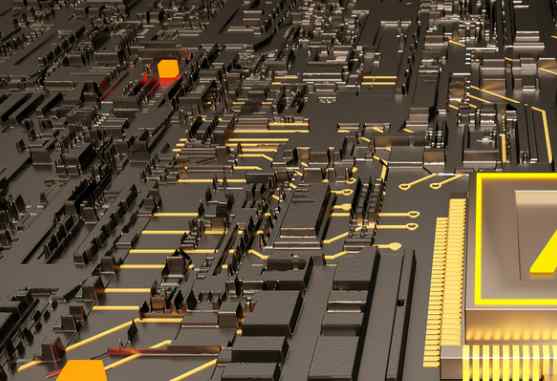
In the PCB manufacturing process, welding work is essential. It not only requires the components to be fixed on the PCB board, but also requires that the solder joints must be firm and smooth, so the quality of welding technology directly affects the success of PCB board production or not, so welding technology is the basic skills that every PCB board maker must master, and now pcb manufacturers will introduce the main points of welding:
1. Welding method
Components must be clean and tinned, electronic components are stored in the air, due to the role of oxidation, the element pin is attached with an oxide film, while there are other dirt, before welding can be scratched off the oxide film with a knife, and immediately coated with a layer of solder (commonly known as tin), and then welding. After the above treatment, the component is easy to weld, and it is not easy to appear virtual welding phenomenon.
2. Welding temperature and welding time
When welding, the temperature of the soldering iron should be higher than the temperature of the solder, but it should not be too high, so that the soldering iron head contact the rosin just smoke. The welding time is too short, the temperature of the solder joint is too low, the solder joint is not sufficiently melted, the solder joint is rough and easy to cause virtual welding, and the welding time is too long, the solder is easy to flow, and it is easy to overheat the components and damage the components.
3. Pay attention to the position of the soldering iron and welding points
The soldering surface of the electric soldering iron is used to contact the welding point, so that the heat transfer area is large and the welding speed is fast.
4. Check after welding
After welding, it is necessary to check for missing welding, virtual welding and short circuit of components caused by solder flow. Welding is more difficult to find, can be held by tweezers gently pull the element pin, if found shaking should immediately repair welding.
The weldability of PCB circuit board and its status
The pcb circuit board is the support body of electronic components and the electrical connection provider of electronic components. According to the number of circuit layers can be divided into single panel, double panel and multi-layer board. The common multi-layer board is generally 4-layer board or 6-layer board, and the complex multi-layer board can reach more than ten layers.
The weldability of PCB circuit board and its status:
In order to ensure that the printed board can have a relatively long shelf life and its surface can maintain a good wetting effect on the solder, it is necessary to carry out solderability treatment on the surface. The characteristic of a metal surface wetted by molten solder is called solderability. This is a large and complex problem, in order to ensure that the printed board can have a relatively long shelf life and its surface can maintain a good wetting effect on the solder, the surface must be solderability treatment.
On the surface of the printed board that has just been made, if it is light copper, it is easy to absorb dust, moisture and various gases in the air due to its large surface tension, and improper operation also makes it contaminated with sweat and oil, while oxygen in the air is also easy to generate metal oxides (CuO) to reduce the wettability of the copper surface.
Three states of solder after melting on the metal surface:
1, non-wetting molten solder does not adhere to the metal surface, exposing the base metal, this phenomenon is called non-wetting. Non-wetting indicates poor weldability of the metal.
2, wetting molten solder on the metal surface to form a uniform, smooth, non-breaking thin layer of solder called wetting. Wetting indicates that the solder has good weldability on the metal surface.
3, semi-wetting molten solder forms irregular bumps on the metal surface, but does not expose the base metal phenomenon is called semi-wetting. Semi-wetting is somewhere in between, and metal weldability is not good.
After drilling the printed circuit, making the circuit pattern and shape processing, in order to improve the weldability of the printed circuit and prevent or delay the weldability of the pad, some treatment must be done.
PCB board patch after the hole is not through the cause
After the PCB board is placed, many users will encounter the situation of impassability. Under what circumstances will the hole be blocked? According to the summarized experience, the following to share with you the causes of the patch caused by the hole. Of course, this reason on the one hand is the reason for the production of circuit board manufacturers, and on the other hand is the reason for SMT.
1. Defects caused by drilling
PCB board production of the board is epoxy resin glass fiber material. FR4. After the plate is drilled, there will be a layer of dust in the hole. Especially boreholes larger than 0.3MM. If the dust is not cleaned, the place where the dust is cured cannot sink copper, which will cause the hole to be blocked. Drilling caused by bad, if the PCB board has been tested, this situation can be tested out. This bad PCB manufacturers can do scrap treatment.
2. Bad caused by copper sinking
The first choice is that the time of sinking copper is too short. The hole copper is not full, and the hole copper melts away when tinning, resulting in bad condition. Most of this appears in the hole below 0.3MM, followed by the circuit board requires too much current, and the copper is not thickened. Too much current melts the hole copper after electrification, resulting in bad. Therefore, if there is a PCB that needs too much current, it must be told to thicken the copper at the time of production.
3.SMT tin or flux quality and technology caused by bad
This kind of situation mostly occurs in the hole of the plug-in. The tin used by SMT manufacturers is not pure, there are too many impurities and the quality of the flux is poor. Solder and tin welding is not good, which is easy to cause virtual welding, and the components do not work. In addition, SMT has technical problems, and the flow stop time in the tin furnace during welding is too long, resulting in the hole copper melting, resulting in the hole impassability.
As a power supply product, PCB circuit boards can be seen everywhere in life. This requires manufacturers to strictly put the quality in production, understand all the failure of the product, deal with it early, and reduce economic losses.