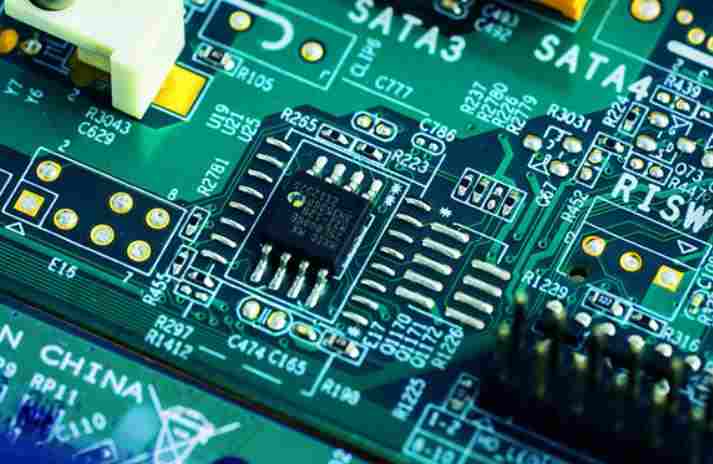
Avoid false welding of SMT automatic welding machine
How to avoid virtual welding SMT chip processing of automatic welding machine
Virtual welding means that there is only a small amount of solder at the solder joint, resulting in poor contact and always in the open and closed state. Welding refers to that the surface of the weldment is not completely tinned and the weldment is not fixed with tin. This is because the surface of the weldment is not clean, or the amount of flux is too small, and the welding time is too short. The so-called "after solder joint failure" means that the quality of solder joints on the surface is qualified, and there are no "lap welding", "half spot welding", "snap welding", "exposed copper" and other welding defects. In the workshop production process, there is no problem with the installed complete machine, but after the user has used it for a period of time, failures due to poor welding and poor conductivity often occur. This is one of the reasons for the high rate of early maintenance. This is Virtual Welding. The quality of the welding spot will seriously affect the overall quality of the potentiometer, and it must be noted that false welding is not allowed. Here, we will discuss how to control the phenomenon of SMT virtual welding in the production and processing process.
1. Wipe it frequently to keep the tip of the soldering iron clean. Since the soldering head of the energized automatic welding machine is in a high temperature state for a long time, its surface is easy to be oxidized or burned, which makes the thermal conductivity of the soldering iron worse and affects the welding quality. In this case, the impurities on the soldering iron head can be wiped with a wet cloth or sponge.
Circuit board
When the temperature is too high, you can temporarily unplug the plug or dip it in rosin to cool it, so that the soldering iron head can be properly tinned at any time
2. Notes on tin plating: If the surface of the weldment and solder joint is stained with rust, dirt or oxide, it shall be cleaned before welding so that the surface of the weldment or solder joint can be tinned.
3. The temperature PCB welding should be appropriate, not too high or too low In order to make the temperature suitable, an automatic welding machine with appropriate power should be selected according to the size of electronic components When the power of the selected automatic welding machine is constant, pay attention to controlling the length of heating time When the solder is automatically dispersed from the tip of the soldering iron to the object to be welded, it indicates that the heating time is sufficient At this time, quickly remove the tip of the soldering iron, leaving smooth solder joints in the welding area If there is almost no tin in the welding area after disassembling the automatic welding machine, this means that the heating time is too short, the temperature is not enough or the object to be welded is too dirty; If the automatic welding machine is removed, the solder will flow downward It indicates that the heating time is too long and the temperature is too high Generally, when the flux melts faster and does not smoke, the temperature control at the tip of the soldering iron is the best welding temperature
4. The amount of tin shall be moderate. The tin dipping amount of the automatic welding machine can be determined according to the size of the required solder joint, so that the solder is sufficient to cover the toughness of the solder joint and form a suitable size and smooth solder joint. Solder joints are not too much tin, and tin is better. On the contrary, this SMT solder joint is easier to weld. It may be that solder is stacked on it rather than welded on it. If the amount of tin applied at one time is insufficient, it can be repaired again, but the automatic welding machine must be removed after the previous tin is melted together; If the amount of tin coating is too much at one time, use a soldering iron to remove an appropriate amount.
5. The welding time should be well controlled and should not be too long. Proper use of welding time is also an important part of welding skills. In case of welding of printed circuit board, 2~3S is generally appropriate. If the welding time is too long, the flux in the solder will be completely volatilized, the welding function will be lost, and the solder joint surface will be oxidized, resulting in rough, black, dull, burr or flow of the solder joint surface. At the same time, if the welding time is too long and the temperature is too high, it is easy to burn the components or copper foil of the printed circuit board. If the welding time is too short and the welding temperature cannot be reached, the solder will not be completely melted, which will affect the wetting of the flux and easily lead to faulty welding.
6. During the curing process of PCB solder joints, remember not to touch the solder joints with your hands. Before the welding point is completely solidified, even a small vibration will cause deformation of the welding point and lead to false welding. This, before pulling out the iron head, the welding part should be fixed, such as using tweezers to clamp, or quickly blowing with the mouth after pulling out the iron head. The purpose of these methods is to shorten the curing time of solder joints.
7. After the welding of the solder joint is completed, the selection of the angle for pulling out the tip of the soldering iron is also particularly important. When the tip of the soldering iron is evacuated diagonally upward, a small amount of tin beads are taken away from the tip of the soldering iron to form smooth solder joints; When the soldering iron head is pulled out vertically, a welding spot with sharp burrs will be formed; When the tip of the soldering iron is level and oriented during evacuation, the tip of the soldering iron can take away most of the tin beads.
In a word, the most direct and fundamental way to avoid SMT false welding is to clean it before welding It is better not to use solder paste for cleaning, because it contains acidic substances, which may corrode the pins of electronic components in the future Welding After the oxide is removed, tin weld the SMT welding surface first, and then the welding is easy, not easy to produce false welding You should also hang the tin on the pins of the electronic components, master the welding time, and ensure the welding quality, so as to ensure the quality of the entire circuit board