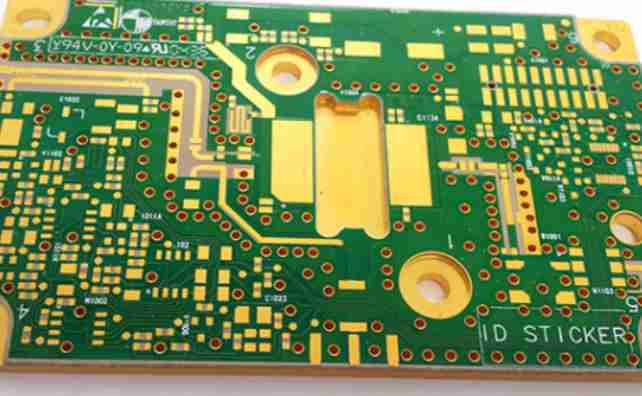
The purpose of the modular and system integration technology is to propose optimized and improved solutions for the three basic requirements of the LED mounter: speed, accuracy and flexibility. Flexible modular technology emphasizes the portability, interoperability, scaling and configurability of equipment, and provides the reconfiguration and openness of equipment control platform to control requirements, so that it can simply and efficiently construct and complete the surface mount equipment with specific requirements, and improve assembly productivity.
The motor uses a lightweight design concept
It can greatly reduce the weight of the moving part of the machine, so that the power consumed during the operation of the machine is also greatly reduced to only 1/4 of the ordinary placement machine, and the power consumption can reach less than 1/4 of the ordinary placement machine; The LED placement machine does not require high placement accuracy, but requires faster speed. At present, there are several professional LED mounters in China, which can be divided into 4, 6 and 8 devices according to different speeds. You can refer to the LED640, LED660 V and LED680 V LED mounters for actual understanding. The number in the middle represents the number of stickers. The higher the number, the higher the speed. The mainstream application of LED placement machine should be able to mount a large area of PCB board, to meet the online requirements, so as to ensure speed.
The development trend of LED chip machine
LED mounter plays a very important role in the production and manufacturing process, is the largest investment in the contemporary mainstream electronic assembly technology production equipment, the most advanced technology, and the most influential equipment on the production capacity and production efficiency of the SMT production line. In fact, the most faults and speed bottlenecks are largely from the mounting process, so the development of the mounting machine equipment is the most eye-catching. At present, the number and advanced degree of the SMT machine has become a key indicator of the electronic manufacturing capability of a company, region or country. The following is the development trend of the SMT machine at this stage.
LED placement machines are developing in the direction of higher accuracy
The accuracy of the placement machine refers to the mechanical accuracy of the navigation movement of the X and Y axes and the rotation accuracy of the Z axis of the placement machine. The chip mounter uses precision mechatronics technology to control mechanical motion to grab the components from the feeder and attach them to the circuit board accurately and reliably after calibration mechanism alignment. In order to produce products with higher performance, one of the first major challenges is to improve the mounting accuracy of the mounter more likely. The following begins with the LED manufacturing process to tell the revolutionary impact that the LED mounter with higher precision may have on the future production of LED.
In the ordinary LED packaging technology, the connection between the chip electrode and the support pin is generally achieved by the way of gold wire interconnection, but the gold wire fracture has been one of the common reasons for failure. The abnormality of the gold wire in LED lighting applications is the culprit of such common problems as dead lights and large light decay. Dead lights can be roughly divided into two situations, one is not bright at all, the other is hot state is not bright cold state, or flicker. The main reason for not shining is that the electrical circuit is open, and the reason for flickering is because the gold wire is virtual welding or poor contact.
With the introduction of inverted welding technology, the connection of the two can be connected by a more stable metal bump welding ball, saving costs and greatly improving reliability and heat dissipation. LED has the advantages of long life, with the reverse welding technology than the traditional use of gold wire interconnect packaging technology can better play the advantages of LED, LED flip welding technology, to achieve single chip and multi-chip module gold wire, no solid adhesive packaging, with high brightness, high light efficiency, high reliability, low thermal resistance, good color consistency and many other advantages.
LED gold wire packaging is commonly known as "no package" and "free package" in the industry. This process uses the flip chip to directly SMT the circuit board, omits the SMD packaging process, and directly attaches the flip chip to the circuit board or the carrier by SMT. Because the chip area is much smaller than the SMD device, this process requires very precise design.
The future LED placement machine in the basic conditions of improving the accuracy, directly applied to the flip packaging process, which will be a small revolution in the LED process, can save a lot of packaging costs, and greatly improve the production cost and shorten the production cycle, so that LED products are really high performance and low price to enter the general lighting market. The direct application of LED mounter to the LED process has the potential to become the trend of future technology.
LED chip machine is developing towards high efficiency production
One of the most important features of today's society is competition. It is this kind of competition that inspires people to explore and innovate. It is this competition that drives the rapid development of science and technology. Driven by the full swing of the LED lighting market, the efficient work of the LED placement machine will inevitably become the embodiment of its core competitiveness. High efficiency is to improve production efficiency, reduce working hours, increase production capacity, and create economic benefits. The main methods to improve efficiency on the current basis are: strengthen the automation performance of the LED placement machine and improve the equipment structure and working mode.