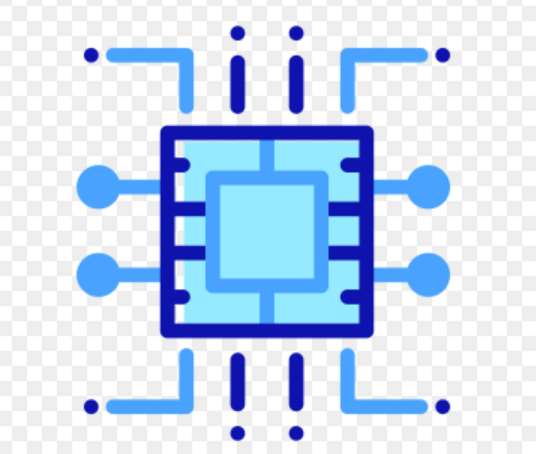
SMT patch processing is one of the most common technologies in the electronics industry. For such a process, what problems do we need to know in order to better play its advantages? The following Jingbang SMT patch factory small make up for you a brief introduction:
1. Mounting of patch processing: Its role is to accurately install the surface assembly components to the fixed position of PCB. The equipment used is the SMT machine, which is located behind the screen printing machine in the SMT production line.
2. Screen printing of patch processing: its function is to leak solder paste or patch glue onto the solder pad of PCB to prepare for the welding of components. The equipment used is screen printing machine (screen printing machine), located at the front end of the SMT line.
3, curing of patch processing: its role is to melt the patch glue, so that the surface assembly components and PCB board firmly bonded together. The equipment used is the curing furnace, which is located behind the SMT machine in the SMT line.
4, patch processing dispensing: it is the glue drops to the fixed position of PCB, its main role is to fix the components to the PCB board. The equipment used is the dispensing machine, which is located at the front end of the SMT production line or behind the testing equipment.
Introduction of nickel electroplating process for printed circuit board PCB
PCB (English PrintedCircuieBoard printed circuit board is short for) with nickel plating as the substrate coating of precious metals and base metals, for some single-sided printed boards, also commonly used as the surface layer. For some surfaces with heavy load wear, such as switch contacts, contact pieces or plug gold, the use of nickel as gold substrate coating, can greatly improve the wear resistance. When used as a barrier, nickel is effective in preventing diffusion between copper and other metals. The matte nickel/gold composite coating is often used as the corrosion resistance of metal coating, and can adapt to the requirements of hot pressing welding and brazing, only nickel can be used as the corrosion resistance coating containing ammonia etching agent, and do not need hot pressing welding and require bright coating of PCB, usually use light nickel/gold coating. The thickness of the nickel coating is generally not less than 2.5 microns, usually 4-5 microns.
Low stress nickel deposits of PCBS are usually plated with modified Watt nickel baths and some sulfamate nickel baths with stress-reducing additives.
We often say that PCB nickel plating has smooth nickel and dumb nickel (also known as low-stress nickel or semi-bright nickel), usually requires uniform and fine coating, low porosity, low stress, good ductility characteristics.
2, nickel sulfamate (nickel ammonia)
Nickel sulfamesulfonate is widely used as substrate coating on metallized hole electroplating and printed plug contact sheets. The obtained deposition layer has low internal stress, high hardness and excellent ductility. A de-stressing agent is added to the bath and the resulting coating will be slightly stressed. There are many different formulations of sulfamate plating bath, typical sulfamate nickel plating bath formulations are listed below. Because of the low stress of the coating, so it is widely used, but the stability of nickel sulfamate is poor, its cost is relatively high.
3, modified Watt nickel (nickel sulfide)
The modified Watt nickel formulation uses nickel sulfate, together with the addition of nickel bromide or nickel chloride. Due to internal stress, nickel bromide is generally used. It can produce a semi-bright, slightly stressed, malleable coating; And this coating for subsequent plating is easy to activate, cost relative bottom.
4, the role of each component of the bath:
The main salts -- nickel sulfamesulfonate and nickel sulfate are the main salts in the nickel liquid. The nickel salt mainly provides the nickel metal ions needed for nickel plating and also plays the role of conductive salt. The concentration of nickel plating solution varies slightly with different suppliers and the allowable content of nickel salt varies greatly. Nickel salt content is high, can use a higher cathode current density, deposition speed is fast, commonly used for high-speed thick nickel plating. But too high concentration will reduce the cathode polarization, dispersion ability is poor, and the plating bath loss is large. The nickel salt content is low and the deposition rate is low, but the dispersion ability is good, and the fine crystalline bright coating can be obtained.
Buffering agent -- boric acid is used as buffering agent to keep the PH value of nickel plating liquid in a certain range. The practice shows that when PH value of nickel plating solution is too low, the cathode current efficiency will decrease. When the PH value is too high, due to the continuous precipitation of H2, the PH value of the liquid layer close to the cathode surface rises rapidly, resulting in the formation of Ni(OH)2 colloid, and Ni(OH)2 inclusion in the coating, the coating brittleness increases, and the adsorption of Ni(OH)2 colloid on the electrode surface, but also cause the retention of hydrogen bubbles on the electrode surface. Increase the porosity of the coating. Boric acid not only has the PH buffer effect, but also it can improve the cathode polarization, thus improving the bath performance, reduce the "burning" phenomenon under the high current density. The presence of boric acid is also beneficial to improve the mechanical properties of the coating.