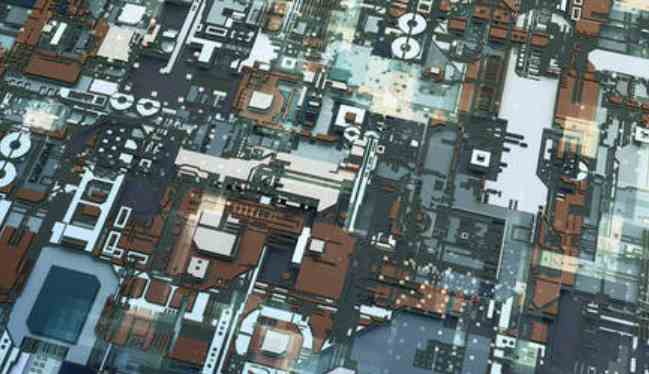
See FIG. 1 for typical photos of the black pad, and FIG. 2 for the cross section of the black pad. From the photos of the cross section, it can be seen that there are typical longitudinal cracks, which are typical characteristics of black nickel.
It can be seen from the photos of the cross section that there is a typical longitudinal crack, which is a typical feature of black nickel. When the black nickel is generated, the gold coating on the surface of ENIG will not have obvious discoloration, which is easy to give the illusion that the welding pad surface treatment is still good. When the welding pad is carried out at high temperature, the gold, as a protective layer of weldability, will quickly dissolve into the solder paste, while the nickel, which has been corroded and oxidized, cannot form a commingle (IMC) with the molten tin, leading to a serious decline in the reliability of the solder joint, and cracking will occur as long as it is slightly affected by external force. Typical solder joint cracking caused by this black nickel is shown in Figure 3.
When the welding pad is carried out at high temperature, the gold, as a protective layer of weldability, will quickly dissolve into the solder paste, while the nickel, which has been corroded and oxidized, cannot form a commingle (IMC) with the molten tin, leading to a serious decline in the reliability of the solder joint, and cracking will occur as long as it is slightly affected by external force.
Formation and harm of phosphorous rich layer
In the welding process of the welding pad treated by ENIG surface, the "nickel" in ENIG really forms an alloy with the solder paste. The typical intermetallic compound (IMC) alloy is Ni3Sn4, while the phosphorus in the nickel coating does not participate in the metallization, but in the nickel layer, phosphorus occupies a certain proportion and is evenly distributed. In this way, After nickel is involved in alloying, the local excess phosphorus will be enriched and concentrated on the edge of the alloy layer to form a phosphor-rich layer. If the phosphor-rich layer is too thick, its strength will be greatly reduced. When the solder joint is affected by external stress, it must be damaged from the most vulnerable link, and the phosphor-rich layer may be the first weak link to destroy, then the reliability of the solder joint will be obviously affected.
Especially in the high heat lead-free process, if the process control is poor, the intermetallic compounds are often thicker, resulting in more phosphorus, phosphorus rich layer is more obvious, and the reliability of the solder joint is in danger. The typical phosphor-rich layer is shown in the black zone between the intermetallic compound and the nickel coating in Figure 4. This black zone can be analyzed by energy dispersive spectroscopy (EDS) to confirm that it contains very high phosphorus content. A large number of failure cases prove that the existence of phosphorus-rich layer is one of the main reasons for the failure of solder joint cracking.
Prevention and control of black nickel and phosphorus rich layer
Although the formation of black nickel and the appearance of phosphorus-rich layer have strong concealment, it may be difficult to detect and prevent by common means. But when we understand its causes, we can find effective prevention and control methods.
For the formation of black nickel, the manufacturing stage is mainly to do a good job of bath maintenance and process temperature control, so that the nickel phosphorus ratio in the coating in the best state. Acidic gold water also needs to have good maintenance, its corrosion should be adjusted in time.
For the user,
1. The best means is to use scanning electron microscope (SEM) to observe the surface treatment of the welding pad, mainly to check whether there are cracks in the gold layer, and EDS to analyze whether the proportion of phosphorus in the nickel coating is within the normal range;
2. Secondly, you can choose the typical welding pad to manually weld and measure the push and pull strength of the solder joint. When it is found that the push and pull strength is abnormally small, there may be black nickel;
3. The last method is to carry out acid gas corrosion test on ENIG samples. If powder or discoloration is found on the surface, the gold coating on the pad is cracked, which indicates the possibility of the existence of black nickel.
Of these methods, the most convenient and quick should be the second method, simple and easy. With these tools, problems can be detected before the ENIG board is used, avoiding the creation of a large number of board components with reliability problems and keeping losses to a minimum.
For the generation of phosphorus-rich layer, when the proportion of phosphorus and nickel in nickel plating is appropriate, the welding process, welding time and welding temperature are mainly controlled, and the thickness of intermetallic layer is controlled at the best 1-2 micron (um). When the formation of too thick intermetallic layer (IMC), the enrichment of too thick phosphorus-rich layer is inevitable.