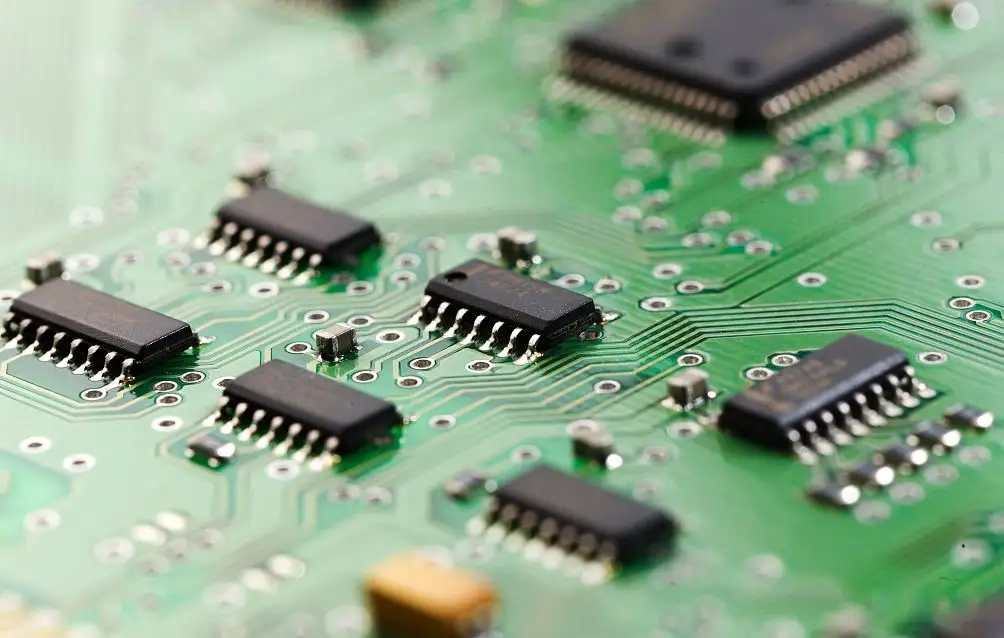
Detailed sharing of PCB assembly inspection and test option guide
PCB Assembly Inspection and Test Options
With the development of technology and the increasing complexity of PCBA, the test and inspection options of these boards must be carefully considered. PCB is a key component, which is expected to work normally in various environments. Appropriate test procedures and inspection measures are required to maintain product quality and reliability.
Benefits of PCB inspection and testing
Having a trusted contract manufacturer is one of the most critical steps to successfully build a circuit board. The company is proud to provide customers with high-quality products. This is accomplished through years of repeated PCB assembly and manufacturing process. We pay close attention to preventive measures and pre construction steps, rather than finding problems afterwards and repairing defects through rework. The most common inspection and testing methods with rich experience of the Company are:
Visual examination
Automated optical inspection
X-ray inspection
First article inspection
Online test
functional testing
Aging test
PCB has various shapes, dimensions and quality requirements. They can be rigid or flexible, single-sided, double-sided, multi-layer, and others. The industry also uses three "categories" to classify PCBs and PCBAs. They are Level 1, Level 2 and Level 3, of which Level 3 is the highest quality and requires the most attention.
As category requirements increase, the complexity of inspection and testing methods increases. Both PCB manufacturing and PCB assembly require a unique set of inspection and test methods to manufacture circuit boards according to specifications.
Visual examination
The most basic form of inspection is visual inspection. This is accomplished by having the technician review the circuit board with the gold plate, bill of materials, and printed matter. Then, the person checks whether there are wrong components, missing components, welding bridges, missing solder, tombstone falling off and other various errors. The equipment that can be used includes magnifying glass, high-power microscope, and of course, good lighting equipment. Because this method is highly operator dependent, it can be time consuming for large and complex boards. This is mainly done at the end, but it is important to visually inspect the circuit board throughout the manufacturing process to verify the procedures and procedures. The inspection after SMT placement can find out whether the picking and placement machine has missed or wrong component placement and solder paste problems. The company uses high power to provide our operators with multiple light sources and glare free lighting, so as to fully understand the PCBA under inspection. Each lens has an adjustable high-power lens for viewing to minimize eye fatigue.
Automated Optical Inspection (AOI)
AOI uses high-resolution cameras and software to capture manufacturing errors. The software essentially checks multiple images of the inspected circuit board against the "golden" circuit board images stored in its memory, and marks the differences.
These machines can be placed on the entire SMT production line. The inspection after reflow stage can find defects in welding, such as dry solder, solder bridge, insufficient wetting, tombstone falling off, etc. The operator can then use the feedback from the machine to make more subtle adjustments to the previous stages to ensure that defects are reduced.
Although AOI technology has come a long way, it still has some weaknesses. On the one hand, AOI is not good at through-hole parts. It can catch many through-hole errors, such as wrong or missing parts, but sometimes the height difference, cast shadows and hidden parts may be the limitations of AOI. Programming also takes some time, which is an additional overhead.
X-ray inspection
For components with hidden leads, X-ray inspection is required. There are pins arranged below the BGA, which makes it impossible to check its connection optically after welding. Then use X-ray to check whether all leads are welded correctly.
First article inspection
In order to validate procedures and components, the OEM usually requires the first inspection of the product. The company's FAI plan is different. Some require CM to verify the completion of the FAI in written documents, and some require that the first article be actually sent to them for approval. No matter what you think is necessary, it is very important to communicate with CM to check all boxes.
Online and functional testing
Online test: This test form requires a customized fixture, usually called a nail bed. Usually, several spring loaded metal probes are assembled on the insulating bed in the form of array. If ICT test is regarded as the best test form, it is usually planned in the design phase, because this requires the designer to place the test pad at the key position of the copper wiring on the bottom layer of PCB.
The tester places the assembled PCB on the probe to electrically connect it to the test pad. Sometimes it is manual or built in the lamp. The test will then check various parameters, such as the resistance, capacitance and inductance between the specified probes, and the mark difference with the established standard.
Function test: This method varies greatly. It is essentially a field simulation device. This test form is created by the OEM and handed over to CM for running. It usually includes a power supply and several inputs to ensure that the board works as expected.
Aging test
The aging test can simulate the real environment. The PCB assembly will be set at the maximum temperature from 24 hours for a specified time, and after cooling, there should be no expected performance problems. This can be verified by functional testing or ICT.
Inspection and test by the Company
We provide inspection and testing methods here according to customer requirements. Whether your circuit board needs various forms of testing or few forms of testing, our experienced team will help you. PCB processing factory explains and shares PCB assembly inspection and test option guide, test procedures and inspection measures in detail to maintain product quality and reliability.