Building 6, Zone 3, Yuekang Road,Bao'an District, Shenzhen, China
+86-13923401642Mon.-Sat.08:00-20:00
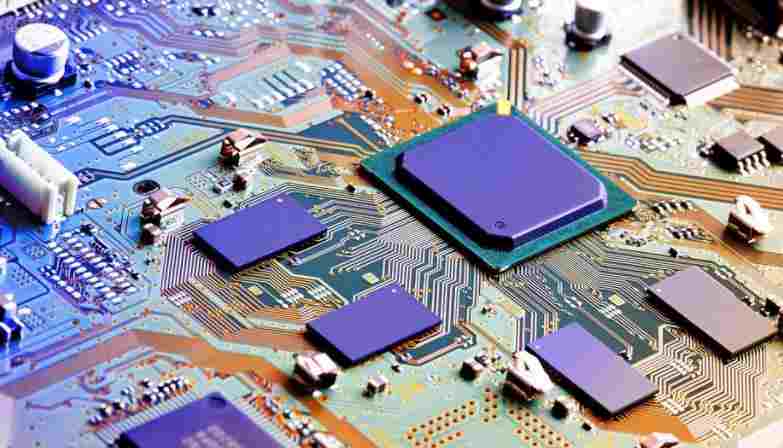
What are the characteristics of SMT assembly process?
SMT placement process can be compared with the traditional through hole insertion technology (THT) From the perspective of assembly technology, the fundamental difference between SMT and THT lies in "pasting" and "inserting" "The differences between the two are also reflected in various aspects of the matrix, components, component shapes, solder joint shapes and assembly process methods
THT uses leaded parts. The circuit connecting wire and mounting hole are designed on the printed board. Insert the component leads into the pre drilled holes on the PCB, then temporarily fix them, and use wave soldering on the other side of the substrate. Welding technology is used for welding to form reliable welding points and establish long-term mechanical and electrical connection. The main components and solder joints of the components are distributed on both sides of the substrate. With this method, because the components have leads, when the circuit density reaches a certain level, the problem of reducing the volume cannot be solved.
The so called surface assembly technology (process) refers to the chip structure components or minimized components suitable for surface assembly, which is placed on the surface of the printed circuit board according to the circuit requirements and welded by reflow soldering or wave soldering The assembly process forms the assembly technology of electronic components with specific functions For traditional THT PCB, components and solder joints are located on both sides of the board; When on the SMT circuit board, the solder joints and components are on the same side of the circuit board Therefore, on the printed circuit board of SMT, through holes are only used to connect wires on both sides of the circuit board. The number of holes is much smaller and the diameter of holes is much smaller With this kind of pipe, the assembly density of the circuit board can be greatly improved
The surface mount technology has the following advantages over the pipes of through hole inserts:
(1) Realize miniaturization. The geometric size and volume of SMT electronic components are much smaller than those of through hole plug-in components, which can usually be reduced by 60% - 70%, or even 90%. The weight is reduced by 60% - 90%.
(2) The signal transmission rate is high. Compact structure, high assembly density. When installed on the circuit board on both sides, the assembly density can reach 5.5-20 solder joints/cm., Due to short connection and low delay, high-speed signal transmission can be realized. At the same time, it is more resistant to vibration and shock. This is of great significance to the ultra high speed operation of electronic equipment.
(3) Good high frequency characteristics. Since the components have no leads or short leads, the distribution parameters of this circuit are naturally reduced, and the RF interference is also reduced.
(4) It is beneficial to automatic production and improves output and production efficiency. Due to the standardization and serialization of chip modules and the consistency of welding conditions, SMT has a very high degree of automation, which greatly reduces module failures caused during welding and improves reliability.
(5) Low data cost. At present, except for a few varieties that are difficult to carry out chip or package with extremely high precision, the package cost of most SMT components is lower than that of iFHT components of the same type and function. The sales price of SMT components is as follows. Lower than THT assembly.
(6) SMT technology simplifies the production process of electronic products and reduces production costs When assembled on a printed circuit board, the lead wires of the components do not need to be reshaped, bent or shortened, thus shortening the entire production process and improving the production efficiency The processing cost of circuits with the same function is lower than that of through hole insertion, which usually reduces the total production cost by 30% to 50%
SMT placement process can be compared with the traditional through hole insertion technology (THT) From the perspective of assembly technology, the fundamental difference between SMT and THT lies in "pasting" and "inserting" "The differences between the two are also reflected in various aspects of the matrix, components, component shapes, solder joint shapes and assembly process methods
THT uses leaded parts. The circuit connecting wire and mounting hole are designed on the printed board. Insert the component leads into the pre drilled holes on the PCB, then temporarily fix them, and use wave soldering on the other side of the substrate. Welding technology is used for welding to form reliable welding points and establish long-term mechanical and electrical connection. The main components and solder joints of the components are distributed on both sides of the substrate. With this method, because the components have leads, when the circuit density reaches a certain level, the problem of reducing the volume cannot be solved.
The so called surface assembly technology (process) refers to the chip structure components or minimized components suitable for surface assembly, which is placed on the surface of the printed circuit board according to the circuit requirements and welded by reflow soldering or wave soldering The assembly process forms the assembly technology of electronic components with specific functions For traditional THT PCB, components and solder joints are located on both sides of the board; When on the SMT circuit board, the solder joints and components are on the same side of the circuit board Therefore, on the printed circuit board of SMT, through holes are only used to connect wires on both sides of the circuit board. The number of holes is much smaller and the diameter of holes is much smaller With this kind of pipe, the assembly density of the circuit board can be greatly improved
The surface mount technology has the following advantages over the pipes of through hole inserts:
(1) Realize miniaturization. The geometric size and volume of SMT electronic components are much smaller than those of through hole plug-in components, which can usually be reduced by 60% - 70%, or even 90%. The weight is reduced by 60% - 90%.
(2) The signal transmission rate is high. Compact structure, high assembly density. When installed on the circuit board on both sides, the assembly density can reach 5.5-20 solder joints/cm., Due to short connection and low delay, high-speed signal transmission can be realized. At the same time, it is more resistant to vibration and shock. This is of great significance to the ultra high speed operation of electronic equipment.
(3) Good high frequency characteristics. Since the components have no leads or short leads, the distribution parameters of this circuit are naturally reduced, and the RF interference is also reduced.
(4) It is beneficial to automatic production and improves output and production efficiency. Due to the standardization and serialization of chip modules and the consistency of welding conditions, SMT has a very high degree of automation, which greatly reduces module failures caused during welding and improves reliability.
(5) Low data cost. At present, except for a few varieties that are difficult to carry out chip or package with extremely high precision, the package cost of most SMT components is lower than that of iFHT components of the same type and function. The sales price of SMT components is as follows. Lower than THT assembly.
(6) SMT technology simplifies the production process of electronic products and reduces production costs When assembled on a printed circuit board, the lead wires of the components do not need to be reshaped, bent or shortened, thus shortening the entire production process and improving the production efficiency The processing cost of circuits with the same function is lower than that of through hole insertion, which usually reduces the total production cost by 30% to 50%
Just upload Gerber files, BOM files and design files, and the KINGFORD team will provide a complete quotation within 24h.