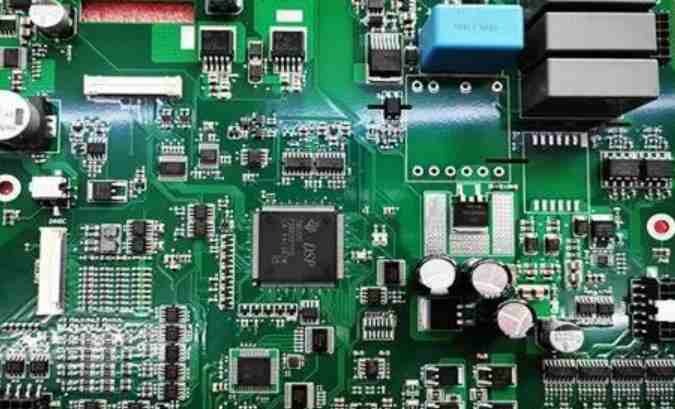
By virtue of its strong technical strength, services, strict knowledge product protection measures and good business reputation, and relying on the perfect Internet trading platform, Fanyi has quickly become an important partner and support recognized by domestic and first-class enterprises. So far, Fanyi has expanded its business to the United States, India, Taiwan, Hong Kong and other regions and regions, and obtained Tensorcom, MR.LOOP, Ubilite, spChips and other nearly 100 foreign enterprises.
At present, there are many domestic PCB proofing factories, and customers often do not know how to choose when looking for a factory. What conditions should a good PCB proofing factory have, and how to consider PCB proofing factory? And so on, we will briefly introduce how to select the PCB proofing factory.
1. Pay attention to whether the factory information is true
In the Internet era, there is also a lot of information about PCB proofing factories on the Internet. When looking for PCB proofing factories, we should pay attention to the authenticity of information. There are many small workshops on the Internet that boast their own strength into large-scale and high-tech strength manufacturers, but in fact, there are indeed three workshops. In addition to searching information on the Internet, it is best to visit the factory, see the factory environment and assembly line, so as to choose the right manufacturer according to their own eyes.
2. Beware of price traps
The price is PCB proofing processing is a problem that most customers are more concerned about, due to regional issues, many customers are in the merchants for online pricing of PCB, formal manufacturers will have online quotation system, customers in the custom PCB proofing, do not cohabit cheap, so as not to customize the product quality is not up to the price.
3. Look at PCB proofing factory services
Good PCB proofing factory, of course, need to have good service. PCB proofing factory purchase needs to involve many issues, such as product process, product use, product warranty, etc., need to have a perfect service system. And the pre-sale service we can communicate with the manufacturer to see whether we can give customers detailed product introduction, whether we can be patient and solve customer problems. After-sales service is to see whether the manufacturer can provide package return, warranty, technology and other problems that may be encountered in the later period.
4. Pay attention to previous cooperation cases of PCB proofing factories
The strength of PCB proofing factory can often be reflected in its past cooperation customers. If many enterprises seek cooperation with this factory, its strength is not to be underestimated. The output and quality are relatively high.
Look for PCB proofing custom manufacturers, Fanyi PCB proofing factory! Fanyi has a series of features such as independent PCB online ordering, CRM management system, online self-quotation, self-ordering, online payment, online query of production schedule, express tracking and so on. Fanyi PCB proofing is a possible choice!
(1) Visual inspection Visual inspection is the use of human eyes to carry out some simple inspection, such as surface dents, pits, scratches, etc. * It is important to check whether the weld hole is in the center of the pad and the integrity of the wire pattern.
(2) Connectivity through holes For multi-layer circuit boards to conduct connectivity tests, the purpose is to find out whether the PCB graphics have connectivity.
(3) Insulation resistance of the circuit board Insulation resistance is a resistance of the printed circuit board insulation components to the external DC voltage. Choose two or more wires with close spacing and insulation, first measure the insulation resistance between them, after humidifying and heating for a period (the relative humidity in the box is about 45 degrees Celsius, 10 hours to two days), put them in the room for one hour, and then measure the insulation resistance between them.
(4) Weldability of welding pad Weldability is used to measure the wetting ability of solder on printed graphics when components are welded to the printed circuit board, which is generally expressed by wetting, semi-wetting and non-wetting. When wet, the solder can flow and expand freely on the wire and pad to form adhesive connection. Semi-wetting, the solder first wets the surface of the pad, and then forms the solder ball in some irregular places of the pad because of improper wetting. Without wetting, the solder accumulates on the surface, but does not form an adhesive connection to the pad surface.