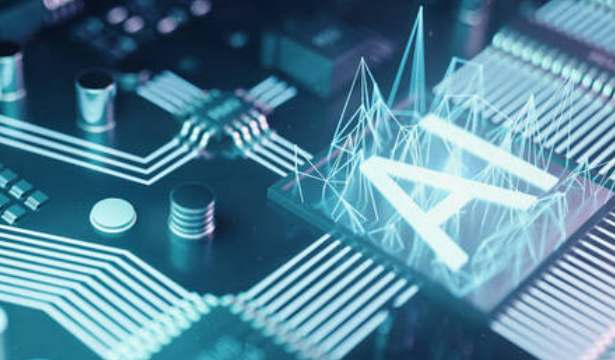
d) purification - when there is organic pollution in the plating solution, it should be treated with activated carbon. But this method usually removes part of the de-stress agent (additive) and must be replaced. The treatment process is as follows;
(1) Take out the anode, add 5ml/l of impurity water, heat (60-80 degrees C) and pump (air stirring) for 2 hours.
(2) When there are many organic impurities, add 3-5ml /lr 30% hydrogen peroxide for treatment and stir for 3 hours.
(3) Add 3-5g /l powdery activity under constant agitation, continue to stir for 2 hours in air, turn off the agitation and let stand for 4 hours, add the filter powder to use the spare tank for filtering and cleaning at the same time.
(4) cleaning and maintenance anode hanging back, with nickel plated corrugated iron plate as the cathode, in the current density of 0.5-0.1 ampere/square meter to drag cylinder 8-12 hours (when the plating solution has inorganic pollution affecting the quality, it is often used)
(5) change the filter element (generally with a group of cotton core and a group of carbon core in series continuous filtration, according to the periodic change can effectively delay the large processing time, improve the stability of the plating solution), analyze and adjust the parameters, add additive wetting agent can test plating.
e) Analysis -- The plating solution should be based on the key points of the process control procedure, the composition of the plating solution and the hull bath test should be analyzed regularly, and the production department should adjust the parameters of the plating solution according to the obtained parameters.
f) Agitation -- Nickel plating process As with other electroplating processes, the purpose of agitation is to accelerate the mass transfer process in order to reduce concentration variations and increase the upper limit of allowable current density. Stirring the plating solution also has a very important role, is to reduce or prevent nickel plating layer pinhole. Because, in the plating process, the ion plating near the cathode surface is poor, a large number of hydrogen precipitates, so that the PH value rises and nickel hydroxide colloids are produced, resulting in the detention of hydrogen bubbles and pinholes. The above phenomena can be eliminated by strengthening the stirring of the remaining plating solution. Mixing with compressed air, cathode movement and forced circulation (combined with carbon and cotton core filtration) is commonly used.
g) Cathode current density -- Cathode current density has influence on cathode current efficiency, deposition rate and coating quality. The test results show that the cathode current efficiency increases with the increase of current density in the low current density region when the electrolyte with low PH is used for nickel plating. In the high current density region, the cathode current efficiency has no relation with the current density, but the cathode current efficiency has little relation with the current density when the plating solution nickel with high PH is used.
Like other kinds of plating, the range of cathode current density selected for nickel plating should also depend on the composition of plating solution, temperature and stirring conditions, due to the large PCB plate area, so that the current density of the high current area and the low current area is very different, generally use 2A/dm2 is appropriate.
6. Failure cause and elimination
a) Pitting: Pitting is the result of organic matter pollution. Large pits usually indicate oil contamination. If you don't stir well, you can't dislodge the air bubbles, which leads to pitting. Can use wetting agent to reduce its impact, we usually put the small pitting point called pinhole, poor pre-treatment, metal, boric acid content is too little, bath temperature is too low will produce pinhole, bath maintenance and process control is the key, anti-pinhole agent application as process stabilizer to add.
b) Roughness and burr: roughness indicates that the solution is dirty, which can be corrected by sufficient filtration (too high PH is easy to form hydroxide precipitation should be controlled). Current density is too high, anode mud and water is not pure into impurities, serious will produce rough and burr.
c) Low binding force: if the copper coating is not fully oxidized, the coating will peel off, and the adhesion between copper and nickel is poor. If the current is interrupted, it will cause the nickel coating itself to peel off at the break, and the temperature is too low and serious.
d) Poor brittleness and weldability of the coating: When the coating is bent or subjected to some degree of wear, the brittleness of the coating is usually revealed. This indicates the existence of organic matter or heavy metal pollution, excessive additives, endocked organic matter and electroplating corrosion resistance, is the main source of organic matter pollution, must be treated with activated carbon, insufficient added economy and high PH will also affect the coating brittleness.
e) Dark coating and uneven color: dark coating and uneven color, indicating metal pollution. Since the copper plating is generally followed by nickel plating, the copper solution brought in is the main source of pollution. It is important to minimize the amount of copper in the hanging gear. To remove metal contamination from the tank, especially copper removal solutions, a corrugated steel cathode should be used and emptied of 5 amps per gallon of solution for one hour at a current density of 2 to 5 amps per square foot. Poor pretreatment, poor low coating, too small current density, too low concentration of main salt, electroplating power circuit contact will affect the color of the coating. #p# Page title #e#
f) Coating burn: Possible causes of coating burn: insufficient boric acid, low concentration of metal salt, low working temperature, too high current density, too high PH or insufficient agitation.
g) Low deposition rate: Low P value or low current density will result in low deposition rate.
h) Coating foaming or peeling: poor treatment before plating, prolonged power failure in the middle, organic impurity pollution, current density is too high, temperature is too low, PH is too high or too low, serious influence of impurities will produce foaming or peeling phenomenon.
I) anode passivation: insufficient anode activator, too small anode area and too high current density.