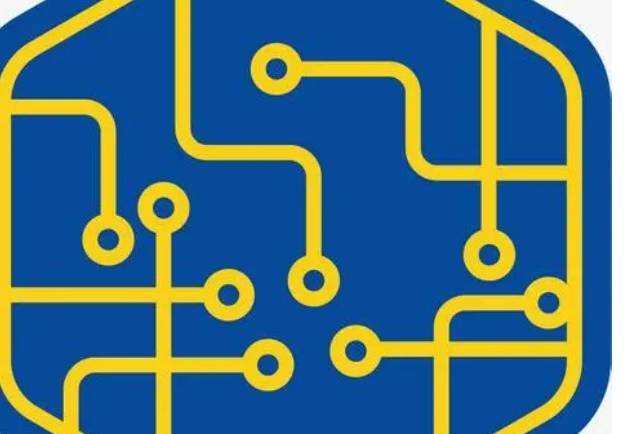
With the rapid development of mobile phone, electronics, communication industry, but also promote the PCB circuit board industry continues to expand and rapid growth, customers for PCB factory components layer, weight, precision, materials, color, reliability and other requirements are more and more high.
However, due to the fierce price competition in the market, the cost of PCB board materials is also on the rise. In order to improve the core competitiveness, more and more manufacturers monopolize the market with low prices. However, behind these ultra-low prices, is to reduce the cost of materials and production costs to obtain, but the device is usually prone to cracks (cracks), easy scratches, (or bruises), its precision, performance and other comprehensive factors are not up to standard, seriously affecting the use of products on the weldability and reliability and so on.
In the face of various PCB circuit boards on the market, distinguish PCB circuit boards good or bad can start from two aspects; The first method is to judge from the appearance, on the other hand is to judge from the quality specification of PCB board itself.
The method of judging the quality of PCB circuit board:
First: Distinguish from the appearance of the circuit board is good or bad, under normal circumstances, PCB circuit board appearance can be analyzed through three aspects;
1. Standard rules of size and thickness: the thickness of the circuit board to the standard circuit board is different sizes, customers can measure and check according to their own product thickness and specifications.
2. Appearance of weld: Because there are more parts of the circuit board, if the welding is not good, the parts are easy to fall off the circuit board, which seriously affects the welding quality of the circuit board. It is very important to have a good appearance, carefully identify and strong interface.
3 Light and color: external circuit boards are covered with ink, circuit boards can play the role of insulation, if the color of the board is not bright, less ink, insulation board itself is not good.
Second: high-quality PCB circuit boards need to meet the following requirements
1. The telephone should be easy to use after the components are installed, that is, the electrical connection should meet the requirements;
2. High temperature copper skin is not easy to fall off;
3. The mechanical properties of the surface should meet the installation requirements;
4. The surface of copper is not easy to oxidize, which affects the installation speed and breaks down soon after oxidation.
5. No additional electromagnetic radiation;
6. The shape is not deformed, so as to avoid the deformation of the shell and dislocation of the screw hole after installation;
7. High temperature, high humidity and special environment should also be considered; Line width, line thickness, line distance meet the requirements, so as to avoid line heating, open circuit, and short circuit;
8. Now the installation is mechanized, the hole position of the circuit board and the deformation error of the circuit and the design should be within the allowable range.
Design standard for packaging and holes of components in PCB design
First, PCB design components package library design standards
1, patch components through reflow welding and wave welding should adopt different packaging, wave welding (red glue process) of plate patch resistance parts preferred to use 0805 packaging;
2, part of the vitality of the standard aperture and pad
The pad width of the patch element should be the same as that of the component width, namely 1:1.
3. PCB standard packaging library should be called. (The suggestions below are based on the standard library)
Second, PCB design components foot spacing design standards
1, plug-in capacitor, thermistor, pressure sensitive resistor, cement resistor, relay, socket, insert, buzzer, receiving head, ceramic resonator, digital tube, touch button, LCD screen, fuse and other devices adopt the packaging form consistent with its foot distance. PCB component hole spacing and component pin spacing must match (note the component pin spacing of different suppliers for the same code).
2, color ring resistance, diode parts foot distance as far as possible in a unified 10mm, jumper width foot distance unified in 5mm; 7.5mm; 10mm; 12.5mm; Five kinds of 15mm.
3. The foot distance of bent-belt incoming materials (porcelain capacitor, thermistor, etc.) should be 5mm. For the rest, the hole distance of PCB parts is designed with the actual foot width of the parts.
4. Plug-in audion is recommended to use a three-hole line, each hole is 2.5mm apart.
5, 7812, 7805 recommended to adopt triangular forming, can also use three hole line, each hole is 2.5mm apart.
6. 7812 and 7805 cannot share the same heat sink. Independent heat sink is recommended.
7. Where it is necessary to use replacement components, the circuit board should leave holes for replacement components.
3. PCB design hole spacing design standard
The hole edge distance between two adjacent components should be more than 1.5mm.
4. The design standard of PCB design aperture is shown in the table below
Note: The confirmed components shall have strict requirements for PCB mounting size tolerance!
Component foot is square foot in principle printed circuit board holes should also be square holes, and the length and width of the holes can not exceed the length and width of the component foot 0.1mm; Especially the square foot compressor relay and square foot single insert must use square hole design. However, due to the limitation of the processing technology of the hole, the length and width of the hole should not be less than 0.8mm. If both are less than 0.8mm, 0.8mm round hole should be made directly.
5, PCB design metallized hole design standard
1, can not use metallized hole conduction large current (above 0.5A).
2, only through the connection of the through hole, under the premise of meeting the wiring requirements, generally do not make special requirements, generally use the hole diameter of 1.0mm hole, the minimum can be 0.5mm.
3. Try to avoid the design of metallized holes (over holes) on the pad, and the metallized holes and solder joints are too close (less than 0.5mm). The over holes may suck the molten solder from the components due to capillary action, resulting in incomplete solder joints or virtual welding.