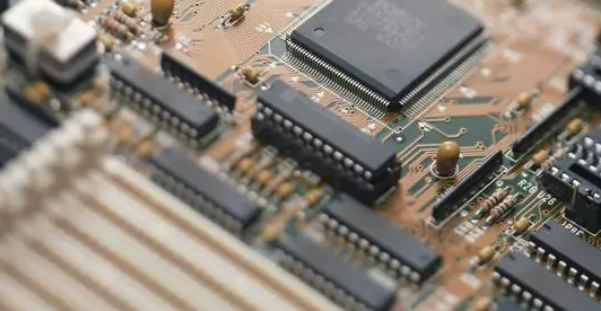
Prevention of the Giavani effect can be traced back to the copper plating process of the previous process, and uniform plating thickness helps to eliminate the hidden dangers of the Giavani effect for high aspect ratio holes and micro-through holes. Excessive corrosion or lateral erosion during film stripping, etching, and tin stripping can contribute to the formation of cracks in which a microetching solution or other solution remains. However, the problem of welding resistance film is still the main reason for the occurrence of Giavani effect, most of the defective plates with Giavani effect have side corrosion or welding resistance film shedding phenomenon, which mainly comes from the exposure development process.
Therefore, if the solder resistance film is "positive foot" after development and the solder resistance film is completely cured, then the problem of the Giavani effect can be almost eliminated. To get a good silver deposition layer, the position of the silver deposition must be 100% metallic copper, each tank solution has a good penetration capacity, and the solution can be effectively exchanged through the hole. In the case of very fine structures, such as HDI boards, it is very useful to install ultrasonic or injectors in the pre-treatment and silvering tank. For the production management of silver deposition process, controlling the rate of microerosion to form a smooth, semi-bright surface can also improve the Javani effect. For original equipment manufacturers (Oems), the design of connecting large copper surfaces or high aspect ratios through holes and thin lines should be avoided as far as possible to eliminate the hidden dangers of the Giavani effect. For the chemical supplier, the silver solution must not be very aggressive, maintain the appropriate pH, the silver precipitation rate is controlled and can produce the desired crystal structure, which can achieve the best corrosion resistance at the thinnest silver thickness.
Corrosion can be reduced by increasing the density of the coating and decreasing the porosity. The use of sulphur-free material packaging, while sealing to isolate the board and air contact, also prevent the air entrained sulfur contact with the silver surface. It is best to store the packaged board in an environment with a temperature of 30 ° C and a relative humidity of 40%. Although the storage period of the silver plate is very long, the principle of first-in-first-out should be followed when storing.
Copper exposure can be reduced or eliminated by optimizing the pre-settling process. In order to achieve this, the copper surface can be examined by a "water breaking" test or a "bright spot" test after micro-etching, and the clean copper surface can maintain a water film for at least 40 seconds. Regular maintenance of the equipment to ensure uniform and stable solution circulation, DOE optimization time, temperature, stirring to obtain the best silver settling operating parameters, thus ensuring the ideal thickness and high quality silver layer. As required, ultrasonic or injectors can be used to improve the wetting ability of the silver sink to micro-pores, high aspect ratio holes and thick plates, while also providing a viable solution for the production of HDI plates. These auxiliary mechanical methods can be applied in the pre-treatment and silver sink to ensure that the hole walls are fully wetted.
Ion contamination can be reduced by reducing the ion concentration of the silver settling solution. For this reason, the ion content of the silver solution should be kept as low as possible without affecting the properties of the solution. The final cleaning section is usually cleaned with deionized water for at least 1 minute, and the ion content (anions and cations) must be regularly tested to meet industry standards. Distinguishing between major sources of contamination, the results of these tests must be recorded and retained.
Microvoids are one of the most difficult defects to prevent because the true cause of their occurrence is not yet known. As mentioned earlier, we already know that some factors seem to cause or accompany microvoids, and the occurrence of microvoids can be controlled by eliminating or minimizing these factors. The thickness of silver deposition is the most significant factor causing microvoids, so controlling the thickness of silver deposition is the first step. Secondly, the micro-erosion rate and silver deposition rate should be adjusted to obtain a smooth and uniform surface structure. It is also necessary to monitor the organic matter content in the silver deposition layer by testing the purity of the silver deposition layer at different time points in the service cycle, and the reasonable silver content should be controlled above 90% (atomic ratio).