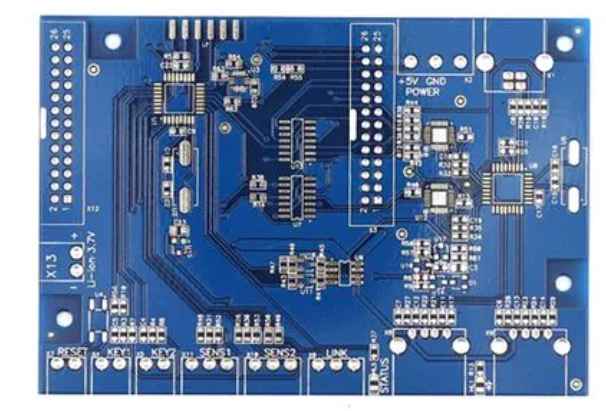
Suitable PCBA patch processing manufacturers can not only bring high quality costs for enterprises, but also bring cost-effective returns. Therefore, in the selection of PCBA patch processing manufacturers, electronics factories are very careful. So, how to choose PCBA patch processing manufacturers? Shenzhen PCBA patch processing manufacturer -kingford will start from several aspects for you to explain. The following patch processing manufacturers Xiaobian to explain how to choose PCBA patch processing manufacturers and how to deal with the relevant knowledge of PCBA processing problems.
1. How to deal with PCBA processing
Kingford focus on the high-quality PCBA order demand of " Multiple varieties, medium and small batch, and short lead time". Next, we introduce how to deal with the problem of PCBA processing tin beads tin slag. In the process of PCBA processing, due to technical and manual factors, the occasional tin beads and tin residue will inevitably appear on the PCBA board, which brings great hidden dangers to the use of products. Due to loose tin beads and tin residues in an uncertain environment, a short circuit of the PCBA board can be formed, resulting in product failure. The point is that this possibility is likely to occur throughout the product lifecycle, putting pressure on customers to sell.
The root cause of tin bead and tin slag produced by PCBA processing
1. Too much tin on the SMD pad. In the reflow welding process, the molten tin will extrude corresponding tin beads.
2. When PCB board or components are exposed to moisture, water will break in the reflow welding process, and the splashing tin beads will spread to the surface of the board;
3. During the post-soldering operation of the DIP plug-in, when manually adding tin and lifting tin, tin beads from the soldering tip will fall onto the PCBA plate;
4. Other unknown reasons.
Measures to reduce tin residue of PCBA processing tin beads
1. Pay attention to the production of steel mesh. It is necessary to adjust the opening size appropriately according to the specific component layout of PCBA board, so as to control the printing amount of solder paste. Especially if some of the foot components or panel components are dense.
2. Strict baking action is recommended for PCB bare boards with BGA, QFN and dense foot components on the board to ensure that moisture is removed from the top surface of the solder board to maximize weldability and eliminate the production of tin beads.
3. The PCBA plant will inevitably introduce the manual welder position, which requires strict control of the swing tin operation in the management. Special storage boxes are arranged, worktables are cleaned in a timely manner, and the welding and pulling quality Control Center shall perform visual inspection of the SMDS around the hand-welded components to see if the solder joints of the SMDS have been accidentally touched and dissolved or if they have been dissolved. Tin beads and tin residues are scattered between the pins of the assembly. PCBA board is a relatively complex product component, it is very sensitive to conductive objects and ESD static electricity. In the PCBA process, plant managers need to improve the level of management (IPC-A-610E Class II is recommended), enhance the quality awareness of operators and quality teams, and implement it from both process control and ideological aspects in order to minimize the production of tin beads and tin residues on the PCBA board.
kingford PCBA processing advantage
▪ SMT workshop: We have imported SMT machines and several sets of optical inspection equipment, with a daily output of 4 million. Each process is equipped with QC personnel, who can keep an eye on product quality. ▪ DIP production line: We have two wave-soldering machines, among which there are more than 10 old employees who have worked for more than three years. The skilled workers can weld all kinds of plug-in materials. 2. Quality assurance, high cost performance. High-end equipment can stick precision special-shaped parts, BGA, QFN, 0201 materials. Can also template patch, loose material hand. ▪ Sample and size batch can be produced, proofing from 800 yuan, batch 0.008 yuan/point, no start-up fee. 3. Rich experience in SMT and welding of electronic products, stable delivery. Accumulated services for thousands of electronic enterprises, involving many kinds of automotive equipment and industrial control motherboard SMT processing services, products are often exported to Europe and the United States, quality can be affirmed by new and old customers. ▪ On time delivery, normal 3-5 days after complete materials, small batch can also be expedited on the same day shipment. 4. Strong maintenance ability, perfect after-sales service ▪ Experienced maintenance engineers, can repair all kinds of patch welding caused by bad products, to ensure the connection rate of each piece of circuit board. ▪ 24-hour customer service staff at any time response, the fastest speed to solve your order problems.
2. How to select PCBA patch manufacturer
First, customer experience
Good word-of-mouth is a necessary factor for the sustainable development of PCBA patch processing manufacturers. When choosing manufacturers, we must investigate the word-of-mouth of manufacturers to see whether it is reliable and trustworthy. And there are many ways to investigate, website, offline can. In addition, also pay attention to the relevant information of the company, see if there is negative news, etc., these are important factors to judge whether a PCBA patch processing manufacturer is reliable. In addition, if you can directly consult the manufacturer's website quotation and order, then, its credibility will increase some.
Ii. Production qualification
The production qualification of PCBA patch processing plant is reflected in many aspects, such as whether there is ISO9001 quality management system certification, whether there is the United States UL certification, whether there is the European Union ROHS related production requirements, which are the important basis to judge its qualification. In addition, through the past cooperation objects and cooperation cases, we can also see whether the production is qualified, whether the quality.
Iii. Cost
Now, the patch market competition is also very fierce, some PCBA patch manufacturers in order to attract customers, will use low price preferential policies to promote. These preferential policies seem to be much cheaper on the surface, but it may be the price of quality, for enterprises, more than worth the loss. You know, high quality products bring not only the use of products, but also the reputation of customers. Moreover, the decrease in cost means that the input must be reduced in some aspects, which may reduce its quality and affect its future development. Therefore, when a PCBA patch manufacturer wants to attract you with a low price, be careful.
Iv. Service
Strong PCBA patch processing manufacturers will provide customers with perfect service, including pre-sale, sale and after-sales, every link can let customers feel the most intimate service. Therefore, when judging whether PCBA patch processing manufacturers are reliable, we can start from the service. For example, before sales, whether the reliable manufacturers have the ability to make appropriate solutions for customer needs, during sales, whether they can quickly solve the problems encountered by customers, after sales, whether they can provide timely and professional services. When customers have questions, whether the manufacturer can carefully answer and solve customers' doubts and difficulties, strengthen customer trust, whether to respond in time, to give customers strong technical support. The above four perspectives are the important basis for selecting PCBA patch processing manufacturers. In addition, product quality, technical support, value creation, etc., can be used to judge whether PCBA patch processing manufacturers are worth cooperating with. Here, also remind the enterprise choice must be careful.