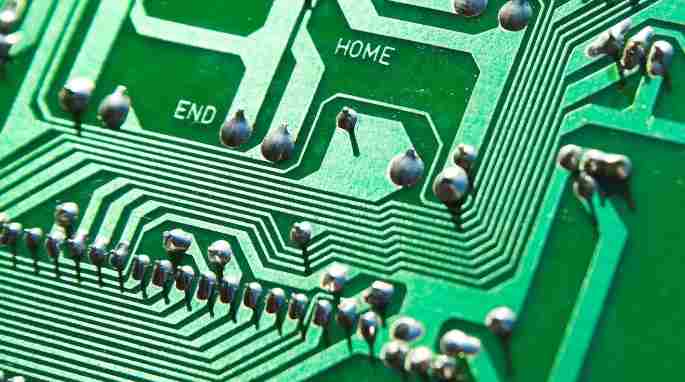
The product deployment phase covers the service phase of the product lifecycle, including support activities and customer feedback to manage reliability and maintainability issues. The continuous improvement process incorporates this feedback and usability metrics into product improvement and improvement activities to support the development of upgrades and alternative configurations within the product family.
The PLM process should support the collation and management of support information from product usage, fault reporting, and services into a single source of facts that can be fed back into the development process.
The end of life
At the end of the product lifecycle, the management of product withdrawal from the market through obsolescence and disposal will be necessary and will usually be replaced by new variants and support for recycling processes.
The PLM process should support the management of product information to support the disposal process.
PLM systems simplify project management for electronic design projects by integrating processes and data into a cohesive solution that is accessible and used by all stakeholders, from project managers to designers, marketers to support staff.
From the design team's perspective, it allows team members to access all relevant information except the typical subset available in an isolated organization. This higher visibility helps prevent problems due to clarity or ambiguity of requirements. It also provides other stakeholders with visibility into design decisions and ensures that their views are taken into account.
If implemented properly, PLM will support data management across product development activities to implement the single fact source concept. In addition, it maintains the integrity of the data and supports its management.
Benefits of PLM
A properly implemented PLM system will improve project delivery by effectively managing workflow optimization processes and reducing development time to achieve faster time to market. Such timing improvements can be crucial in competitive markets, where products that hit the market first can gain sales momentum and a reputational edge over those that come later.
PLM systems will introduce automation and validation into the process, helping to reduce errors throughout the life cycle, reducing the effort and waste of resources needed to resolve problems that are not discovered until the implementation phase. These benefits are achieved primarily through the integration of design and production processes.
PLM systems will improve communication among stakeholders and visibility of project data to provide better quality development and reduce the risk of engineering errors due to misinterpretation or loss of information. This advantage is especially significant for geographically dispersed multidisciplinary teams collaborating on product development projects.
PLM will enable you to react faster and more effectively to change, respond to changing requirements, comply with changing regulations, or open up new markets.
conclusion
Formal product lifecycle management can achieve significant improvements throughout the development phase of a project. Benefits are limited to project management and all stakeholders, including the product design team. The core of product life cycle management is around project data management. With the adoption of Industry 4.0 and the introduction of artificial intelligence solutions to enhance development processes, product lifecycle management systems can be seen as a necessary next step for electronic device development organizations.
Key requirement
PCB data must be available to everyone who needs it when needed. In addition, it must be error-free, and everyone accessing the data set must see the exact same data. Achieving these requirements by creating centralized resources sounds easy, but with large data sets of complex data, it can be a management challenge. Redundancy controls are necessary to ensure that a single failure does not prevent the design team from accessing the data, effectively bringing the design process to an abrupt halt. A local copy of a central resource sounds like a simple solution. Nonetheless, it creates huge problems in ensuring that local data is maintained and consistent across geographically dispersed collaborating teams.
Security controls are needed to prevent data from being accidentally or maliciously destroyed or deleted, dropping a wrench in the design process. In addition, by designing the team to remotely access the centralized solution, control needs to ensure that any type of network outage does not cut the team off from the data.
Controls need to be configured to ensure that only authorized personnel can change data, that changes are recorded and validated, and that the impact of changes on ongoing design projects can be automatically identified and affected parties notified.
A formal release management function should manage the creation of production data sets and bills of materials and their transfer to the purchasing and manufacturing processes. In addition, this capability should include an authorization process to prevent the release of incomplete or unverified data.
generalize
PCB data management is a complex task, if done correctly, it can improve the design accuracy and shorten the time. However, if not implemented properly, any problem can cause the design process to stop or cause the product to not work properly.