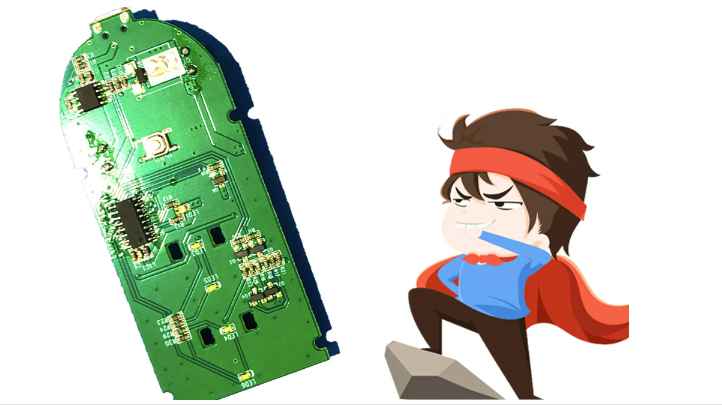
When the circuit board is reflow welding, it is easy to bend the plate and warped the plate. If it is serious, it will even cause the element air welding and erect the tablet. How to overcome it?
1, PCB circuit board deformation harm
On the automatic surface mounting line, if the circuit board is uneven, it will cause inaccurate positioning, and the components cannot be inserted or affixed to the holes of the board and the surface mounting pad, or even crash the automatic inserting machine. The circuit board on which the components are installed is bent after welding, and it is difficult to cut the feet of the components neatly. The board can not be installed into the chassis or machine socket, so the assembly plant encountered the board is also very troublesome. At present, the surface mounting technology is developing towards the direction of high precision, high speed and intelligence, which puts forward higher requirements for the smoothness of PCB board as the home of various components.
It is specified in the IPC standard that the maximum allowable deformation of PCB board with surface mount is 0.75%, and the maximum allowable deformation of PCB board without surface mount is 1.5%. In fact, in order to meet the needs of high precision and high speed mounting, some electronic mounting manufacturers have stricter requirements on the amount of deformation, such as our company has a number of customers to allow the maximum deformation of 0.5%, and even some individual customers require 0.3%.
PCB board is composed of copper foil, resin, glass cloth and other materials, the physical and chemical properties of each material are different, after pressing together will inevitably produce thermal stress residual, resulting in deformation. At the same time, in the process of PCB processing, it will go through various processes such as high temperature, mechanical cutting and wet treatment, which will also have an important impact on the deformation of the board. In short, the causes of PCB board deformation are complex and diverse. How to reduce or eliminate the deformation caused by different material characteristics or processing has become one of the most complex problems faced by PCB manufacturers.
2. Cause analysis of deformation
The deformation of PCB board needs to be studied from several aspects, such as material, structure, graphic distribution, processing process, etc. This paper will analyze and elaborate various causes of deformation and improvement methods.
The copper surface area on the circuit board is uneven, which will worsen the bending and warping of the board.
Generally, a large area of copper foil will be designed on the circuit board for grounding. Sometimes, Vcc layer will also be designed with a large area of copper foil. When these large areas of copper foil are not evenly distributed on the same circuit board, it will cause the problem of uneven heat absorption and heat dissipation speed. If the expansion and contraction cannot be done at the same time, it will cause deformation under different stresses. At this time, if the temperature of the board has reached the upper limit of Tg value, the board will begin to soften, resulting in permanent deformation.
Connecting points (vias) between the layers of the board limit board growth and shrinkage
Most of today's circuit boards are multilayer boards, and there will be rivets between layers of connection points (vias), and the connecting points are divided into through holes, blind holes and buried holes, where the connecting points will limit the effect of cooling and shrinkage of the board, but also indirectly cause the bending and bending of the board.
Cause and improvement of PCB deformation
The weight of the board itself can cause the board to sag and deform
General back welding furnace will use the chain to drive the circuit board forward in the back welding furnace, that is, to both sides of the board when the fulcrum to prop up the whole board, if the board above the excess parts, or the size of the board is too large, it will be due to its own kind of amount and show the middle depression phenomenon, resulting in bending.
The depth of V-Cut and the connection strip will affect the deformation of the plate
Basically, V-Cut is the culprit of damaging the structure of the board, because V-Cut is in the original a large sheet of the board to cut out grooves, so the V-Cut place is prone to deformation.
Cause and improvement of PCB deformation
2.1 Sound analysis of sheet deformation caused by compacted materials, structure and graphics
PCB board is made of core board, semi-cured sheet and outer copper foil pressed together. The core board and copper foil are deformed by heat when pressed together. The deformation depends on the coefficient of thermal expansion (CTE) of the two materials.
The thermal expansion coefficient (CTE) of copper foil is about 17X10-6.
The z-direction CTE of common FR-4 substrate is (50~70) X10-6 at Tg point.
Above TG point is (250~350) X10-6, and x-direction CTE is generally similar to copper foil due to the existence of glass cloth.
A note on TG points:
When the temperature of high Tg printed board rises to a certain area, the substrate will change from "glass state" to "rubber state", and the temperature at this time is called the glass transition temperature (Tg) of the board. That is, Tg is the highest temperature (° C) at which the substrate remains rigid. That is to say, ordinary PCB substrate materials at high temperature, not only produce softening, deformation, melting and other phenomena, but also show a sharp decline in mechanical and electrical characteristics.
The plate of general Tg is more than 130 degrees, the high Tg is generally more than 170 degrees, and the medium Tg is about more than 150 degrees.
Usually Tg≥170℃ PCB printed board, called high Tg printed board.
With the increase of Tg of the substrate, the characteristics of heat resistance, moisture resistance, chemical resistance and stability of the printed board will be enhanced and improved. The higher the TG value, the better the temperature resistance of the plate, especially in the lead-free process, high Tg is often used.