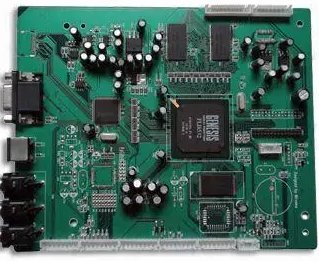
De drilling and pitting is an important process after NC drilling of rigid flex printed circuit boards and before electroless copper plating or direct copper plating. To achieve reliable electrical interconnection of rigid flex printed circuit boards, appropriate de drilling and pitting technologies must be selected based on the special material composition of rigid flex printed circuit boards and the strong alkaline resistance of polyimide and acrylic acid as the main materials. There are two kinds of technologies for drilling and pitting of rigid flex printed circuit boards: wet method technology and dry method technology. The following two PCB technologies are discussed with colleagues.
The wet drilling and pitting technology for rigid flex printed circuit boards consists of the following three steps:
1. Swelling (also called swelling treatment). The alcohol ether type swelling agent is used to soften the pore wall base material, destroy the polymer structure, and then increase the surface area that can be oxidized, so that its oxidation is easy. Butyl carbitol is generally used to swell the pore wall base material.
2. Oxidation. The purpose is to clean the hole wall and adjust the hole wall charge. At present, there are three traditional ways in China.
(1) Concentrated sulfuric acid method: because concentrated sulfuric acid has strong oxidation and water absorption, it can carbonize most of the resins and form water soluble alkyl sulfonates to remove them. The reaction formula is as follows: the effect of CmH2nOn+H2SO4 -- MC+nH2O on removing resin drilling dirt on the hole wall is related to the concentration of concentrated sulfuric acid, treatment time and solution temperature. The concentration of concentrated sulfuric acid used for removing drilling dirt shall not be less than 86%, and it shall be 20-40 seconds at room temperature. If pitting is required, the solution temperature shall be appropriately increased and the treatment time shall be extended. Concentrated sulfuric acid only works on the resin and has no effect on the glass fiber. After the hole wall is etched with concentrated sulfuric acid, there will be glass fiber heads protruding from the hole wall, which needs to be treated with fluoride (such as ammonium bifluoride or hydrofluoric acid). When fluoride is used to treat the protruding glass fiber head, the process conditions should also be controlled to prevent the wicking effect caused by the excessive corrosion of glass fiber. The general process is as follows:
H2SO4:10%
NH4HF2:5-10g/l
Temperature: 30 ℃ Time: 3-5 minutes
According to this method, the rigid flex printed circuit board after the hole is punched is de dirtied and concave etched, and then the hole is metallized. Through metallographic analysis, it is found that the inner layer is not completely dirtied, resulting in low adhesion between the copper layer and the hole wall. Therefore, when the metallographic analysis is used for thermal stress test (288 ℃, 10 ± 1s), the copper layer on the hole wall falls off, causing the inner layer to open.
Moreover, ammonium bifluoride or hydrofluoric acid are very toxic, and wastewater treatment is very difficult. What's more, polyimide is inert in concentrated sulfuric acid, so this method is not suitable for drilling and pitting of rigid flex printed circuit boards.
(2) Chromic acid method: because chromic acid has strong oxidation and strong etching ability, it can break the long chain of macromolecular substances on the hole wall, and produce oxidation and sulfonation, generating more hydrophilic groups on the surface, such as carbonyl (- C=O), hydroxyl (- OH), sulfonic acid (- SO3H), etc., so as to improve its hydrophilicity, adjust the charge on the hole wall, and achieve the purpose of removing drilling and pitting on the hole wall. The general PCB process formula is as follows:
Chromic anhydride CrO3: 400 g/l
H2SO4: 350 g/l
Temperature: 50-60 ℃ Time: 10-15min
According to this method, the rigid flex printed circuit board after drilling was de soiled and concave etched, and then the hole was metallized. The metallographic analysis and thermal stress experiment of the metallized hole were carried out, and the results fully conform to the GJB962A-32 standard.
Therefore, the chromic acid method is also suitable for drilling and pitting of rigid flex printed circuit boards. For small enterprises, this method is indeed very suitable, simple and easy to operate, and more importantly, the cost. However, the only regret of this method is the presence of the toxic substance chromic anhydride.
(3) Alkaline potassium permanganate method: At present, many PCB manufacturers still follow the drilling and pitting technology of rigid multilayer printed circuit boards -- alkaline potassium permanganate technology to treat rigid flex printed circuit boards due to the lack of professional technology. After removing resin drilling dirt, the method can also etch the resin surface to produce small uneven pits, so as to improve the adhesion between the coating on the hole wall and the substrate, Potassium permanganate is used to oxidize and remove swollen resin drilling dirt. This system is very effective for general rigid multilayer boards, but it is not suitable for rigid flex printed circuit boards. Because the main insulating substrate polyimide of rigid flex printed circuit boards is not alkali resistant, it needs to be swelled or even partially dissolved in alkaline solutions, not to mention the environment of high temperature and high alkali. If this method is adopted, even if the rigid flex printed circuit board is not scrapped at that time, the reliability of equipment using the rigid flex printed circuit board in the future will be greatly reduced.
3. Neutralization. The substrate after oxidation treatment must be cleaned to prevent contamination of the activation solution of the next process. Therefore, it must go through the neutralization and reduction process. Different neutralization and reduction solutions are selected according to different oxidation methods.
At present, the popular dry method at home and abroad is the plasma drilling and pitting technology. Plasma is used in the production of rigid flex printed circuit boards, mainly to remove drilling dirt on the hole wall and modify the hole wall surface. The reaction can be seen as a dynamic chemical reaction equilibrium process in which highly activated plasma reacts with polymer materials and glass fibers on the pore wall in gas and solid phases. The gas products generated and some unreacted particles are pumped away by vacuum pump. According to the polymer materials used for rigid printed circuit boards, N2, O2 CF4 gas is used as the original gas, in which N2 plays the role of cleaning vacuum and preheating.
The schematic formula of plasma chemical reaction of O2+CF4 mixed gas is:
O2+CF4O+OF+CO+COF+F+e-+…….
Plasma
As the electric field accelerates, it becomes a highly active particle and collides with O and F particles to produce highly active oxygen free radicals and fluorine free radicals, which react with polymer materials as follows:
[C、H、O、N]+[O+OF+CF3+CO+F+…] CO2+HF+H2O+NO2+……
The reaction between plasma and glass fiber is:
SiO2+[O+OF+CF3+CO+F+…]SiF4+CO2+CaL
So far, plasma treatment of rigid flex printed circuit board has been realized.
It is worth noting that the carbonylation reaction of atomic O with C-H and C=C increases the polar group on the polymer bond, which improves the hydrophilicity of the polymer material surface.
The rigid flex printed circuit board treated with O2+CF4 plasma and treated with O2 plasma can not only improve the wettability (hydrophilicity) of the hole wall, but also remove the reaction. After the end of the sediment and the reaction is incomplete intermediate products. After plasma technology was used to remove drilling and pitting on rigid flex printed circuit board and direct electroplating, metallographic analysis and thermal stress experiment were carried out on the metallized holes, and the results fully conform to GJB962A-32 standard.