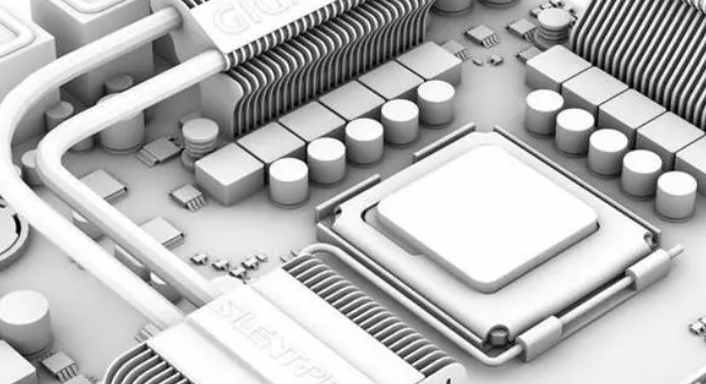
(1) can use low-speed chips do not need high-speed chips, high-speed chips used in key places.
(2) Can be used to string a resistance method, reduce the control circuit up and down along the jump rate.
(3) Try to provide some form of damping for relays, etc.
(4) Use the lowest frequency clock that meets system requirements.
(5) Clock generator as close as possible to the device using the clock. The quartz crystal oscillator housing should be grounded.
(6) Circle the clock area with the ground line and the clock line should be as short as possible.
(7) I/O drive circuit as close as possible to the edge of the printing board, so that it will leave the printing board as soon as possible. The signal entering the printed board should be filtered, the signal from the high noise area should also be filtered, and the series terminal resistance method is used to reduce the signal reflection.
(8) The useless end of MCD should be connected to the high, or grounded, or defined as the output end. The end of the integrated circuit should be connected to the power source, and do not hang.
(9) The input end of the idle gate circuit should not be suspended, the positive input end of the idle operational amplifier should be grounded, and the negative input end should be connected to the output end.
(10) Printed board as far as possible to use 45 line rather than 90 line wiring to reduce high-frequency signal transmission and coupling.
(11) The printed board is partitioned according to the frequency and current switching characteristics, and the noise element and the non-noise element should be further away.
(12) Single panel and double panel with single point power supply and single point grounding, power line, ground as thick as possible, economic is able to bear the use of multilayer board to reduce the power supply, ground inductive.
(13) Clock, bus, chip selection signal should be away from I/O lines and connectors.
(14) analog voltage input line, reference voltage end should be far away from the digital circuit signal line as far as possible, especially the clock.
(15) For class A/D devices, the digital part and the analog part would rather be unified than cross *.
(16) The clock line perpendicular to the I/O line has less interference than the parallel I/O line, and the clock element pins are far away from the I/O cable.
(17) The pin of the component should be as short as possible, and the pin of the decoupling capacitor should be as short as possible.
(18) The key lines should be as thick as possible and protected on both sides. High-speed lines should be short and straight.
(19) The line sensitive to noise should not be parallel to the high-current, high-speed switching line.
(20) Do not run lines under quartz crystals and noise-sensitive devices.
(21) Weak signal circuit, low frequency circuit around do not form a current loop.
(22) Any signal should not form a loop. If it is unavoidable, make the loop area as small as possible.
(23) One decoupling capacitor for each integrated circuit. A small high-frequency bypass capacitor is added to the side of each electrolytic capacitor.
(24) Use large capacity tantalum capacitors or polycool capacitors instead of electrolytic capacitors as circuit charge and discharge storage capacitors. When using tubular capacitors, the case should be grounded.
Brief discussion on SMT patch processing requirements for patch components
In the process of SMT patch processing, the quality of processed products is affected in addition to the SMT processing technology, technology, equipment and graphic design, and the selection of SMT materials is also very important. In the process of SMT patch processing, the selection of appropriate substrate materials will have the effect of twice the result with half the effort on product quality. On the contrary, if the selection of inappropriate materials will have the consequence of twice the result with half the effort. The following Dongguan Xinmeng SMT factory Xiaobian for you to introduce SMT processing how to choose the appropriate SMT material?
There are many kinds of substrates for SMT patch processing, and different materials have different properties. The patch materials are generally divided into two categories, one is organic patch materials, which is represented by the well-known metal base patch; The other is inorganic patch materials, mainly ceramic patch and porcelain shaft coated copper patch.
Metal-base patch because of its performance and characteristics and the performance of electronic products are close to each other, so it has become the best choice for many SMT processing plants. The metal patch is made of 0.3mm-2.Omm thick metal plate, such as aluminum plate, steel plate, copper plate and epoxy resin semi-cured sheet and copper foil. Metal plate can achieve large area SMT processing, and has the following performance characteristics:
1. Good mechanical properties
Metal-based patches have high mechanical strength and toughness, better than rigid material patches, can be used for large area patch processing, and can undertake the installation of overweight components, in addition, metal-based patches also have high dimensional stability and smoothness.
2, good heat dissipation performance
Because the metal patch is directly in contact with the semi-cured sheet, it has excellent heat dissipation performance. The metal patch is used for patch processing. During processing, the metal patch can play the role of heat dissipation. The heat dissipation capacity depends on the material and thickness of the metal patch and the thickness of the resin layer. Of course, while taking into account the heat dissipation performance, electrical performance, such as electrical strength, should also be taken into account.
3, can shield electromagnetic ferry
In the high frequency electronic circuit, to prevent electromagnetic radiation is always the concern of designers, the use of metal patch can act as a shield plate, play the role of shielding electromagnetic.