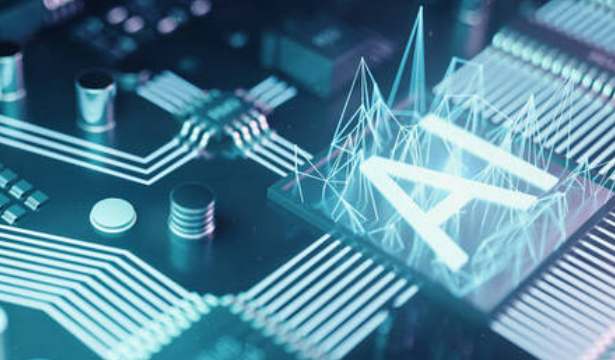
Anode activator -- Except for sulfate nickel plating solution which uses insoluble anode, other nickel plating processes all use soluble anode. In order to ensure the normal dissolution of the anode, a certain amount of anode activator is added to the plating solution. It was found that CI - chloride ion was the best activator for nickel anode. In nickel plating solution containing nickel chloride, nickel chloride plays the role of anode activator as well as main salt and conductive salt. In nickel plating solution without nickel chloride or its content is low, it is necessary to add a certain amount of sodium chloride according to the actual situation. Nickel bromide or nickel chloride are also commonly used as stress relief agents to maintain the internal stress of the coating and to give the coating a semi-bright appearance.
Additive - the main ingredient of additive is stress reliever, the addition of stress reliever, improve the cathode polarization of the plating solution, reduce the internal stress of the coating, with the change of the concentration of stress reliever, can make the internal stress of the coating change from tensile stress to compressive stress. Commonly used additives are: naphthalene sulfonic acid, p-toluenesulfonamide, saccharin, etc. Compared with the nickel coating without de-stressing agent, the uniform fine and semi-bright coating can be obtained by adding de-stressing agent to the plating solution. Usually stress relief agents are added by ampere-hour (now common combination of special additives including pinhole prevention agents, etc.).
Wetting agent - In the process of electroplating, hydrogen precipitation on the cathode is inevitable. Hydrogen precipitation not only reduces the cathode current efficiency, but also causes pinholes in the coating due to the retention of hydrogen bubbles on the electrode surface. The porosity of nickel plating layer is relatively high, in order to reduce or prevent the production of pinholes, a small amount of wetting agent should be added to the plating solution, such as sodium dodecyl sulfate, sodium diethyl hexyl sulfate, sodium n-octylsulfate, it is an anionic surface active substance, can be adsorbed on the cathode surface, the electrode and the solution between the interfacial tension reduction, The wetting contact Angle of hydrogen bubbles on the electrode is reduced, so that bubbles can easily leave the electrode surface, preventing or reducing the formation of pinholes in the coating.
5. Maintenance of plating solution
a) Temperature -- Different nickel processes use different bath temperatures. The influence of temperature on nickel plating process is complicated. In the nickel plating solution at higher temperature, the internal stress of the nickel coating is low and the ductility is good. The internal stress of the nickel coating is stable when the temperature is increased to 50 degrees C. The general operating temperature is maintained at 55-60 degrees C. If the temperature is too high, nickel brine hydrolysis will occur, resulting in nickel hydroxide colloidal hydrogen bubble retention, resulting in pinholes in the coating, but also reduce the cathode polarization. Therefore, the working temperature is very strict and should be controlled within the prescribed range. In actual work, the normal temperature controller is used to maintain the stability of the working temperature according to the optimal temperature control value provided by the supplier. #p# Page title #e#
b) PH value -- The practical results show that the PH value of nickel plating electrolyte has a great influence on the coating properties and electrolyte properties. In PH≤2 strong acid electroplating solution, no metal nickel deposition, only light gas precipitation. Generally, the PH value of PCB nickel plating electrolyte is maintained between 3 and 4. The nickel plating solution with higher PH value has higher dispersion force and higher cathode current efficiency. However, when the PH is too high, due to the continuous precipitation of light gas from the cathode in the electroplating process, the PH value of the coating near the cathode surface increases rapidly. When the pH value is greater than 6, there will be light nickel oxide colloid formation, resulting in hydrogen bubble retention, and the coating pinhole. The inclusion of nickel hydroxide in the coating will also increase the brittleness of the coating. A nickel plating solution with a lower PH and better anodic dissolution can increase the content of nickel salts in the electrolyte, allowing the use of a higher current density, thus enhancing production. However, if PH is too low, the temperature range of bright coating will be narrowed. Add nickel carbonate or basic nickel carbonate, PH value increases; Add sulfamic acid or sulfuric acid to reduce the PH value. Check and adjust the PH value every four hours during the operation.
c) anode -- soluble anode is used in conventional nickel plating of PCB at present, and it is quite common to use titanium basket as anode with nickel Angle. Its advantage is that the anode area can be made large enough and does not change, anode maintenance is relatively simple. The titanium basket shall be loaded into the anode bag made of polypropylene material to prevent the anode mud from falling into the plating solution. And should regularly clean and check whether the hole is smooth. The new anode bag should be soaked in boiling water before use.