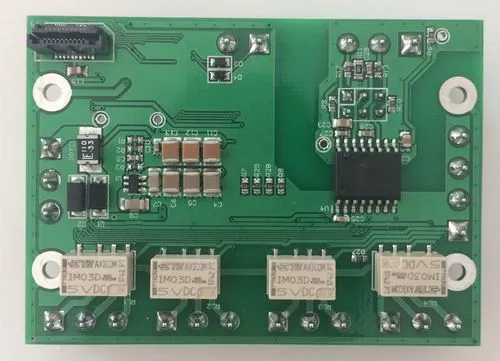
Crimping is a necessary assembly process in the production process of circuit boards, but this process will encounter copper foil wrinkling, bias of the laminated layer, resin cavities, and so on. Let's take a closer look.
1、 Preface
For multilayer PCB manufacturers, pressing is the most important process. There are many problems worth studying and discussing in the production process, such as copper foil wrinkling, laminated layer deflection, resin cavity, white edge and white angle, delamination and blistering, uneven plate thickness, etc.
To solve the above problems, it is necessary to have a clear understanding of the main pressing materials (inner core board, PP) and the control points of the press and be familiar with their characteristics.
2、 Main materials in pressing process
A. Inner core plate
The core board of multilayer PCB board that has been etched into an inner pattern is called the inner core board. Before pressing, the inner core board must be browning (blackening) treated to increase the roughness of the inner copper foil surface, so that the PP sheet adhesive can fully combine with the copper surface during the pressing process, so as to increase the bonding force between the PP and the copper surface.
As the layers of multilayer boards become higher and higher, the inner core boards become thinner and thinner. The horizontal browning process gradually takes the vertical blackening process to confirm whether the browning effect of the inner core boards meets the requirements, mainly from three aspects: micro etching amount, acid resistance time, and browning tension.
B. Prepreg (PP):
1. Composition:
Commonly used PP sheets are mainly composed of epoxy resin and glass fiber;
2. Main basic physical properties:
① Glue content RC%: the proportion of epoxy resin can be tested according to the test method of IPC-TM-650 2.3.16;
② Gel time GT: the time required from testing the B-stage PP sheet at 170 ℃ to fully curing the C-stage, which can be tested according to the test method of IPC-TM-650 2.3.18;
③ Volatile matter V C%: test the residual solvent of PP tablets after the immersion process, which can be tested according to IPC-TM-650 2.3.19;
3. Functions:
① As the medium combined with core board and core board, PCB core board and copper foil;
② Impedance control: provide proper thickness of insulation layer;
4. Specification:
At present, the main PP sheets used are 106, 1080, 3313., 2116, 1506, 7628. The pressing thickness of PP sheets with different specifications, the same specification and different glue content are different.
5. Storage conditions:
Humidity: ≤ 50% RH;
Temperature: ≤ 5 ℃: can be stored for 180 days; It can be stored for 90 days at 20 ± 2 ℃;
3、 Crimping equipment
1. Type of hot press:
According to different heating methods, the main types can be divided into:
① Electric heating: This is an early heating method, but it is rarely used now because of unstable temperature rise and fall
② Hot kerosene heating: the heat medium oil is heated by the boiler, and then the heat is transferred to the press by the heat medium oil. Because the heat provided is stable, it is easy to control the temperature rise and fall. At present, most presses use this heating method.
2. Pressure up method:
At present, most of the presses use hydraulic pressurization, and the pressure source is a downward cylindrical cylinder
3. Control points:
① Vacuum: after feeding the press and before starting to press, vacuumize it to avoid bubbles remaining in the pressing process;
② Time: the slope and holding time of temperature and pressure at each stage mainly affect the heating rate and curing time;
③ Pressure: the pressure on the production board at each stage mainly affects the glue flow and stress release of the production board;
④ Temperature: the temperature of the hot plate of the press at each stage mainly affects the actual temperature of the production plate;
4、 Quality key points after pressing:
1. Reliability of production board:
① Thermal stress: measure the heat resistance of the production plate. Test method: thermal shock (288 ± 5 ℃, 3 times of tin dipping, 10sec/time);
②TG; To measure whether PP of production board is completely cured, test method: IPC-TM-650 2.4.25 DSC
③ Peel strength: measure the adhesion between copper foil and PP of PCB production board. Test method: IPC-TM-650 2.4.8
2. Thickness:
① Slice and measure the thickness of each dielectric layer;
② Use a thickness gauge to measure the thickness of the edge and middle of the production plate, generally measuring 5 points or 9 points;
3. Appearance: no pits and dents, copper foil wrinkles, white edges and corners
5、 Conclusion
Anomalies generated in the pressing process can generally be found after the outer layer is etched (especially resin cavities, white edges and white corners). At this time, the pressing production time from the production board has exceeded 3-5 days, and the abnormal tracking is relatively difficult. According to past experience, most of the exceptions are caused by process operations or material and equipment exceptions. Therefore, in daily operation management and control, the WI standard must be fully followed. The spot check and detection of PCB equipment must be completed regularly. In case of any exception, the machine must be shut down in time to solve it.