on PCB need X-ray inspection for the first product produced X-rays have strong penetrability and are the first to be used for various types of PCB An instrument used for testing. X-ray fluoroscopy can display the thickness, shape and quality of solder joints, and solder density These specific quotas can fully reflect the welding quality of solder joints, including open circuit, short circuit, holes, internal bubbles and tin deficiency, which can be quantitatively analyzed
Just upload Gerber files, BOM files and design files, and the KINGFORD team will provide a complete quotation within 24h.