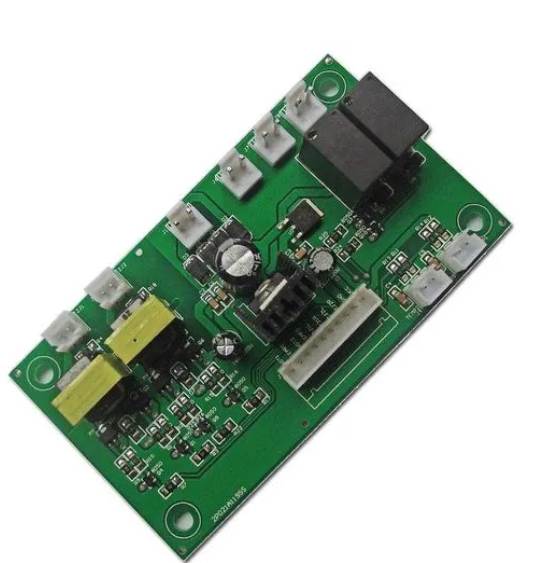
What are the types of SMT patch processing paste? In the smt patch processing process, the solder paste will often be used, but there are various types of solder paste, which is the need to choose the solder paste according to the processed products. Below, the patch processing manufacturer will tell you what problems will be caused by PCB processing and what solder paste related knowledge of SMT patch processing.
1. What are the solder paste for SMT patch processing
First, there are lead solder paste and lead-free solder paste
Lead solder paste contains lead, which is harmful to the environment and human body, but the welding effect is good, the cost is low, and it can be used in some electronic products without requirements for environmental protection. Lead-free solder paste ingredients only contain trace amounts of lead, small harm to human body, belong to environmental products, used in environmental protection electronic products, foreign customers will require the use of lead-free solder paste for production.
Two, high temperature solder paste, medium temperature solder paste, low temperature solder paste
1, high temperature solder paste, refers to the usually used lead-free solder paste, the melting point is generally above 217℃, good welding effect.
2. Medium temperature tin paste, commonly used lead-free medium temperature tin paste melting point is about 170℃, medium temperature tin paste is mainly characterized by the use of imported special rosin, good adhesion, can effectively prevent collapse.
3. The melting point of low-temperature solder paste is 138℃, and the low-temperature solder paste is mainly composed of bismuth. When the components of the patch cannot withstand the temperature of 200℃ or above and the patch reflux process is required, the low-temperature solder paste is used for welding process to protect the parts and PCB that cannot withstand the high-temperature reflow welding, which is very popular in the LED industry.
Three, tin powder particle size
According to the particle diameter of tin powder, tin paste can be divided into 1, 2, 3, 4, 5, 6 grades of tin paste, of which 3, 4, 5 powder is more commonly used. The more sophisticated the product, the smaller the tin powder needs to be, but the smaller the tin powder, it will correspondingly increase the oxidation area of the tin powder. In addition, the shape of tin powder is round, which is conducive to improving the quality of printing. The higher the difficulty of SMT patch processing products, the more important the selection of solder paste, solder paste suitable for product requirements can effectively reduce the solder paste printing quality defects, improve the quality of reflow welding, and reduce the cost of production.
2. What problems will be caused by PCB processing
Surface treatment: Major process issues (including coating process)
(1) welding resistance (a more difficult than a welding, the third time is more difficult to weld, the fourth is usually unable to weld). (2) wave soldering solder penetration is poor. (3) copper welding spot. "Black plate", "gold crisp".
(1) soldering flux edge copper wire of Giovanni concave serious consequences (=1/3 wire width), can not heavy industry. (2) easily corroded by acid gas; Sensitive to hand marks; Ag migration.
(1) Continuous production of Cu6Sn5 by Sn and Cu affects the storage life. (2) Producing tin whiskers. (3) Low process efficiency, at the same time, long process time (10min), high temperature (70℃), serious damage to the flux resistance, especially the fine lines. Best weldability, long storage life, but not suitable for dense foot devices.
(1) The coating thickness, except ENIG, is not specified in the relevant IPC standards, and it can meet the weldability requirements. The general requirements of the industry are as follows. OSP:0.15~ 0.5um, IPC does not specify, 0.3 ~ 0.4um is recommended. EING:Ni- 3~ Sum; Au-0.05~ 0.20um (IPC only specifies the thinnest requirements). Im-Ag:0.05~ 0.20um, the thicker the erosion, the more serious (IPC does not stipulate). Im-Sn: ≥0.08um, the thickness is expected to be thicker, mainly because Sn and Cu will continuously generate Cu6Sn5 at room temperature, which affects the weldability. HASL Sn63Pb37, usually formed naturally between 1 ~ 25um, is difficult to grasp accurately in pcb surface treatment technology; And lead-free SnCu alloy is mainly used, due to high processing temperature, easy to form Cu3Sn affect the poor weldability, basically not used at present. (2) Wettability of SAC387 (wetting time under different furnace times, unit :s). 0 times :Im-Sn(2)-EING(1.2),OSP(1.2)-Im-Ag(3). 2 times :EING(3), Eing (3)-OSP(7)-Im-Sn(8). 4 times :EING(3)-lm-Ag(4.3)-OSP(10)-Im.Sn(10). (3) Wetting force on SAC305 (after two passes). It is EING(5.1)-Im-Ag (4.5) -Im-Sn (1.5)-0SP(0.3). The PCB board surface treatment acts as a pre-welding protection against oxidation, and is fused into the solder during welding, so that corrosion resistance is not generally of concern. However, if you want to betray the quality of surface treatment process, you must know its corrosion resistance. Under the condition of conventional salt spray test, OSP, Im-Ag and ENIG have poor salt spray resistance. Only the surface treated with Im-Sn is better, and no obvious corrosion phenomenon is observed.