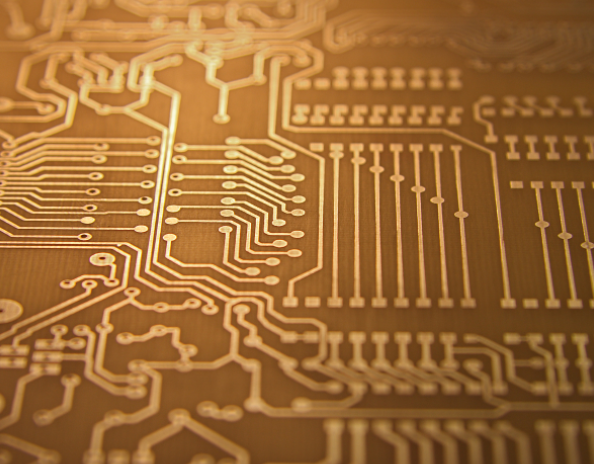
Basic information should be paid attention to in wearable PCB design
Due to its small size, there is almost no standard for the growing wearable Internet of Things market with ready-made printed circuit boards Before these standards can be used, we must rely on the knowledge learned from board level development and manufacturing experience to think about how to apply them to unique emerging challenges There are three aspects we should pay special attention to: circuit board surface information, RF/microwave design, and RF transmission line
Printed circuit board
PCB board cloth
PCB is usually composed of laminate, which may be fabricated from fiber reinforced epoxy (FR4), polyimide or Rogers information, or other laminates The insulating material between different layers is called prepreg Wearable devices need a high level of reliability, so when PCB designers are faced with the choice of using FR4 (a cost effective PCB manufacturing material) or more advanced and more expensive materials If wearable PCB applications require high-speed and high-frequency data, FR4 may not be an option The dielectric constant (Dk) of FR4 is 4.5, the dielectric constant of the more advanced Rogers 4003 series data is 3.55, and the dielectric constant of the brother Rogers 4350 is 3.66
The dielectric constant of a stack refers to the ratio of the capacitance or energy between a pair of conductors near the stack and the capacitance or energy between a pair of conductors in vacuum At high frequencies, the loss is small. Roger 4350, with a dielectric constant of 3.66, is more suitable for higher frequency applications than FR4 with a dielectric constant of 4. 5. Under normal conditions, the number of PCB layers of wearable devices varies from 4 to 8 The layer structure principle is that if it is an 8-layer PCB, it should provide enough grounding and power supply surfaces and clamp the wiring layer With this kind of pipe, the ripple effect in crosstalk is preserved and electromagnetic interference (EMI) can be significantly reduced In the circuit board layout design stage, the floor plan generally places a large stratum near the distribution floor This will produce very low ripple effect, and system noise can be reduced to almost zero This is particularly important for RF subsystems Compared with Rogers data, FR4 has a high dispersion factor (Df), especially at high frequencies For the FR4 stack with higher performance, the Df value is about 0.002, which is an order of magnitude better than the conventional FR4 stack But Rogers' stack is only 0.001 or less When FR4 data is used in high frequency applications, there is a significant difference in insertion loss Insertion loss is defined as the power loss, Rogers, or other data in the signal transmission from point A to point B when FR4 is used
Manufacturing problems
Wearable PCB needs more strict impedance control, which is an important factor of wearable devices, because impedance matching can achieve clearer signal transmission In the early stage, the standard tolerance of signal transmission track is ± 10% This quota is obviously not good enough for today's high-frequency high-speed circuits The current requirement is ± 7%, and in some cases even ± 5% or less This parameter, as well as other variables, has a particularly strict impedance control, which will seriously affect the manufacturing of these wearable PCBs, thus limiting the number of businesses that can manufacture them The dielectric constant tolerance of laminates made from Rogers UHF data is usually kept at ± 2%, and some products can even reach ± 1% Rogers has very low insertion loss in these two kinds of data Compared with traditional FR4 data, the transmission and insertion loss of Rogers stack is reduced by half In most cases, cost is a problem However, Rogers can provide relatively low loss high-frequency stacking efficiency at an acceptable price For commercial applications, Rogers can be combined with epoxy resin based FR4 to produce mixed PCB. Some layers use Rogers data and others use FR4. When selecting Rogers stack, frequency is the primary consideration When the frequency exceeds 500MHz, PCB designers tend to choose Rogers data, especially RF/microwave circuits, because when the above trajectory is strictly controlled by impedance, these data can provide higher efficiency Compared with FR4 data, Rogers data also has lower dielectric loss, and their dielectric constant is stable in a wide frequency range In addition, Rogers data can provide ideal low insertion loss performance for high