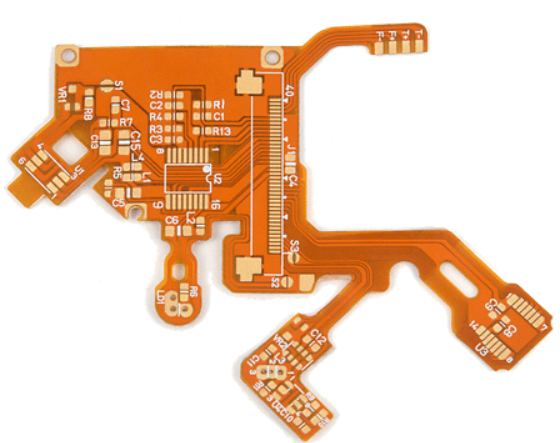
Step description
Step 1 Cut the material
This is a process that every FPC PCB production must go through. The initial cutting of the substrate is done in order to minimize excess waste. When cutting large will make excess material waste.
2. Chemical cleaning
This step is mainly to clean the oxide layer above the conductive substrate. If the copper oxide above the copper foil is not cleaned, it will produce continuous oxidation of the circuit board, which is a loss for the actual service life of the FPC circuit board.
3. Inner anticorrosive dry film (FPC flexible circuit board)
The first step is to make the line onto the film, in the use of an exposure machine to expose the line above the film attached to the corrosion resistant dry film (sensitive film) on the substrate, so that the line can be transferred to the copper foil.
Acid etching (FPC circuit etching)
When using chemical etching, it is easy to use hydrochloric acid or sulfuric acid for FPC soft plate, but it is easy to use ammonia water when etching hard lines.
5. Chemical cleaning
This step is to prevent the remaining solution from etching in the circuit, and then plasma is used to clean the FPC circuit board.
6. Inner covering film alignment
Before this step, first of all, the appearance of the soft plate covering film should be made into shape, and then the covering film and the FPC circuit board should be aligned using a soldering iron on the pad for preliminary fixation.
7. Press together
Pressing is divided into fast pressing and slow pressing. For this production process, which also requires several times of pressing, the first pressing is the use of fast pressing machine. At this time, the maximum thickness allowed after pressing will be clearly standardized in the data. After pressing, check whether there are pressing bubbles, overflow glue and other problems.
Step 8 Bake
This step is to fully combine the circuit board with the glue. The glue used between the copper foil and the covering film flows flat after baking at high temperature, which will make the combination more complete
9. Print characters on the FPC circuit board
It is also necessary to make the characters above the film onto the screen, and print the characters onto the FPC circuit board using the screen. Check whether characters are missing or underprinted.
10. Final inspection
This is a required process for all FPC boards. It is the last guarantee for FPC boards to be inspected in the production shop.
11. Flexible circuit board characteristics and advantages and disadvantages
Flexible circuit board (FPC), also known as flexible circuit board, flexible circuit board; It is short, small, light and thin. It has the characteristics of high assembly density and small volume. There are high cost, long cycle, complex inspection methods and so on.
characteristic
1. Short: short assembly time
All lines are configured. Eliminate the connection work of extra rows of wires
2. Small: smaller than PCB
Can effectively reduce the volume of the product. Increase the convenience of carrying
3, light: weight than PCB (hard board) light
It can reduce the weight of the final product
4. Thin: thinner than PCB
It can improve the softness. Strengthen the assembly of three - dimensional space in the finite space
advantage
Flexible printed circuit board is a printed circuit made of flexible insulating material, which has many advantages that rigid printed circuit board does not have:
1. It can be bent, wound and folded freely. It can be arranged arbitrarily according to the spatial layout requirements, and can be moved and expanded arbitrarily in three-dimensional space, so as to achieve the integration of component assembly and wire connection;
2. Using FPC, the volume and weight of electronic products can be greatly reduced, which is suitable for the development of electronic products to high density, miniaturization and high reliability. Therefore, FPC has been widely used in aerospace, military, mobile communications, laptops, computer peripherals, PDA, digital cameras and other fields or products.
3. FPC also has the advantages of good heat dissipation and weldability, easy installation and low comprehensive cost. The combination of soft and hard design also makes up for the slight deficiency of flexible substrate in the bearing capacity of components to a certain extent.
shortcomings
1. High one-time initial cost: Since flexible PCBS are designed and manufactured for special applications, the initial circuit design, wiring and photographic plate costs are high. Unless there is a special need to apply soft PCB, usually a small amount of application, it is best not to use;
2. It is difficult to change and repair the soft PCB: once the flexible PCB is made, the change must start from the base drawing or the compiled light drawing program, so it is not easy to change. Its surface is covered with a protective film, which must be removed before repair and restored after repair, which is a relatively difficult job.
3. Limited size: Soft PCB is usually manufactured by intermittent process in the case of not common, so it is limited by the size of production equipment, and can not be made very long and wide;
4. Improper operation is easy to damage: improper operation of the installation personnel is easy to cause damage to the soft circuit, and its tin welding and rework need to be operated by trained personnel.