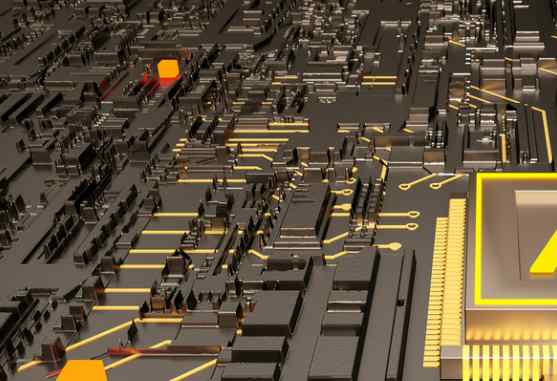
At present, the typical process of printed circuit board (PCB) processing uses the "graphic plating method". That is, a layer of lead-tin corrosion resistance layer is pre-plated on the copper foil part that needs to be retained on the outer layer of the board, that is, the graphic part of the circuit, and then the rest of the copper foil is corroded by chemical means, which is called etching.
It should be noted that there are two layers of copper on the board at this time. In the outer etching process, only one layer of copper must be completely etched away, and the rest will form the final required circuit. This type of graphic plating is characterized by a copper-coated layer that exists only under the lead tin resist layer. Another process method is to coat the entire plate with copper, and the part outside the sensitive film is only tin or lead tin resist layer. This process is called "full plate copper plating process". Compared with graphic plating, the biggest disadvantage of full plate copper plating is that the surface of the plate must be plated twice and they must be corroded away during etching. Therefore, when the wire width is very fine, a series of problems will arise. At the same time, side corrosion will seriously affect the uniformity of the lines.
In the processing process of the outer circuit of the printed board, there is another method, which is to use the sensitive film instead of the metal coating as the corrosion resistance layer. This method is very similar to the inner layer etching process, you can see etching in the inner layer making process.
At present, tin or lead tin is the most commonly used corrosion resistance layer, used in the etching process of ammonia etching agents. Ammonia etching agent is a commonly used chemical liquid, which does not react with tin or lead tin. Ammonia etching agent mainly refers to ammonia water/ammonia chloride etching solution. In addition, ammonia/ammonia sulfate etching solution can also be bought in the market.
Sulfate based etching solution, after use, the copper in it can be separated by electrolysis, so it can be reused. Due to its low corrosion rate, it is generally rare in actual production, but it is expected to be used in chlorine-free etching. Some people experimented with the use of sulfuric acid-hydrogen peroxide as an etching agent to corrode the outer pattern. For a number of reasons, including economic and liquid waste treatment aspects, this process has not been widely adopted in a commercial sense. Further said, sulfuric acid-hydrogen peroxide, can not be used for lead tin corrosion resistance layer etching, and this process is not the main method in the production of PCB outer layer, so most people rarely ask.
2. Etching quality and previous problems
The basic requirement for etching quality is to be able to completely remove all copper layers except under the resist layer, and that's it. In a strict sense, if it is to be precisely defined, then the etching quality must include the consistency of the wire width and the degree of side erosion. Due to the inherent characteristics of the current corrosion fluid, not only downward but also in all directions to produce etching, so side erosion is almost inevitable.
The problem of side erosion is one of the etch parameters that is often discussed. It is defined as the ratio of side erosion width to etching depth.
It's called an etching factor. In the printed circuit industry, it varies widely, from 1:1 to 1:5. Obviously, a small side etching degree or a low etching factor is the most satisfactory.
The structure of the etching equipment and the different composition of the etching fluid will have an impact on the etching factor or the degree of side erosion, or in optimistic terms, it can be controlled. Some additives can reduce the degree of side corrosion. The chemical composition of these additives is generally a trade secret, and the respective developers are not disclosed to the outside world. As for the structure of the etching equipment, the following chapters will be devoted to the discussion.
In many ways, the quality of etching has existed long before the printed board entered the etching machine. Because there is a very close internal relationship between the various processes or processes of printed circuit processing, there is no process that is not affected by other processes and does not affect other processes. Many of the problems identified as etching quality actually exist in the process of film removal and even before. For the etching process of the outer layer graphics, because the "pour stream" image reflected in it is more prominent than most printed board processes, many problems are finally reflected in it. At the same time, this is also because the etching is the last link in a long series of processes that start with the self-coating film, after which the outer pattern is transferred successfully. The more links there are, the greater the chance of problems. This can be regarded as a very special aspect of the printed circuit production process.