frequency operation The efficiency of thermal expansion (CTE) of Rogers 4000 series materials has excellent dimensional stability This means that when the circuit board is in the cold state, the thermal expansion and contraction of the circuit board can be kept at the stability limit under higher frequency and higher temperature cycling. Compared with FR4, the thermal reflux and extreme thermal reflux loop For the hybrid stack, Rogers and high-performance FR4 can easily mix together to use the same manufacturing technology and technology. In conclusion, it is relatively easy to achieve high manufacturing output Rogers stacking does not require a professional through-hole preparation process Conventional FR4 cannot achieve very reliable power efficiency, but high-performance FR4 data do have good reliability characteristics. For example, higher Tg is still relatively low in cost, and can be used in a variety of applications, from simple audio design to complex microwave applications
RF/Microwave Design Considerations
Portable technology and Bluetooth paid the way for RF Today's frequency range is becoming more and more dynamic A few years ago, very high frequency (VHF) was defined as 2GHz~3GHz But now we can see ultra-high frequency (UHF) applications in the range of 10GHz to 25GHz. Therefore, it is applicable to wearable device PCB boards. The RF part needs to pay more attention to the wiring problems, separate signals, and keep the traces that generate high-frequency signals away from the ground Other considerations include: provision of bypass screening procedures, adequate decoupling capacitors, grounding, transmission line and return line designs are almost equal The bypass filter suppresses the ripple effect of noise content and crosstalk The decoupling capacitor needs to be placed closer to the pin of the device carrying the power signal High speed transmission lines and signal loops require a ground plane between power plane signals to eliminate noise signal jitter At higher signal speeds, small impedance mismatches can cause imbalance between transmitted and received signals, leading to distortion Therefore, special attention must be paid to impedance matching problems related to RF signals, with high speed and special tolerance RF transmission lines need controlled impedance to transmit RF signals from specific IC substrates to PCB boards These transmission lines can be implemented externally, at the top and bottom layers, or designed in the middle layer The methods used in PCB RF design layout are microstrip, floating stripline, coplanar waveguide or grounding The microstrip line consists of a fixed length of metal or track and the whole ground plane or part of the ground plane directly below it The characteristic impedance in general microstrip line structure is 50 Î © To 75 Î ©.
Suspended stripline is another method of wiring and noise suppression The line consists of fixed width wiring on the inner layer and large ground plane above and below the central conductor The ground plane is clamped between the power planes, which provides a very effective grounding effect This is the preferred method for RF signal routing on wearable devices PCB boards Coplanar waveguides can provide better isolation near RF lines and lines requiring close tracking The medium consists of a section of central conductor and ground plane on one side or below The method of transmitting RF signal is suspended stripline or coplanar waveguide These two methods provide better isolation between the signal and the RF trace It is recommended to use the so-called "through-hole fence" on both sides of the coplanar waveguide This method provides a row of grounding vias on each metal grounding plane of the central conductor The main runway in the middle is surrounded by fences on both sides. In summary, it provides a shortcut to the following strata for the return current This method reduces the noise level associated with high ripple effects of RF signals 4 5 The same data as the prepreg FR4, while the dielectric constant of the prepreg from the microstrip, stripline, or offset stripline is about 3.8 to 3.9. In some equipment using ground plane, the blind hole can be used to improve the decoupling efficiency of the power capacitor and provide a shunt path from the equipment to the ground The grounding shunt path can shorten the length of the through-hole, which has two purposes: you can not only create shunt or grounding, but you can reduce the transmission distance of equipment with smaller grounding, which is an important RF design factor of PCB