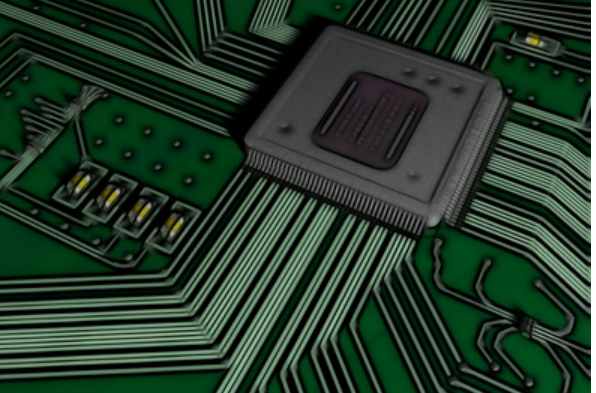
When drawing component packaging in PCB, it is often difficult to grasp the size of the pad, because the data we refer to gives the size of the component itself, such as pin width, spacing, etc., but the corresponding pad size on PCB board should be slightly larger than the size of the pin, otherwise the reliability of welding cannot be guaranteed. The following will mainly describe the specification of pad size.
In order to ensure the welding quality of SMT components (SMT), in the design of SMT printed board, in addition to the printed board should be set aside 3mm-8mm process edge, according to the relevant specifications of the design of various components of the welding pad graphics and dimensions, layout of components orientation and spacing between adjacent components, we believe that special attention should be paid to the following points:
(1) On the printed board, where conductive graphics (such as interconnects, ground wires, mutual guide holes, etc.) and copper foil required to be retained are located under the solder resistance film, bare copper foil shall be used. That is, do not allow plating metal coating whose melting point is lower than the welding temperature, such as tin lead alloy, so as to avoid causing crack or wrinkle of welding resistance film located in the coating, so as to ensure the welding and appearance quality of PCB board.
(2) When selecting or calling the welding pad graphic size data, it should match the package shape, welding end, pin and other welding related dimensions of the components it chooses. It is necessary to overcome the bad habit of copying or invoking the graph dimensions of the pads in the data or software library without analysis or comparison. When designing, selecting or calling the welding pad graphic size, you should also distinguish the components you selected, their code (such as sheet resistance, capacitance) and the size related to welding (such as SOIC,QFP, etc.).
(3) The welding reliability of surface mount components mainly depends on the length of the pad rather than the width.
(a) As shown in Figure 1, the length of the pad B is equal to the length T of the weld end (or pin), plus the extension length b1 of the inside of the weld end (or pin) (pad), plus the extension length b2 of the outside of the weld end (or pin) (pad), i.e. B=T+b1+b2. The length of b1 (about 0.05mm -- 0.6mm), not only should be conducive to the solder melting can form a good crescent profile solder joint, but also to avoid the solder bridge phenomenon and take into account the components of the mounting deviation is appropriate; The length of b2 (about 0.25mm -- 1.5mm), mainly to ensure that the formation of the best meniscus profile of the solder joint is appropriate (for SOIC, QFP and other devices should also take into account the anti-stripping ability of the pad)
(b) The width of the pad shall be equal to or slightly greater (or less) than the width of the weld end (or pin).
Common mounting components pad design diagram, as shown below.
Pad length B=T+b1+b2
Spacing inside pad G=L-2T-2b1
Pad width A=W+K
Outer spacing of pad D=G+2B.
Where: L -- length of the component (or distance between the outer sides of the device pins);
W -- component width (or device pin width);
H -- component thickness (or device pin thickness);
b1 -- Extension length of the inner side of the welding end (or pin) (pad);
b2 -- the extension length of the outside (pad) of the welding end (or pin);
K -- Correction amount of pad width.
Typical values of pad extension length for common components:
For rectangular sheet resistor and capacitor:
B1 = 0.05 mm, 0.10 mm, 0.15 mm, 0.20 mm, 0.30 mm one of them, the shorter the element length of the value should be smaller.
B2 = 0.25 mm, 0.35 mm, 0.5 mm, 0.60 mm, 0.90 mm, 1.00 mm, the thickness of the element of the thinner, the value should be smaller.
K=0mm,+-0.10mm,0.20mm one of them, the narrower the width of the component, the smaller the value should be taken.
For SOIC and QFP devices with airfoil pins:
B1 = 0.30 mm, 0.40 mm, 0.50 mm, 0.60 mm one, device appearance outsiders, or adjacent pin center distance outsiders, take the value should be smaller.
B2 = 0.30 mm, 0.40 mm, 0.80 mm, 1.00 mm, 1.50 mm one of components supplied by appearance, have thrown some value.
K = 0 mm, 0.03 mm, 0.30 mm, 0.10 mm, 0.20 mm, the distance between adjacent pin center distance small person, take the value should be smaller.
B=1.50mm ~ 3mm, usually about 2mm.
Make it longer if the outside space allows.
(4) There is no through hole (the distance between the through hole and the edge of the pad should be greater than 0.6mm). If the through hole plate and the pad are connected, the connection less than 1/2 of the width of the pad can be connected, such as 0.3mm ~ 0.4mm, to avoid various welding defects caused by solder loss or thermal separation.
(5) Symbols such as characters and graphics are not allowed to be printed in the welding disc used for welding and testing; The mark should be more than 0.5mm away from the edge of the pad. In order to avoid the printing material immersion pad, resulting in various welding defects and affect the accuracy of detection.
(6) The connection between the pad, the pad and the pass plate, as well as the pad and the interconnection wire larger than the width of the pad or the large area of ground or shielded copper foil, there should be a section of heat isolation lead, the wire width should be equal to or less than half of the width of the pad (the smaller pad shall prevail, The general width is 0.2mm ~ 0.4mm, and the length should be greater than 0.6mm); If shielded by a solder mask, the width can be equal to the width of the solder pad (such as the connection with the ground area or shielded copper foil).
(7) For the same components, generally symmetrical use of the pad (such as sheet resistance, capacitance, SOIC, QFP, etc.), the design should strictly maintain its comprehensive symmetry, that is, the shape and size of the pad graph is completely consistent (make solder melt, And the position of the shape of the figure should be completely symmetrical (including the position of the interconnect leading from the pad; If the solder mask is used, the interconnect is free). To ensure that when the solder melts, the surface tension acting on all the solder joints on the components can maintain balance (that is, its resultant force is zero), in order to facilitate the formation of ideal high quality solder joints.
(8) There is no through hole between the welding pads of components without external pins (such as chip resistance, capacitor, adjustable potentiometer, adjustable capacitor, etc.) (that is, there is no through hole under the component body; Except if the dead can be blocked with welding resistance film) to ensure the cleaning quality.