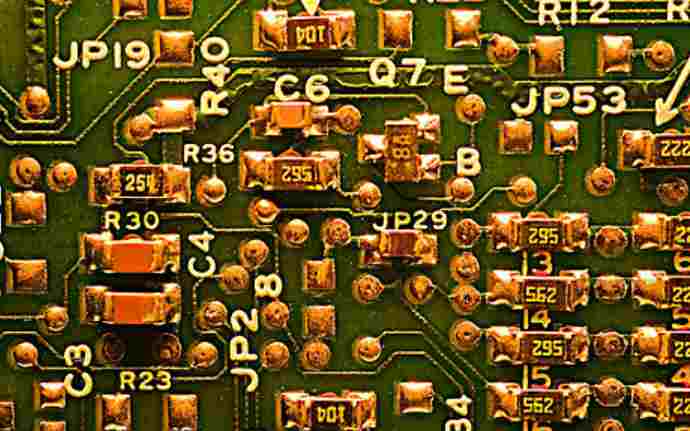
When we use electronic equipment, we often find that after continuous use for a period of time, the electronic equipment will generate a certain amount of heat, so that the internal temperature of the equipment will rise rapidly. If the heat is not dissipated in time, the equipment will continue to heat up, and the devices will fail due to overheating, and the reliable performance of the electronic equipment will decline.
Therefore, it is very important to have a good heat dissipation treatment on the circuit board. The heat dissipation of PCB circuit board is a very important link, so how to heat dissipation of circuit board, let's discuss the next.
1, high heating device with radiator, heat conduction plate
When there are a few (less than 3) PCB components with high heat, heat sinks or heat conduction tubes can be added to the heating components. If the temperature still cannot be lowered, we can use a radiator with a fan to enhance the heat dissipation effect.
When the amount of heating device is more (more than 3), you can use a large radiator (plate), it is according to the position and height of the heating device on the circuit board and customized special radiator or in a large plate radiator cut out different components of the high and low position. The radiator cover is fastened on the component surface as a whole, and contact with each component to dissipate heat. But because the components are installed and welded at different levels, the heat dissipation effect is not good. Soft thermal phase change pads are usually added on the surface of components to improve the heat dissipation effect.
2, through the circuit board itself heat dissipation
At present, the widely used circuit board substrate is copper coated/epoxy glass cloth substrate or phenolic resin glass cloth substrate, and a small amount of paper coated copper plate.
Although these substrates have excellent electrical properties and processing properties, but the heat dissipation is relatively poor, as a heat dissipation way of high heating components, almost can not be expected from the PCB resin heat conduction, but from the surface of the components to the surrounding air heat dissipation.
However, as electronic products have been more and more inclined to component miniaturization, high-density installation, high thermal assembly, if only rely on the surface of a very small surface area to dissipate heat is far from enough.
And because a large number of surface mounted components such as QFP and BGA are used, the heat generated by components is largely transmitted to the circuit board. Therefore, the best way to solve the heat dissipation is to improve the heat dissipation capacity of the PCB directly in contact with the heating component, through the circuit board conduction or emission.
3, the use of reasonable cable design to achieve heat dissipation function
Because the resin in the plate has poor thermal conductivity, and the copper foil line and hole are excellent conductors of heat, so improving the copper foil residual rate and increasing the heat conduction hole is the main means of heat dissipation.
If the heat dissipation capacity of a PCB is to be evaluated, the equivalent thermal conductivity (9EQ) of the insulating substrate for PCB, which is composed of various materials with different thermal conductivity, is calculated.
4. For the use of free convection air cooling equipment, it is best to arrange integrated circuits (or other devices) by the length of the way, or by the length of the way.
5. The devices on the same printed circuit board should be arranged as far as possible according to their calorific value and heat dissipation degree. Devices with small calorific value or poor heat resistance (such as small signal transistors, small-scale integrated circuits, electrolytic capacitors, etc.) should be placed at the upper stream of the cooling air flow (entrance). Devices with high calorific value or good heat resistance (such as power transistors, large-scale integrated circuits, etc.) are placed at the downstream of the cooling flow.
6. In the horizontal direction, the high-power devices are arranged near the edge of the printed circuit board as far as possible, so as to shorten the path of heat transfer; In the vertical direction, the high-power components should be placed close to the printed circuit board as far as possible, so as to reduce the temperature that affects other components when these components work.
7, it is best to place the temperature sensitive device in the lowest temperature area (such as the bottom of the equipment), do not put it above the heating device, multiple devices are best in the horizontal staggered layout.
8, the heat dissipation of the printed circuit board in the equipment mainly depends on the air flow, so in the design to study the air flow path, reasonable configuration of devices or printed circuit boards. Air flow always tends to flow where the resistance is low, so when configuring components on the printed circuit board, avoid leaving a large area of airspace. The configuration of multiple printed circuit boards in the whole machine should also pay attention to the same problem.
9. Avoid the concentration of hot spots on the PCB circuit board, distribute the power evenly on the circuit board as far as possible, and maintain the uniform and consistent temperature performance of the PCB circuit board surface. Often in the design process to achieve strict uniform distribution is more difficult, but we must avoid the power density is too high in the area, in order to prevent the occurrence of hot spots to affect the normal operation of the entire circuit. If conditions are available, it is necessary to carry out thermal performance analysis of printed circuits. For example, the thermal performance index analysis software module added in some professional PCB design software can help designers improve circuit design.
10. Arrange the components with the highest power consumption and maximum heat dissipation near the optimal location for heat dissipation. Do not place high heating components in the corners and edges of the printed circuit board, unless there is a cooling device arranged near it. In the design of the power resistance as far as possible to select some large components, and adjust the layout of the printed circuit board so that it has enough space for heat dissipation.
11, high heat dissipation components in connection with the substrate should be able to reduce the thermal resistance between them. To better meet the requirements of thermal characteristics, use some thermal conductive materials (such as a layer of heat-conducting silicone) on the bottom surface of the chip, and keep a certain contact area for heat dissipation.
12. Connection between components and substrate:
(1) Shorten the lead length of components as much as possible;
(2) When selecting high-power components, the thermal conductivity of lead materials should be taken into account. If possible, the largest lead transverse surface should be selected as far as possible;
(3) Select the components with more pins.
13. Encapsulation selection of components:
(1) In consideration of thermal design, attention should be paid to the package description of components and its thermal conductivity;
(2) Consideration should be given to providing a good heat conduction path between the substrate and component package;
(3) In the heat conduction path to avoid air partition, if there is such a case can be used to fill thermal materials.