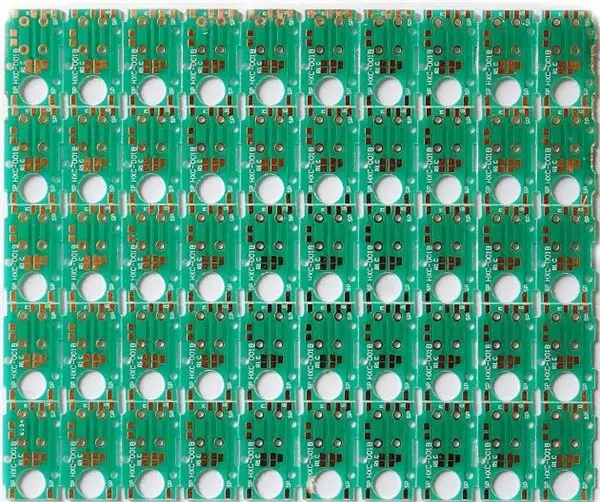
Matters needing attention in pcb soft board design
The most important function of Hot Bar reflow is to melt the solder paste that has been printed on the electronic printed circuit (PCB) by using the Hot pressing head to connect two independent electronic parts. The most common is to weld the flexible flat cable (FPB) to the electronic printed circuit (PCB).
Since the hot press head of the Hot Bar machine is the only heat source, when the hot press head is pressed on the flexible flat cable (FPC), the heat must be transmitted downward to the electronic printed circuit board (PCB) to melt the solder paste that has been printed on the electronic printed circuit board. Therefore, the flexible flat cable must have the function of heat conduction.
Generally speaking, it is the most common design of heat conduction function to make plating holes or vias on the solder pad of, as shown in the structure below. It is recommended that there should be three Vias or 2.5 Vias on the welding pad of each FPC. Another advantage of making electroplated holes is that during the hot pressing welding of molten tin, excess tin can overflow from the electroplated holes to avoid short circuit between pads.
The flexible flat cable should be pasted with double-sided adhesive tape to fix the flexible flat cable on the electronic printed circuit board, because the operator is unlikely to hold the FPC with his hands until the Hot Bar reflow is completed. In addition, the problem of unstable quality will also occur.
To sum up the design requirements of FPC, it is better to have three plated holes or through holes on the welding pad of each FPC, and at least two+half plated holes or through holes.
Stick double-sided adhesive tape on the side of FPB pasted on the electronic printed circuit board. The thickness of double-sided adhesive tape should be less than 0.15 mm. The distance from the edge of FPC welding pad to double-sided adhesive tape should be 0.20 mm.
The recommended size design of hot bar soft board is as follows:
The hole diameter of the through hole is 0.4mm
1.2mm from the center to the center of the through hole
The distance from the center of the welding pad to the center is 1.8mm
Width of welding pad is 0.9mm
In order to avoid breaking the flexible flat cable due to stress concentration, it is strongly recommended to stagger the edge of the cover film (Polymer) of the flexible flat cable. Refer to the following structure diagram of the flexible flat cable.
In order to cooperate with Hot Bar operation and avoid pressure or damage to parts, the following is the recommended limit size of part location:
The minimum dimension from the part to the front edge of FPC is 2.0mm.
The minimum dimension from the part to the left and right edges of FPC is 3.0mm.
When FPC extends outward, a minimum space of 5.0mm should be reserved so that FPC can be stuck on the PCB. It can also be considered to make positioning holes on FPC and design alignment pins on the hot pressing fixture for positioning, which can save space on double-sided adhesive tape and printed circuit board, but accuracy must be considered.
The minimum size from the part under FPC to the rear edge of FPC is 10.0mm (to ensure that the double-sided adhesive can be stuck on the printed circuit board).