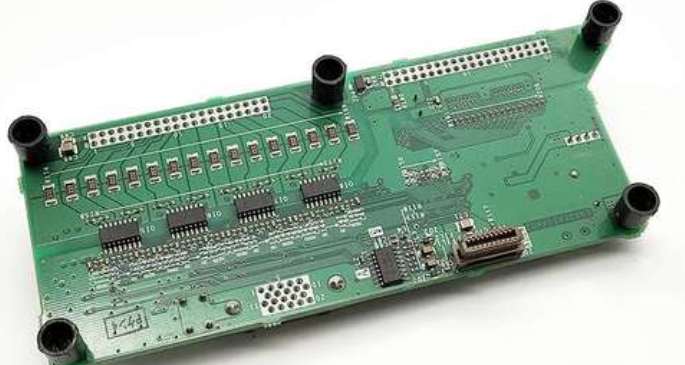
1. To ensure the assembly quality, we should pay attention to the printing process, which is a very important step in kingford patch processing plant. If this step is done, the product quality will be no problem. So, what are the requirements of kingford patch processing plant for the printing solder paste process?
First, the requirements of welding paste
Industry insiders said that patch processing in the welding paste, there are four main requirements:
1. It has to be even
In order to ensure that the solder paste pattern is clear, it is necessary to ensure that when the solder paste is applied, the amount of the solder paste is uniform and consistent, and the two adjacent figures can not be welded. At the same time, the graphics of the solder paste should be consistent with the graphics on the pad, and no dislocation can occur.
2. The amount of welding paste is different
Under normal circumstances, the amount of solder paste on the pad should be 0.8mg/mm2. For components with short spacing, it is about 0.5mg. The actual amount of paste needs to be controlled according to the thickness of the actual operation template and the size of the opening.
3. Deviation
In patch processing, it is not necessary to ensure that there is no deviation. In contrast, the weight of the solder paste at the time of printing the PCB board can be different from the weight determined at the beginning of the design. This is mainly because the pad is not the same, the coverage area of the solder paste is not the same, so a certain deviation will be allowed, but the deviation value cannot be too large.
4. Ensure no collapse and neat edges
Guanlan patch processing industry emphasized that after welding paste printing, it is necessary to ensure that there is no particularly serious collapse, and the edge should be guaranteed to melt together. In addition, the dislocation should not exceed 0.2mm, and the dislocation of the welding pad with narrow spacing should not exceed 0.1mm. In addition, the PCB circuit board can not be contaminated by solder paste, so after operation, must be cleaned with tin belt.
Two, how to check whether it is qualified
If you want to know whether the printing solder paste process is qualified, you can use visual inspection. kingford patch processing manufacturers said that visual detection is one of the best ways to ensure accuracy. In the process of eye inspection, magnifying glass will be used, usually 2-5 times or 3-20 times of the microscope, according to the requirements of the circuit board product to choose the appropriate detection tools.
3. What are the testing standards?
The final inspection standards are set in accordance with industry standards, such as IPC standards or SJ/T10670-1995 General Technical Requirements for surface Assembly process, which can be found on the Internet.
Nowadays, in the process of patch processing, the most problems are printing solder paste. Especially, the position of printing, the amount of solder paste, whether uniform, whether clear graphics, whether adhesion, whether the surface is sticky and so on May become the influencing factors. Therefore, special attention should be paid to the printing solder paste this step.
2. Environmental requirements for the production line of smt processing plant
Why do many electronic enterprises prefer to spend money to find smt manufacturers, rather than their own processing and production? The reason is very simple. smt production line has high requirements on many factors. Take temperature and humidity in the workshop as an example. Therefore, it is difficult for ordinary electronics factories to spend money to create such an environment.
In fact, there is a very simple introduction to the SMT patch processing industry, that is, the capacitor or resistor on the electronic products are pasted on the special equipment, and then welded, so that the components are more firm, will not fall, will not shift. After high-tech processing out of the circuit board efficiency is much faster than manual installation, and the error rate is low, so relative to their own production, electronic enterprises want to complete the production by SMT manufacturers. So, what are the environmental requirements of the smt production line? Industry insiders say that smt production lines have different temperature and humidity requirements.
First, temperature requirements
Under normal circumstances, the workshop temperature of smt production line must be kept at about 23 degrees, with the lowest not lower than 15 degrees and the highest not more than 35 degrees. Only in this range of circuit boards produced, the quality is the best.
Two, humidity requirements
Humidity has a great impact on the quality of products, the higher the humidity, the more susceptible to moisture electronic components, the worse the quality. If the air is too dry, static electricity will also be generated. Therefore, humidity must be guaranteed in smt production line, and the constant humidity ratio is about 40 percent. Operators should also pay attention to wear anti-static clothing, so as to avoid electrostatic reactions.
Three, cleanliness requirements
As a matter of fact, smt production line has a high requirement on cleanliness. The workshop must be free from any smell and dust, and the interior must be kept clean and tidy without corrosive materials or dirt. Otherwise, the production efficiency will be affected, and the fault maintenance rate of products will be increased, which will lead to production failure.
Four, power supply stability requirements
According to industry insiders, power supply stability has a great impact on processing quality and progress, so in order to avoid equipment failure during processing, on the smt line, it is necessary to have a voltage regulator to ensure the stability of the power supply.
After reading these four points, I believe you have a good understanding of the environmental requirements of the smt production line.
In fact, it can be seen from these four points that the smt production line has a little harsh requirements on the environment. After all, there are very few workshops that can achieve complete dust-free, odorless, moderate dry humidity and appropriate temperature. Unless they are professional workshops, they are difficult to maintain. This is one of the reasons why electronics companies cannot produce their own products. Because the creation of these equipment and workshops requires a large amount of manpower and financial input, and maintenance costs are also high. For electronic enterprises, it is better to hand over to professional smt manufacturers than to produce by themselves, which is more economical and convenient