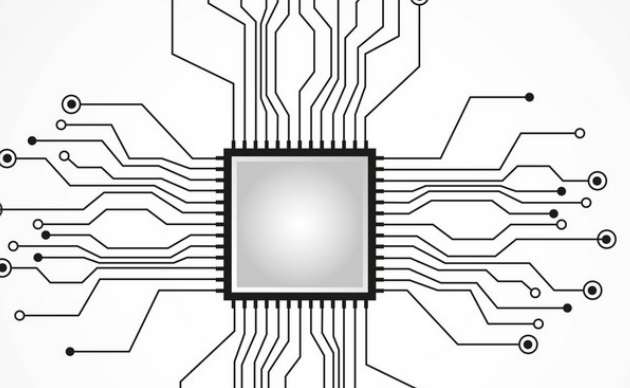
Peak soldering furnace long-termaccumulation of tin slag precipitation float in the use of tin lead solder process, peak soldering furnace due to long-term production after the accumulation of a large number of copper ions, affect the quality of welding, therefore, the need for a period of time to carry out "cleaning" (the tin of the tin furnace all dissolved out, remove the foreign matter attached to the wall of the tin furnace, add a new tin strip). This process was common at the time when tin-lead solders were used. However, in response to the European Union RoHS directive, the electronics factory began to gradually introduce lead-free solder, due to the substantial increase in the cost of solder, this "clean furnace" practice did not continue, more practice is to add pure tin to the tin furnace (does not contain copper alloy tin), in order to dilute the content of copper ions in the old tin furnace solder, and maintain in a certain proportion.
This method of adding new tin to dilute the copper ions of the tin furnace, although it saves the cost of solder, but because of long-term production accumulation, the wall of the tin furnace, especially the bottom of the tin furnace, will be attached to a lot of tin slag and flux residue and other "dirty" things, these "dirty" things under certain conditions, may be removed from the wall after the surface of the tin liquid, part of it may be along the tin flow of the tin wave generator, From the crest nozzle, at this time, if there is a component plate in welding, these "dirty" things will easily stick to the bottom of the component plate, causing the board dirty problem.
Other factors
(1) There was a continuous occurrence of multiple dirty plates, and the bar code number on the component board was analyzed. (Each component board has a unique bar code, which is mainly used to monitor and trace some key points of quality in the manufacturing process. The bar code can be used to count the number of component boards that have passed wave soldering per hour. The wave soldering time of each plate can be checked in the system). It was found that these plates showed a certain regularity, that is, the dirty position of the plates basically appeared on the edge of the plates, and a dirty plate appeared every 5.5 minutes. The analysis confirmed that it should be because the spoon accidentally touched the chain claw when the wave soldering operators were picking up the tin slag, which made the tin slag stick to the chain claw, resulting in the tin slag being transferred to the component plate during production. According to this problem, relevant improvement measures are formulated: it is necessary to stop the operation of the chain claw when cleaning the tin slag. For special reasons, the tin slag needs to be cleaned during the operation of the chain claw, special care should be taken in the operation. At the same time, subsequent stations are required to pay close attention to the edge of the component plate.
(2) The other situation is that the board dirt is relatively concentrated in the middle of the PCB, the area of the board dirt is small, generally in point shape, and the number is relatively small. This situation is generally sandwiched in the convex wave and the wave of tin slag, after the impact of tin flow splash, the convex wave and the wave peak nozzle spacing has been changed larger, so the non-equipment factors caused. After checking the wave peak soldering furnace, it was found that the tin slag flow between the two waves was not smooth, and there was accumulation phenomenon. After stopping the machine for detailed inspection, the original tin slag flow at the outlet end of the two waves was blocked by a mass of sticky foreign matter, resulting in the tin slag flow was not smooth. After cleaning, the normal production was tracked and no plate dirty problem occurred again. After the analysis, the sticky foreign body may be the tin clamp during the production of power board. Due to the weak clamping, it fell into the tin furnace and melted in the high temperature of the tin furnace. According to this accident, relevant improvement measures are formulated: When the component plate with clamped tin strip is produced, when the component plate is found without tin strip at the post inspection station of the wave soldering furnace, the wave soldering operator should be immediately fed back to confirm whether it falls in the tin furnace. Hand insert tin bar station, if found damaged tin bar, can not be used.
3 Conclusion
In addition to the problems caused by the improper operation of wave soldering operators, the design defects of wave welding equipment itself and maintenance should also be paid attention to. Sometimes the dirty problem of the component board may be caused by many reasons, and only partial improvement can not be completely eliminated.
(1) In the usual equipment maintenance process, to ensure that the tin furnace, peak nozzle, motor and conveying guide rail fixed firmly, stable, do not shake, to avoid the tin slag on the tin furnace because of shaking washed to the peak, thus sticking to the surface;
(2) the distance between the flat wave peak nozzle and the spoiling wave peak nozzle should be suitable, the distance is too far, the solder temperature on the plate between the two waves to the solder melting point below, there will be solidification phenomenon, affecting the welding quality, the distance between the two waves is too close, it is easy to wash each other, so that the tin slag between the two waves upstream to the peak above, stick to the surface;
(3) After long-term use of tin furnace, tin slag, flux residue and PCB oxide will be stuck on the furnace wall, which must be cleaned regularly to ensure clean. Otherwise, "dirty" things more, easy to be washed to the crest, stick to the surface.