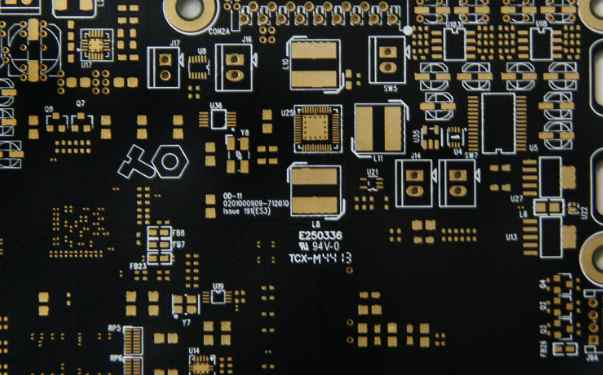
The so-called throwing material means that in the production of seeds, after sucking the material does not stick, but throws the material into the throwing box or other places, or does not suck the material and perform the above one throwing action. Throwing material to form the loss of material, prolongs the production time, reduces the production power, raises the production cost, in order to optimize the production power, reduce the cost, must solve the problem of high throwing rate.
The main reasons and countermeasures of throwing material:
Reason 1: Suction nozzle question, suction nozzle deformation, blockage, damage to form a lack of air pressure, leakage, the formation of suction can not, take material is not correct, identify through but throw material.
Countermeasures: clean and replace the nozzle;
Reason 2: Identification system questions, poor vision, visual or laser lens is not cleaned, there is debris interference identification, improper identification light source selection and intensity, gray level is not enough, and there may be bad identification system.
Countermeasures: Clean and wipe the appearance of the identification system, adhere to clean and no debris stains, adjust the intensity and gray level of the light source, and replace the components of the identification system;
Reason 3: Azimuth question, take the material is not in the central orientation of the material, take the material height is not correct (generally 0.05MM after hitting zero) and form a deviation, take the material is not correct, there is deviation, identification with the corresponding data parameters do not match and be discarded by the identification system as invalid material.
Countermeasures: adjust the bearing of the material;
Reason 4: vacuum doubt, lack of air pressure, vacuum pipe channel is not smooth, there are guides blocking the vacuum channel, or vacuum leakage to form a lack of air pressure and can not afford to take material or fall on the way to paste after picking up.
Countermeasures: Adjust the pressure steep slope to the required pressure value of the equipment (such as 0.5~ 0.6Mpa), clean the pressure pipeline, and repair the leakage path;
Reason 5: program questions, the modified program component parameters are not set correctly, with the incoming material scale, brightness and other parameters do not form an identifiable but lost.
Countermeasure: Modify component parameters, search for the best parameter setting of components;
Reason 6: The doubt of incoming material, incoming material is irregular, and it is unqualified products such as pin oxidation.
Countermeasures: IQC should test incoming materials and contact component suppliers;
Cause 7: The feeder is in doubt, the feeder's orientation is deformed, the feeder is fed poorly (the feeder's spine gear is damaged, the material belt hole is not stuck on the spine gear of the feeder, there are foreign objects under the feeder, the spring is aging, or the electrical is poor), the material is not taken or the material is thrown, and the feeder is damaged.
Countermeasures: Adjust the feeder, clean the feeder platform, replace the broken parts or the feeder.
When there is a throwing phenomenon to solve, you can first ask the site personnel, after describing, and then according to the investigation and analysis, directly find the question, so that it can be more effective to find the question, to solve, to improve the production power, but not too much to occupy the machine production time.
The reason of tin unsaturation on SMT circuit board was analyzed
Analysis of the reasons why the solder joint is not full:
1, PCB pad or SMD welding site has serious oxidation phenomenon;
2, the activity of the flux in the solder paste is not enough to completely remove the oxidizing substances in the PCB pad or SMD welding site;
3, reflow welding zone temperature is too low;
4. The wettability of the flux in the solder paste is not good;
5, if there are some solder joints on the tin is not full, it may be that the solder paste before use is not fully stirred flux and tin powder is not fully integrated;
6. The amount of solder paste in the solder joint is not enough;
7. In over-reflow welding, the preheating time is too long or the preheating temperature is too high, resulting in the failure of the flux activity in the solder paste;
Analysis of excessive chloride ion consumption in PCB copper plating
At present, with the development of printed circuit boards to high density and high precision, more stringent requirements are put forward for sulfate copper plating process, and various factors in the copper plating process must be controlled at the same time in order to obtain high quality coating. In view of the phenomenon of excessive chloride ion consumption in the copper plating process, the reasons for excessive chloride ion consumption are analyzed below.
The antecedents of excessive chloride ion consumption are:
When copper plating, the low current area of the circuit board surfaceappears "dull" phenomenon, and the chlorine concentration is low; Generally, after adding hydrochloric acid, the "dull" phenomenon of the coating in the low current density area of the plate can disappear, the chloride ion concentration in the plating solution can reach the normal range, and the plate coating is bright. If a large amount of hydrochloric acid is added to solve the "dull" phenomenon of the coating in the low current density area, it is not necessarily caused by too low chloride ion concentration, and the real reason needs to be analyzed. If you take to add a large amount of hydrochloric acid: one, may have other consequences, two to increase production costs, is not conducive to enterprise competition.
"Low current density area coating luster" Reasons:
By adding a large amount of hydrochloric acid to eliminate the "low current density area coating is not bright" phenomenon, indicating that if there are too few chloride ions, it is necessary to add hydrochloric acid to increase the concentration of chloride ions to reach the normal range, so that the coating in the low current density area is bright. What if you have to multiply hydrochloric acid to get the chloride concentration to the normal range? What's consuming a lot of chloride? The concentration of chloride ions is too high, and the brightener will be consumed quickly. It shows that chloride ions will react with brightener, and excess chloride ions will be consumed. In turn, excess brightener also consumes chloride ions. Because too few chloride ions and excessive brightener are the main reasons for the plating in the low current density area is not bright, it can be seen that the main reason for the excessive consumption of chloride ions in copper plating is the concentration of brightener is too high.