Building 6, Zone 3, Yuekang Road,Bao'an District, Shenzhen, China
+86-13923401642Mon.-Sat.08:00-20:00
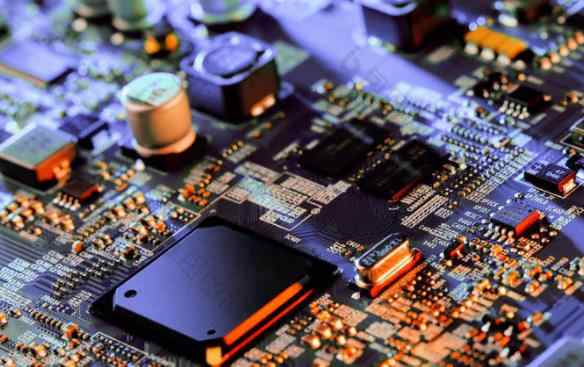
Introduction to MES System in SMT/PCB Assembly Industry
SMT is a popular technology and process in electronic assembly industry To ensure SMT production, at least three conditions must be accurately controlled: solder paste supply, placement data comparison, reflow soldering and inspection In order to manage the above key factors, driven by external and internal demands, companies often need to introduce new management technologies and methods to support the needs of management and development
With the rapid development of electronic technology and the shortening of product cycle, PCB component manufacturers are required to meet high requirements At the same time, global competition brings more and more pressure to enterprises If modern PCB assembly manufacturing enterprises want to survive and develop in the competition, they must adopt new production models so that customers can quickly respond and provide high-quality products At present, system integration and information integration are new efficient management technologies for enterprises
Many companies continue to improve the automation of the SMT production line and introduce high-quality enterprise management systems, which has improved their production management level.
How to effectively combine the advanced production line control system with the enterprise level production execution information system and build a bridge between them is a problem to be solved in the enterprise information construction. MES manufacturing execution system can solve this problem. Manufacturing Execution System (MES) is a workshop oriented execution information system, which is located between the upper project management system and the lower production process control system. It collects on-site real-time information to optimize the management of the entire production process from order placement to product completion.
PCB assembly industry is a typical process manufacturing industry, with a high degree of equipment automation. In order to fully tap the production potential of advanced equipment, optimize production behavior, and comprehensively improve the level of enterprise information management, the construction and application of MES system is particularly important.
Overview of MES system solutions in the assembly industry:
1. At present, MES system is widely used in China. The enterprise shall customize the MES system to meet the company's needs and development process through analysis and planning according to the company's internal and external conditions. For the assembly industry, the requirements for information automation are relatively high. The implementation of MES system can start from data collection and monitoring. On this basis, data quality analysis and process scheduling will be effective.
2. MES system is a bridge to communicate production and management information, and plays a connecting role in enterprise information integration system. ERP system without MES will not be able to organize production quickly according to market demand. In this case, the MES system shall handle the interface with the upper ERP system.
3. Agile production is the core of advanced manufacturing mode. Traditional MES system solutions are difficult to adapt to this demand. The MES system of agile manufacturing must have good integration, compatibility, adaptability, scalability and reliability.
The construction goals of MES system in PCB assembly industry are:
1) Build a MES platform with unified basic data and system framework. Provide customized user interface, business module and secondary development. 2) According to the requirements of the lean production management mode, a MES system is developed to realize the dynamic quality control of the production process. Through the establishment of SMT assembly line production process management control model. Collect and upload information data in real time, and monitor and schedule them. It realizes the integrated information management from production task allocation, equipment management to on-site dynamic scheduling.
3) Provide dynamic quality analysis method, real-time quality problem alarm, promote the improvement of management level, and make the quality control mode transition from manual inspection to automatic processing and real-time control. Establish a quality knowledge base to promote the optimization of quality standards. Through collection, analysis, treatment and accumulation, the quality is improved.
4) Complete the integration with the existing information system of the enterprise.
According to PCB assembly industry, functional module division mainly includes data acquisition, monitoring and alarm, dynamic quality process control, process planning and scheduling, equipment management, auxiliary production site management, etc
SMT is a popular technology and process in electronic assembly industry To ensure SMT production, at least three conditions must be accurately controlled: solder paste supply, placement data comparison, reflow soldering and inspection In order to manage the above key factors, driven by external and internal demands, companies often need to introduce new management technologies and methods to support the needs of management and development
With the rapid development of electronic technology and the shortening of product cycle, PCB component manufacturers are required to meet high requirements At the same time, global competition brings more and more pressure to enterprises If modern PCB assembly manufacturing enterprises want to survive and develop in the competition, they must adopt new production models so that customers can quickly respond and provide high-quality products At present, system integration and information integration are new efficient management technologies for enterprises
Many companies continue to improve the automation of the SMT production line and introduce high-quality enterprise management systems, which has improved their production management level.
How to effectively combine the advanced production line control system with the enterprise level production execution information system and build a bridge between them is a problem to be solved in the enterprise information construction. MES manufacturing execution system can solve this problem. Manufacturing Execution System (MES) is a workshop oriented execution information system, which is located between the upper project management system and the lower production process control system. It collects on-site real-time information to optimize the management of the entire production process from order placement to product completion.
PCB assembly industry is a typical process manufacturing industry, with a high degree of equipment automation. In order to fully tap the production potential of advanced equipment, optimize production behavior, and comprehensively improve the level of enterprise information management, the construction and application of MES system is particularly important.
Overview of MES system solutions in the assembly industry:
1. At present, MES system is widely used in China. The enterprise shall customize the MES system to meet the company's needs and development process through analysis and planning according to the company's internal and external conditions. For the assembly industry, the requirements for information automation are relatively high. The implementation of MES system can start from data collection and monitoring. On this basis, data quality analysis and process scheduling will be effective.
2. MES system is a bridge to communicate production and management information, and plays a connecting role in enterprise information integration system. ERP system without MES will not be able to organize production quickly according to market demand. In this case, the MES system shall handle the interface with the upper ERP system.
3. Agile production is the core of advanced manufacturing mode. Traditional MES system solutions are difficult to adapt to this demand. The MES system of agile manufacturing must have good integration, compatibility, adaptability, scalability and reliability.
The construction goals of MES system in PCB assembly industry are:
1) Build a MES platform with unified basic data and system framework. Provide customized user interface, business module and secondary development. 2) According to the requirements of the lean production management mode, a MES system is developed to realize the dynamic quality control of the production process. Through the establishment of SMT assembly line production process management control model. Collect and upload information data in real time, and monitor and schedule them. It realizes the integrated information management from production task allocation, equipment management to on-site dynamic scheduling.
3) Provide dynamic quality analysis method, real-time quality problem alarm, promote the improvement of management level, and make the quality control mode transition from manual inspection to automatic processing and real-time control. Establish a quality knowledge base to promote the optimization of quality standards. Through collection, analysis, treatment and accumulation, the quality is improved.
4) Complete the integration with the existing information system of the enterprise.
According to PCB assembly industry, functional module division mainly includes data acquisition, monitoring and alarm, dynamic quality process control, process planning and scheduling, equipment management, auxiliary production site management, etc
Just upload Gerber files, BOM files and design files, and the KINGFORD team will provide a complete quotation within 24h.