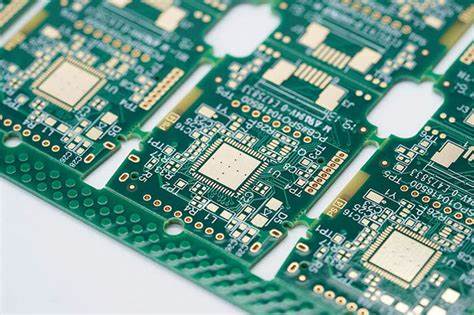
PCB assembly in the medical industry
Printed circuit boards (PCBs) play an important role in healthcare and medicine. As the industry continues to innovate to bring the best technology to patients and their caregivers, more and more research, treatment and diagnostic strategies are moving towards automation. Therefore, more jobs involving PCB assembly are needed to improve medical devices in the industry.
As the population ages, the importance of PCB assembly in the medical industry will continue to grow. Currently, PCBs play an important role in medical imaging equipment such as MRIs and cardiac monitoring equipment such as pacemakers. Even temperature monitoring devices and responsive neurostimulators can be implemented with state-of-the-art PCB technology and components. Today, the editor specially invited the technical staff of Jeddobang todiscuss with you the role of PCB assembly in the medical industry.
mobile health
With the advancement of PCB assembly technology, traditional wires and flexible wires have quickly become a thing of the past. In the past, traditional electrical outlets were often used for plugging and unplugging cords and cords, but modern medical innovations allow doctors to care for patients anytime, anywhere.
In fact, the mHealth market was estimated to be worth more than $20 billion as early as the year before last, with smartphones, iPads and other such devices enabling healthcare providers to easily receive and transmit vital medical information as needed. Thanks to advances in mobile medicine, you can better help patients by filling out documents, ordering equipment and medications, and researching certain symptoms or conditions with just a few mouse clicks.
implantable medical device
The use of PCB assembly becomes even more complicated when it comes to implantable medical devices because there is no uniform standard that makes all PCB assemblies compliant. In other words, different implants will achieve different goals under different medical conditions, and the instability of implants will also affect the design and manufacture of PCBs. In any case, a well-designed PCB can enable deaf people to hear with cochlear implants. Some for the first time in their lives.
What's more, patients with advanced cardiovascular disease could benefit from implanted defibrillators because they may be more vulnerable to sudden and unexpected cardiac arrest, which can occur anywhere or Caused by trauma.
Electronic Health Record
In the past, integration of electronic health records has been poor, with many electronic records lacking connectivity of any kind. Instead, each system is a separate system that handles orders, documents, and other tasks in an independent manner. Over time, these systems have been integrated to form a more comprehensive picture, which has allowed the healthcare industry to expedite patient care anTremendous progress has been made in integrating patient information. However, as the future ushers in a new era of data-driven healthcare, the potential for further development is almost limitless. In other words, electronic health records will be used as a modern tool to enable the medical industry to collect data about the population; making it permanent to improve medical success and effectiveness.
Medical PCB manufacturers need to ensure a deep understanding of project requirements when designing, from function, material selection to product life. The design must follow the standards and regulations of the medical industry. In addition, they also need to grasp the design trends of medical PCBs:
smaller and denser
Component placement density for medical devices increases as circuit boards get smaller. Subsequently, board margin errors also decrease, imposing adaptability when manufacturing and designing these PCBs.
High Density Interconnect (HDI) Boards
Smaller boards with advanced features result in paths with tighter interconnections and smaller trace areas. Due to this, HDI is used on many medical boards.
Non-standard shape
Non-standard PCB form factor designs are brought about by the latest trends that focus on self-monitoring health obligations for medical conditions, fitness, and exercises.
Rigid and flexible structure
Flexible electronics, which must be designed with special manufacturing requirements in mind, continue to gain momentum.
To manufacture high-precision and high-quality medical PCBs, the production process must comply with international regulations, and manufacturers should continuously optimize the manufacturing process. For example, they can optimize the medical PCB (radio frequency test) manufacturing industry at one time, and use digital twin technology for PCB development, Potential errors can be identified before the first plate is rolled. By using these manufacturing methods, manufacturing costs will be reduced and production efficiency will be significantly increased.
Medical PCB Assembly
Medical PCB Assembly
A medical PCBA is made by gluing electronic components onto a medical PCB. Multiple electronic components must be assembled on a PCB in order for it to function in a device. Some of the factors that the assembly process primarily relies on are:
Types of Sort Boards
Characteristics of electrical components assembled on boards.
Reasons to use boards
The following are popular assembly techniques used for medical PCB assembly:
HDI / Via-in-Pad Technology
Via-in-pad technology helps to reduce space by about 50% and increase component density on PCB, so it is widely used in small medical devices. In addition, this assembly technology is suitable for PCBs that require high speed and high dissipation.
surface mount technology
Surface Mount Technology, also known as SMT, is an assembly technique used in almost all medical devices. Like the small size of SMT components, it allows us to assemble more components even in a small space. Furthermore, This assembly technology supports automated soldering and assembly, increasing reliability and productivity.
Through hole technology
Through-hole technology is a method of producing electronic circuits in which pin-through-hole (PTH) components are mounted with leads. It is actually the mounting process of inserting leads into drilled holes and soldering electronic components on a printed circuit board.