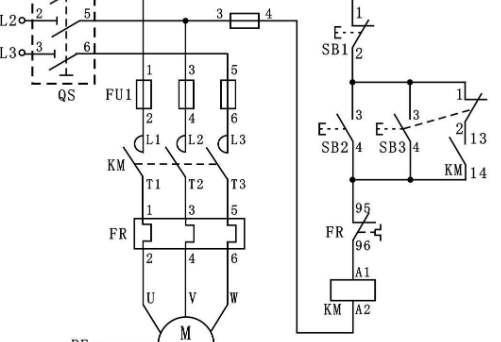
Super - complete pcb failure analysis technology
As the carrier of various components and the hub of circuit signal transmission, PCB has become an important and key part of electronic information products. Its quality and reliability level determine the quality and reliability of the whole equipment.
As the carrier of various components and the hub of circuit signal transmission, PCB has become an important and key part of electronic information products. Its quality and reliability level determine the quality and reliability of the whole equipment. With the miniaturization of electronic information products and the environmental requirements of lead-free and halogen-free, PCB is also developing towards high density, high Tg and environmental protection. However, due to the reasons of cost and technology, a large number of failure problems appear in the process of production and application of PCB, which leads to a lot of quality disputes. In order to find out the cause of failure so as to find a solution to the problem and distinguish the responsibility, the failure case must be analyzed.
To obtain the exact cause or mechanism of PCB failure or defect, the basic principles and analysis process must be followed, otherwise valuable failure information may be missed, resulting in failure of the analysis or the wrong conclusion may be obtained. The general basic process is to first determine the failure location and failure mode based on the failure phenomenon through information collection, functional testing, electrical performance testing and simple appearance inspection, that is, failure location or fault location. For a simple PCB or PCBA, the failure site can be easily identified. However, for a more complex BGA or MCM packaged device or substrate, the defect is not easily observed through a microscope. In this case, other means are needed to determine the defect. Then the failure mechanism analysis should be carried out, that is, the mechanism of PCB failure or defects should be analyzed by various physical and chemical means, such as welding, contamination, mechanical damage, wet stress, medium corrosion, fatigue damage, CAF or ion migration, stress overload and so on. Then there is failure cause analysis, which is based on failure mechanism and process analysis to find the cause of failure mechanism. If necessary, test verification should be carried out as often as possible, through which accurate cause of induced failure can be found. This provides a target-oriented basis for further improvement. Finally, the failure analysis report is prepared according to the test data, facts and conclusions obtained in the analysis process. The report is required to have clear facts, strict logical reasoning and strong organization, and avoid imagination.
In the process of analysis, attention should be paid to the basic principles of using analysis methods from simple to complex, from the outside to the inside, from never destroying the sample to using destruction. Only in this way can we avoid the loss of critical information and the introduction of new artificial failure mechanisms. Just like a traffic accident, if one party of the accident damages or flees from the scene, it is difficult for the wise police to make accurate identification of responsibility. At this time, traffic laws generally require the party who flees from the scene or destroys the scene to take full responsibility. The failure analysis of PCB or PCBA is the same. If an electric soldering iron is used to repair the failed solder joint or a large scissors is used to cut the PCB forcefully, then there is no way to start the analysis. The failure site has been damaged. Especially in the case of few failure samples, once the environment of the failure site is damaged or damaged, the real cause of failure cannot be obtained.
Basic procedures for failure analysis
Optical microscope
The optical microscope is mainly used to inspect the appearance of PCB, find the failure site and related material evidence, and preliminarily judge the failure mode of PCB. Appearance inspection mainly checks PCB contamination, corrosion, the location of burst board, circuit wiring and the regularity of failure, such as batch or individual, is always concentrated in a certain area and so on.
X-ray (X-ray)
For some parts that cannot be inspected by appearance, as well as the through hole inside the PCB and other internal defects, X-ray fluoroscopy system has to be used for inspection. X-ray perspective system is the use of different material thickness or different material density to X-ray moisture absorption or permeability of different principles to image. This technique is more commonly used to check for defects inside PCBA solder joints, through hole internal defects, and defect spot positioning in high-density packaged BGA or CSP devices.