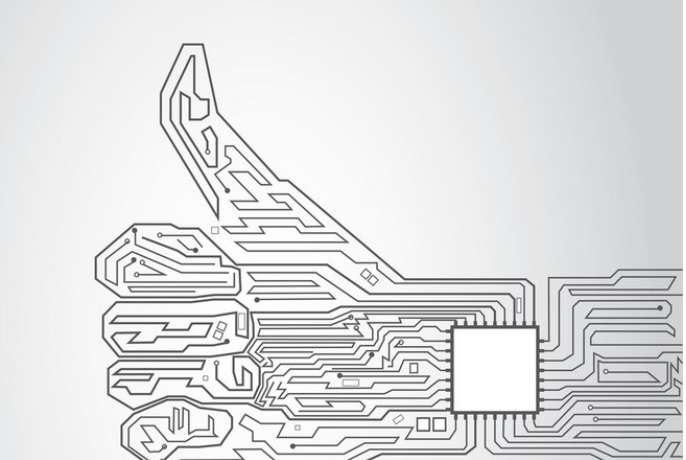
Input ground and output ground in the switching power supply for low-voltage DC-DC, to output voltage feedback back to the primary transformer, both sides of the circuit should have a common reference, so after the ground wire on both sides of the copper, but also connected together, to form a common ground.
After the wiring design is completed, it is necessary to carefully check whether the wiring design conforms to the rules formulated by the designer, and also confirm whether the rules formulated meet the requirements of the printed board production process. Generally, it is necessary to check whether the distance between wire and wire, wire and component pad, wire and through hole, component pad and through hole, through hole and through hole is reasonable, and whether it meets the production requirements. Is the width of the power cord and ground wire appropriate? Is there any place in the PCB where the ground wire can be widened? Note: Some errors can be ignored. For example, some connectors have part of their Outline lying outside the frame, and errors occur when checking spacing. In addition, after each modification of the line and hole, it is necessary to re-cover the copper once.
2. Review According to the "PCB checklist", the content includes the design rules, layer definition, wire width, spacing, pad, hole setting, but also focus on the review of the rationality of the device layout, power supply, ground network wiring, high-speed clock network wiring and shielding, the placement and connection of the coupling capacitor.
Three, the design output output light drawing file matters needing attention:
a, need to output the layer of wiring layer (bottom), screen printing layer (including the top screen printing, bottom screen printing), welding resistance layer (bottom welding resistance), drilling layer (bottom), in addition to the generation of drilling file (NC Drill).
B. When setting the Layer of the screen printing layer, do not select Part Type, select the Outline, Text and Line of the top layer (bottom layer) and the screen printing layer.
c. When setting the Layer of each Layer, select the Board Outline; when setting the layer of the screen printing layer, do not select Part Type; select the Outline, Text and Line of the top (bottom) layer and the screen printing layer.
d. When generating the drill file, use the default Settings of the Power PCB and do not change anything.
1. Do not rotate the device at any Angle: since the placement machine cannot rotate at any Angle, it can only rotate 90℃, 180℃, 270℃, 360℃. As shown in Figure B below, if the rotation is 1℃, the Angle between the device pin and the pad on the circuit board will be staggered by 1℃ after the placement machine is affixed, thus affecting the welding quality.
2. Problems that should be paid attention to when shorting adjacent pins: The shorting method in Figure a below is not conducive for workers to identify whether the pins should be connected, and it is not beautiful after welding. If the drawing is short connected according to the method of Figure b and c and solder resistance is added, the welding effect will be different: as long as each pin is not connected, the chip will have no short circuit phenomenon, and the appearance is beautiful.
3, about the middle of the chip under the middle of the pad problem: the bottom of the chip in the middle of the pad chip drawing if according to the chip packaging picture in the middle of the pad, it is easy to cause short circuit phenomenon. It is recommended to narrow the middle pad so that the distance between it and the surrounding pin pad is increased to reduce the chance of short circuit. As shown below:
4. The two devices with high thickness should not be closely packed together: as shown in the figure below, the layout of the plate will cause the SMT machine to encounter the previous attached device when attaching the second device, and the machine will detect danger, resulting in automatic power failure of the machine.
5. About BGA: Because BGA package is special, its welding pad is under the chip, and the welding effect can not be seen outside. In order to facilitate the repair, it is recommended to make two positioning holes with Hole Size:30mil on the PCB board, so as to locate the steel mesh (used to scrape the solder paste) during the repair.
And it is suggested that the space should be set aside within a certain range around the BGA to place the device, so as to be able to put the screen scraping paste when repairing.
6. About the color of PCB board: it is recommended not to make it red. Because the red circuit board is white under the red light source of the camera of the patch machine, it cannot be programmed and is not convenient for the welding of the patch machine.
7, about the large device below the small device: some people like the small device in the same layer of the large device, such as: digital tube under the resistance:
This layout will cause difficulties to repair, repair must be removed first, and may cause damage to the digital tube. It is recommended to drain the resistance under the digital tube to the Bottom surface.
8, about the impact of copper coating and welding plate connected to molten tin: because the copper coating will absorb a lot of heat, resulting in solder is difficult to fully melt, thus forming virtual welding.
9. Suggestions on the board and adding process:
Nowadays, more and more engineers can draw, wire and design PCB with software. However, once the design is completed, the welding efficiency can be improved. The author believes that the above factors need to be paid attention to. And cultivate good drawing habits, good communication with the processing plant, is every engineer to consider.