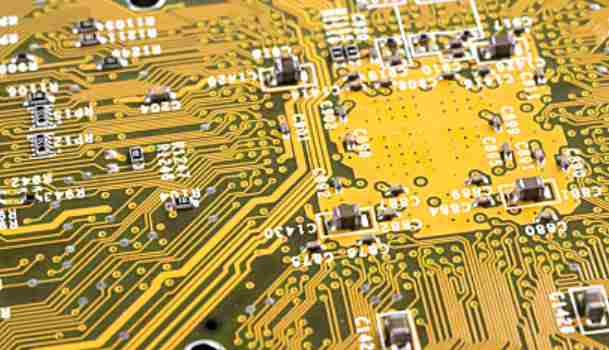
In this paper, the different mechanisms of Solder Bead production and Solder Ball production in the reflow welding are described. The reasons of solder bead production and measures to be taken to prevent and reduce the bead are described. In this paper, how to analyze and improve the tin beads after the appearance of the method suggestions and references are provided
1 Introduction
Tin bead phenomenon is one of the main defects in surface assembly technology (SMT) production. Due to its many causes, it is difficult to control, so it often troubles SMT engineers and technicians. The formation mechanism of tin beads is different from that of tin balls, and the countermeasures need to be different. The tin bead mainly appears on the side of the chip resistive capacitive element, and sometimes also appears near the IC pin. Tin beads not only affect the appearance of board products, more importantly, because of the dense components on the printing board, there is a danger of short circuit in the use process, thus affecting the quality of electronic products. There are many reasons for tin beads, often caused by one or more factors, so we must do a good job in prevention and improvement in order to better control it.
2. Mechanism of tin beads and tin spheres
2.1 Formation mechanism of tin ball
The main reason for the tin ball is that in the process of solder joint forming, the molten metal alloy "splashes" out of the solder joint for various reasons, and forms many scattered small solder balls around the solder joint. They are often clustered and discrete in the form of small particles stuck in the flux residue around the end of the component or pad.
Common causes of tin balls are:
The material subjected to too fast heating or cooling, especially lead-free high temperature process, will lead to the formation of tin balls.
The evaporation rate of molten flux is too fast when reflow welding, the proportion of relatively high solvent in the flux composition is relatively high, or excessive solvent with high boiling point, improper heating and so on will lead to the possibility of tin ball production.
(3) The soldering surface or solder in the oxidation degree of tin is too high, so that the welding of the whole parts of the solder heat, heat and other processes are not consistent, thus affecting the thermal conductivity of the flux, heat transfer and other thermal behavior is affected, will also make the possibility of tin ball.
The use of solder paste in the process of adverse factors affect the solder paste use environment, such as improper solder paste back temperature lead to solder paste (solder paste flux contains more hydrophilic components) moisture absorption, will cause solder paste splash in the welding process and form tin ball.
2.2 Formation mechanism of tin beads
Tin bead refers to some large solder ball in the solder paste welding, solder paste may be collapsed, extrusion and other reasons beyond the printing pad, in the welding process, these exceed the solder paste on the solder plate in the welding process failed to melt together and independent, formed in the element body or near the pad, But most of the tin beads occur on either side of the chip element.
Take the chip element with square pad design as an example, as shown in Figure 2 below. After the solder paste printing, if there is more solder paste, it is easy to produce tin beads. The solder paste beyond the pad is divided into two parts, which are the extension part of the pad (blue area) and the extension part of the pad (yellow area). The red area is the actual pad area.
For the solder paste of the epitaxial part of the pad, as long as the solder paste of the pad part is fused together with the solder paste when forming a Fillet during welding, the tin bead will not be formed. For the inner extension part of the disc, when the amount of solder is small, the solder paste can form a Fillet with the welding end of the component; But when the amount of solder, the element placement pressure will squeeze the solder paste to the element body (insulator) below, in the flow welding heat melt, due to the surface energy, melting solder paste into a ball, it has a tendency to raise the element, but the force is very small, the element gravity squeeze to both sides of the element, separated from the pad, in the cooling of the formation of tin beads. If the element gravity is large and more solder paste is extruded, even more tin beads will be formed.
2.3 Difference between tin beads and tin balls
Tin beads and tin balls are often confused, but they are not. The main difference between tin beads and tin balls is that the mechanism of production is different. In addition, the outer shape of the tin bead is larger than that of the tin ball in terms of the apparent volume, usually larger than 5mil in diameter. From the position of appearance, the tin bead is mainly concentrated in the middle of the chip element and the element body is relatively low on both sides, and the tin ball in the flux residue anywhere. From the point of view of the number of tin beads is generally 1 to 4, and the tin ball is uncertain, the number is often many.
3 Factors affecting the production of tin beads
According to the formation of tin beads, the main factors affecting the formation of tin beads are:
The graphic design of SMT steel mesh opening and pad.
⑵SMT steel mesh cleaning.
⑶ Repetition accuracy of the machine.
(4) Temperature curve of reflow furnace.
⑸ Patch pressure.
⑹ solder plate outside solder paste quantity.
4. Countermeasures and experience to reduce the production of tin beads