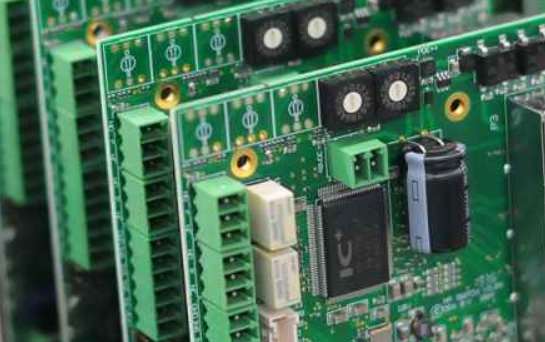
SMT mounter life and structural components
This SMT is placed on the SMT production line It is included behind the dispenser or solder paste printer It is a device for accurately placing surface mounted components on PCBpads by moving placement heads This SMT placement machine is the core production equipment in the SMT process At the same time, the SMT placement machine is usually more expensive If there is a failure or the service life is shortened, the cost of SMT placement will be greater for the manufacturer
1. Strengthen the daily maintenance of the mounter
SMT mounting machine is a very complex, high-tech and high-precision machine, which requires constant temperature, humidity and a very clean environment. The daily maintenance must be carried out in strict accordance with the requirements of equipment regulations, and the daily, weekly, monthly, semi annual and annual maintenance measures must be observed.
Circuit board
SMT places the daily maintenance contents of the machine
1. 10 minutes before work every day, the technicians will guide the operator to start the shutdown for daily maintenance.
2. Wipe the dust on the machine surface with a clean white cloth, including the body surface, display, keyboard, mouse, button, switch, etc. If necessary, wipe the machine surface with a rag dipped in soapy water, which must be screwed dry without dripping. It is not allowed to clean with alcohol or dish washing water.
3. Check whether the air pressure reaches 0.5MPA.
4. Check whether the PCB conveyor belt runs smoothly. Use PCB to test without card.
5. Check whether all safety devices are normal, including front and rear safety doors and feeder floating height sensors, and check whether the area sensors are normal, test the functions of each sensor under the running and paused states, and the display screen can normally display the alarm state of the sensors.
6. Use a vacuum cleaner to clean the scattered parts inside the machine.
7. Use lens paper to clean the dust on the VCS lens of the laser sensor.
8. Warm up the machine, listen to whether the sound of the machine is abnormal, and start production only after there is no abnormality.
Structural components of SMT mounter
1. Mounter host
1. Main power switch: turn on or off the host power
2. Visual display: display the identification of images or components and marks obtained by moving the lens. 3. Operation display: display the VIOS software screen of machine operation. If errors or problems occur during the operation, the correction information will also be displayed on this screen.
4. Warning light: use green, yellow and red to instruct the working state of the mounter.
Green: the machine is in automatic operation
Yellow: Error (unable to return to the origin, picking error, identification failure, etc.) or interlock.
Red: The machine is in the emergency stop state (when pressing the machine or YPU stop button).
5. Emergency stop button: press this button to immediately trigger the emergency stop.
2. Working head assembly
1. Working head assembly: move along XY direction (or X direction), take out parts from feeder and install them on PCB.
2. Moving handle of working head assembly: when the servo control is released, it can be moved in all directions by hand. This handle is usually used when moving the work head assembly manually.
Third, visual system
1. Moving lens: used to identify the mark or photo position or coordinate tracking on PCB.
2. Independent visual lens: used to identify components, mainly QPF with pins.
3. Backlight component: when the independent visual lens is used for identification, the component is illuminated from the back.
4. Laser parts: laser beam can be used to identify parts, mainly sheet parts.
5. Multi angle lens: multiple parts can be recognized at the same time to speed up recognition.
4. Feeding platform
Belt feeder, bulk feeder and tube feeder (multi tube feeder) can be installed on the front or rear feeder platform of the mounting machine.
5、 Shaft structure
X axis: the moving head assembly is parallel to the PCB transmission direction.
Y-axis: the moving head assembly is perpendicular to the PCB transmission direction
Z axis: controls the height of the working head assembly.
R axis: it controls the rotation of nozzle axis of working head assembly.
W axis: adjust the width of the transport track.