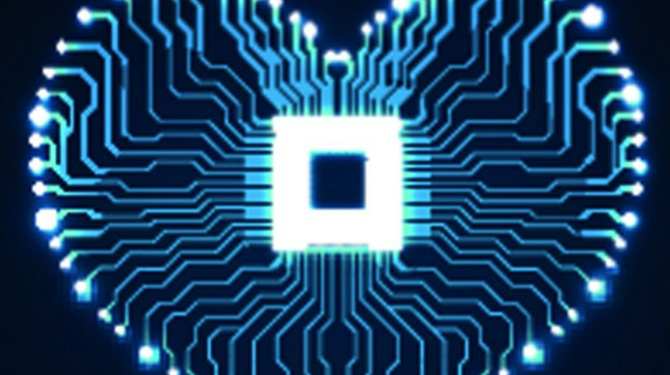
In today's key application objects of PCB, PCB for automobile is occupying an important position. However, due to the special working environment, safety and high current requirements of the automobile, it has high requirements on the reliability and environmental adaptability of PCB, and involves a wide range of PCB technology types, which is a challenge for PCB enterprises. For the manufacturers who want to develop the automotive PCB market, they need to do more understanding and analysis of the new market.
With special emphasis on high reliability and low DPPM for automotive PCBS, does our company have the accumulation of technology and experience in high reliability manufacturing? Is it consistent with the direction of future product development? In the process control, can be well in accordance with the requirements of TS16949? Has low DPPM been achieved? These need to be carefully evaluated, just see this attractive cake and blindly enter, will be harmful to the enterprise itself.
The following provides a representative part of the professional production of automotive PCB enterprises in the testing process of some special practices to provide the majority of PCB colleagues for reference:
1. Second test method
Some PCB manufacturers adopt the "second test method" to improve the rate of finding the defect plate through the first high voltage breakdown.
2, bad board anti-stay test system
More and more PCB manufacturers have installed "good board marking system" and "bad board error prevention box" in the light plate testing machine to effectively avoid artificial leakage. The good plate marking system marks the tested PASS plate for the test machine, which can effectively prevent the tested plate or bad plate from flowing to the customer. In the test process, when the PASS board is tested, the test system outputs the signal that the box is open; Conversely, when a bad board is tested, the case closes, allowing the operator to properly place the tested circuit board.
3. Establish PPm quality system
At present, PPm (Partspermillion defect rate) quality system has been widely used in PCB manufacturers. In many of my company's customers, to Singapore's HitachiChemICal its application and results are the most worthy of reference. There are more than 20 people in the factory who are responsible for the statistical analysis of the abnormal quality of online PCB and the abnormal return of PCB quality. Statistical analysis method of SPC production process was used to classify each broken plate and each returned defective plate for statistical analysis. Besides, auxiliary tools such as microslicing were used to analyze in which production process bad and defective plates were produced. According to the results of statistical data, purposefully solve the problems in the process.
4. Comparative testing method
Some customers use two different brands of PCB models in different batches for comparative testing, and track the PPm of corresponding batches, so as to understand the performance of the two test machines, so as to choose a better performance test machine to test automotive PCB.
5. Improve test parameters
Select higher test parameters to strictly detect this kind of PCB.PCBA OEM because, if select higher voltage and threshold, increase the number of high voltage leakage reading, can improve the detection rate of PCB defect board. For example, a large Taiwan-funded PCB enterprise in Suzhou uses 300V, 30M, 20 euros to test automotive PCB.
(1) When the metal bracket must be used with the metal shield device or case, a zero ohm resistor should be used to realize the connection.
(2) Determine the size of the mounting hole to realize the reliable installation of the metal or plastic support, the top and bottom of the mounting hole to use large welding pad, the bottom of the pad can not use solder resistance, and ensure that the bottom of the pad does not use wave soldering process for welding.
▪ Do not arrange protected signal cables and unprotected signal cables in parallel.
▪ Special attention should be paid to the wiring of reset, interrupt and control signal lines.
(1) High-frequency filtering should be adopted.
(2) Away from input and output circuits.
(3) Away from the edge of the circuit board.
▪PCB should be inserted into the chassis, not in open positions or inside joints.
▪ Attention should be paid to the wiring of signal lines under magnetic beads, between pads and those that may come into contact with magnetic beads. Some magnetic beads conduct electricity quite well and may produce unexpected conductive paths.
▪ If you have several boards in a case or motherboard, put the most electrostatic sensitive board in the middle.