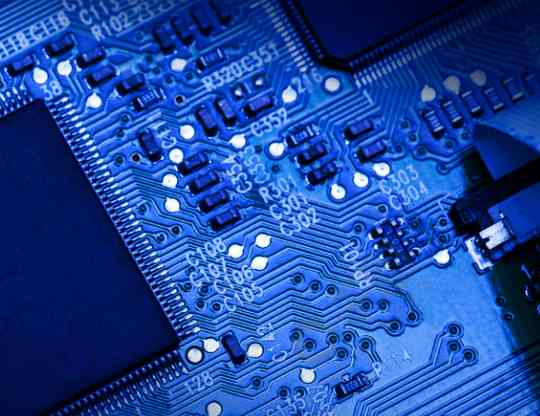
With the development of electronic technology, electronic components are developing in the direction of miniaturization and high-density integration. BGA components have been more and more widely used in SMT assembly technology, and with the emergence of uBGA and CSP, the difficulty of SMT processing and assembly is becoming greater and greater, and the process requirements are becoming higher and higher. Due to the difficulty of BGA repair, it is a task for all SMT engineers to achieve good welding of BGA.
What Should Be Paid Attention To In SMT Patch Processing BGA
BGA Preservation and Use
The BGA component is a highly temperature-sensitive component, so the BGA must be stored under constant temperature and dry conditions, and the operator should strictly follow the operating process to avoid the components being affected before assembly. In general, the ideal storage environment for BGA is 200C-250C, and the humidity is less than 10%RH(nitrogen protection is better).
In most cases, we will note the moisture-proof treatment of BGA before the packaging of the components is opened, and we should also note the time that the components can not be exposed during the installation and welding process after the packaging of the components is beaten, in order to prevent the components from being affected and resulting in a decline in the welding quality or a change in the electrical performance of the components. The following table is a classification of humidity sensitive grades, which shows the corresponding time during assembly when components must be installed and welded once the sealed moisture-proof package is opened. In general, BGA is a humidity sensitive grade above 5.
If the components are stored in nitrogen, the use time can be relatively extended. About every 4-5 hours of dry nitrogen action can extend the air exposure time by 1 hour.
In the process of assembly, we often encounter such a situation, that is, after the package of components is opened, it cannot be used within the corresponding time, and the exposure time exceeds the time specified in Table 1. Then before the next use, in order to make the components have good weldability, we recommend baking the BGA components. Baking conditions: temperature 125 degrees, relative phase humidity ≤ 60%RH.
The baking temperature should not exceed 125 degrees at least, because the high temperature will cause the metallic structure change at the connection between the tin ball and the components, and when these components enter the reflow stage, it is easy to cause the disconnection between the tin ball and the component package, resulting in SMT assembly quality problems, we will think that the quality problems caused by the components themselves. However, the temperature of fruit baking is too low, it can not play the role of dehumidification. If conditions permit, we suggest baking the components before assembly, which is conducive to eliminating the internal moisture of BGA, improving the heat resistance of BGA, and reducing the impact of thermal shock on the components when they enter reflow welding. BGA components are removed after baking and cooled for half an hour before assembly.
BGA Welding Process Requirements
In the assembly process of BGA, every step and every tool will have an impact on the welding of BGA.
Solder Paste Printing
The quality of solder paste is an important link that affects the surface mounting production. The selection of solder paste usually considers the following aspects: good printability, good weldability, good weldability and low residue. In general, the alloy composition of our solder paste is low residue type solder paste with 63% tin and 37% lead.
It does not mean that the smaller the solder paste powder, the better, because from the welding effect, the solder paste with large tin powder particles is better than the solder paste with small tin powder particles. Therefore, we should consider all factors comprehensively when choosing. Due to the small pin space of BGA and the small opening of the screen template, we use a welding paste with a diameter below 45M to ensure a good printing effect.
The printed screen template is generally made of stainless steel. Because the pin spacing of BGA components is small, the thickness of the steel plate is thin. The thickness of the general steel plate is 0.12MM-0.15MM. The opening of the steel plate depends on the condition of the components, and the opening of the steel plate is usually slightly smaller than the pad.
For example, a BGA with an external size of 35MM and a unique 1.0MM between pins has a welded rib diameter of 23MIL. We generally control the size of the opening of the steel plate at 21MIL.