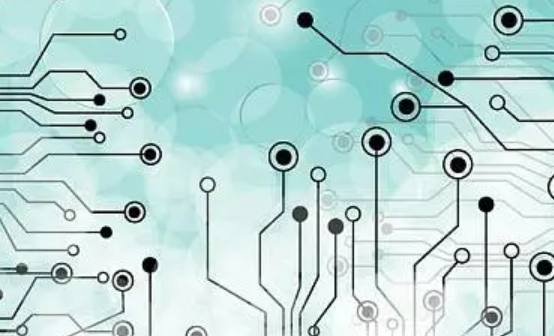
How to reflect the SMT patch processing solder joint quality
Nowadays, the "light, thin, short and small" of electronic products has put forward higher requirements for miniaturization and assembly density of components. Under such requirements, how to ensure solder joint quality is an important issue in SMT patch processing. Solder joint as a direct result of welding, its quality and reliability determine the quality of electronic products. That is to say, in the production process, the quality of assembly is ultimately reflected in the quality of welding. So SMT patch processing how to reflect the solder joint quality?
First, the appearance of the solder joint evaluation
A good solder joint should be in the service life of the equipment, its mechanical and electrical properties do not fail. Its appearance is as follows:
1, good wetting;
2. Complete, smooth and bright surface;
3, the appropriate amount of solder and solder completely cover the welding parts of the pad and lead (or welding end), the height of the component is moderate.
In principle, these criteria are applicable to all types of solder joints produced by all welding methods in SMT patch processing. In addition, the edge of the welding point should be thin. If the welding surface is large enough, the wetting Angle between the solder and the pad surface should be less than 300, and the maximum should not exceed 600.
2. Failure form of solder joint within the life cycle
Considering the relationship between failure and time, the failure form is divided into three different periods:
1. In the early failure stage, a large number of welding joints with poor quality fail, and some welding joints are damaged due to improper process operation and loading and unloading. The process can be optimized to reduce the early failure rate.
2, stable failure rate stage, the quality of most of the solder joints in this stage is good, the failure rate (failure rate) is very low, and relatively stable.
3, the end of life, failure is mainly caused by the accumulation of broken factors, including chemical, metallurgical, thermal mechanical characteristics and other factors, such as the occurrence of metal reaction between solder and welded metal, or thermal mechanical stress caused by solder joint failure. The failure is mainly determined by the characteristics of the material, the specific structure of the solder joint and the load.
Solder paste, usually called solder paste or solder paste, solder paste is a kind of welding material must be used in SMT patch processing. The main composition is to mix tin powder and flux into paste. The following Jingbang SMT processing factory will introduce the SMT processing solder paste types and instructions for use.
First, the type of tin paste
1. According to environmental protection requirements, it is divided into lead paste and lead-free paste (environmental protection paste) :
Environmental protection tin paste only contains trace amounts of lead, lead is harmful to human health, in the electronic products exported to Europe and the United States, the content of lead requirements are not strict. Therefore, lead-free process will be used in SMT patch processing. First, SMT patch processing industry in the next few years, SMT patch processing using lead-free process is a trend.
In the processing process of lead-free SMT, it is more difficult to apply tin than the process with lead, especially in the case of BGAQPN, etc., the paste with a high proportion of silver will be used. Silver with 3 points and silver with 0.3 points are common in the market. In the solder paste, silver solder paste is a more expensive at present.
2. According to the melting point, it can be divided into high temperature, moderate and low temperature three kinds:
Commonly used high temperature tin silver copper 305,0307. Medium temperature is tin bismuth silver, low temperature is commonly used tin bismuth, in SMT processing according to the characteristics of different products to choose.
3. According to the fine tin powder, it is divided into No.3 powder No.4 powder No.5 powder tin paste:
Selection: In the SMT patch processing of general large components (1206 0805 LED lights), No. 3 powder tin paste is used, because its price is relatively cheap.
In digital products have encountered dense foot IC, in SMT patch processing will use 4 powder solder paste.
In the encounter of very precise welding components such as BGA, very demanding products such as mobile phones and tablets, SMT patch processing will use No. 5 powder tin paste.
2. Preservation of solder paste and preparation before printing
After receiving the solder paste, please put it in the refrigerator immediately and store it at 3-7℃. Please note that solder paste cannot be frozen.
Preparation for solder paste printing: The following two steps must be carried out before the solder paste is removed from the refrigerator and put into the printing process:
(1) Do not open the seal, and place it at room temperature for at least 4-6 hours, so that the temperature of the solder paste naturally rises to room temperature.
(2) After the solder paste temperaturereaches room temperature, before being put into printing, it is necessary to stir to ensure the uniform distribution of each component in the solder paste. It is recommended to use special mixing equipment, stirring in the same direction for 1-3 minutes.