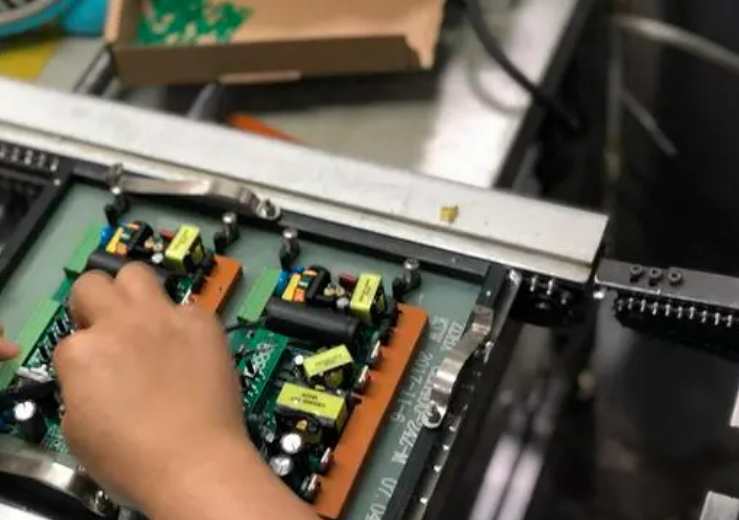
Combined with years of PCBA assembly production technology management experience for R & D enterprise design personnel, on the basic knowledge of SMT process to do a popularization and talk about the industrialization of the current R & D enterprise system class veneer road, market trends have shown that mobile phones have been Apple, Xiaomi, Huawei and other giants divided 80% of the share, So the original many SMT processing enterprises began to transform into all kinds of other needs processing veneer, and the characteristics of this kind of demand is destined to be customized system class veneer, this and the original mobile phone motherboard production has an essential difference, mobile phone requirements are mass intensive production, the process decided only need SMT segment process can complete the assembly, And R & D veneer is small batch distributed production, in addition to SMT process, after the section also needs THT and even manual welding, crimping, gluing coating, etc., the process is more complex.
The following is a flow chart of finished system veneer processing:
In a nutshell, the key process is: SMT- THT/ hand welding - test - three anti paint, among which the highest technical content of typical R & D type factory SMT process introduction:
I. Material distribution: intelligent warehouse management system scheme
Intelligent warehouse management system will use the combination of electronic intelligent manufacturing management and warehouse management information modernization, lean production (JIT) as the theoretical basis, Through database technology, image identification technology, bar code technology, electronic shelf lighting technology, API technology (application program interface), OLAP technology (online transaction processing) and the corresponding communication mechanism and external system docking integration, the warehouse process and operation information can be effectively managed.
Overall flow chart of the system:
Technical features:
1. PO Receiving without bar code: take the initiative to obtain PO information from ERP, receive materials automatically through AOS (automatic recognition by camera)/ manual, check the information related to materials and PO, and generate Reel ID by the system after checking, and print material labels.
2. Receiving goods with barcode PO: UPN information import is supported. Scan UPN information to check information related to materials and delivery notes.
3. IQC inspection: interconnect with LCR and other inspection equipment, generate inspection report after completion of inspection, and exchange the inspection results to ERP automatically. After completion of inspection, batch to be stored and batch to be returned will be generated automatically according to the inspection result.
4. Raw material warehousing: Select the corresponding batch list to be warehousing, scan the reel id, and complete warehousing according to the recommended rules (storage space/electronic shelf storage space). After storage, it can carry out supplementary printing (Bluetooth printing, network printing), splitting, merging, inventory, storage adjustment operations (support single material, whole storage operations). At the same time, conduct early warning management of the warehouse (warehouse age, overdue, sluggish materials, etc.).
5. Pull-out management: according to the system pull-out order, use PDA to select the pull-out order number, and pull the material from the raw material warehouse to the corresponding area (line warehouse, workshop, etc.); The system automatically lights up according to the principle of FIFO, and warehouse personnel issue materials according to the visual lighting reminder (support multi-order operation). Electronic shelf:
6, miscellaneous: for special reasons to lend (samples, maintenance, testing, etc.) miscellaneous operations. Electronic shelf according to the rules of light prompt material. When materials are returned, the remaining quantity is updated and stored.
7. Line storage: Select the corresponding batch list to be stored, scan the reel id, and complete the storage according to the recommended rules (storage space/electronic shelf storage space). After storage, it can carry out supplementary printing (Bluetooth printing, network printing), splitting, merging, inventory, storage adjustment operations (support single material, whole storage operations), etc.
8. Wire warehouse material delivery: According to the planned start time of work order, the system will generate early warning for the first set of material preparation of work order in advance (time can be configured freely). Use PDA to select the number of work order, according to the electronic shelf material reminder, work order LPM material distribution (support positive and negative combination of material distribution), support electronic material rack car material distribution, support in accordance with the station table sorting material distribution and partition reminder.
9. Material return: Material return with automatic counting machine to complete the material return operation.
10. Return goods: return goods according to PO or account alias.
11, inventory: cycle inventory, regular inventory, custom inventory.
12. LPM (low warning) material delivery: WMS system passes MES system (the premise is that MES must provide interface)
Low Kanban warning is generated by docking. PDA is used to select the work order number and LPM materials can be issued.
13. Special material management: special process control for solder paste and humidity sensitive parts.
14. Scrapping operation: scrapping application, scrapping appraisal, scrapping warehouse, and processing by renewable resource manufacturers are carried out for scrapping products
The process.
15, special operations: logistics transmission belt, automatic scanning code buckle operation.
16. Permission management: It can control the permission of separate warehouse. Non-warehouse personnel cannot operate the warehouse.
17, ERP interface: warehouse information automatic interaction ERP, can set whether to update ERP inventory.
Two, substrate marking: laser coding
Laser marking technology, as a modern precision machining method, has unparalleled advantages compared with traditional machining methods such as machine labeling, manual labeling, inkjet coding and printing.
1, the use of laser processing means, and no processing force between the marking parts, with the advantages of no contact, to ensure the invisible change and damage of PCB or components. At the same time, it has wide adaptability to materials, and can make very fine marks on the surface of a variety of materials with very good durability.
2, laser space control and time control is very good, marking object material, shape, size and processing environment of freedom are very large, especially suitable for automatic marking and special surface marking. And the processing mode is flexible, can not only adapt to the needs of laboratory type individual design, but also can meet the requirements of industrial mass production.
3, laser marking fine lines can reach millimeter to micron magnitude, using laser marking technology to make mark imitation and change are very difficult, very important for product security.
4, laser processing system combined with FA industrial control technology can constitute efficient automatic processing equipment, can type a variety of words, symbols and patterns, easy to use software design marking pattern, change the marking content, to meet the requirements of modern production high efficiency, fast pace.
5, laser processing and traditional labeling/coding compared, no pollution sources/consumables, is a clean and pollution-free processing technology.