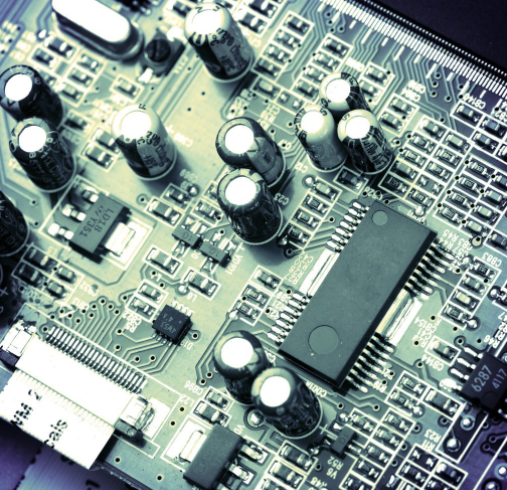
PCB Etching Process and Process Control
The process PCB from the light-emitting panel to the display circuit diagram is a relatively complex physical and chemical reaction process This paper analyzes its one-step corrosion At present, the typical process of PCB (PCB board) is "graphic electroplating". That is, the copper foil part that needs to be reserved on the outer layer of the circuit board is pre coated with lead tin anti-corrosion coating, that is, the pattern part of the circuit, and then chemically etches the remaining copper foil, which is called etching
PCB board
1. Etch Type
It should be noted that there are two layers of copper on the circuit board during the etching process. In the outer etching process, only one layer of copper must be completely etched, and the rest will form the final required circuit The feature of this pattern electroplating is that the copper plating layer only exists below the lead tin resistance layer Another process is to plate copper on the whole circuit board, and the part outside the photosensitive film is only tin or lead tin resist This process is called "full plate copper plating process" Compared with pattern electroplating, the disadvantage of copper plating on the whole circuit board is that all parts of the circuit board must be copper plated twice and must be corroded during the etching process Therefore, when the wire width is very thin, a series of problems will occur At the same time, side corrosion will seriously affect the uniformity of the circuit In the processing technology of external circuit of printed circuit board, another method is to use photosensitive film instead of metal coating as the resist layer This method is very similar to the inner layer etching process. You can refer to the etching in the inner layer manufacturing process At present, tin or lead tin is a commonly used anti-corrosion coating for the etching process of amino etchant Amino etchant is a common chemical liquid, which has no chemical reaction with tin or lead tin Ammonia etchant mainly refers to ammonia/ammonium chloride etching solution In addition, ammonium sulfate etching chemicals are also available on the ammonia/market After using sulfate etching solution, the copper in it can be separated by electrolysis and reused Because of its low corrosion rate, it is usually rare in practical production, but it is expected to be used for chlorine free etching Someone tried to use hydrogen sulfate as an etchant to etch the outer pattern For many reasons, including economy and waste liquid treatment, this process has not been widely used commercially In addition, sulfuric acid hydrogen peroxide cannot be used for the etching tin resistance of lead. This process is not the main method for producing the outer layer of printed circuit board, so most people pay little attention to it
2. Etching quality and past problems
The basic requirement for etching quality is to completely remove all copper layers except those below the resist layer Strictly speaking, if defined, the etching quality must include the consistency of wire width and side etching degree Due to the inherent characteristics of the current etching solution, this will produce etching effects not only in the downward direction, but also in the left and right directions. Side etching is almost inevitable Undercut is one of the etching parameters often discussed It is defined as the ratio of undercut width to etching depth, which is called etching factor In the printed circuit board industry, it has a wide range of changes, from 1:1 to 1:5. Obviously, smaller undercut or lower etching coefficient is satisfactory The structure of etching equipment and etching solutions with different components will affect the etching factor or the extent of side etching, or optimistically, it can be controlled The use of certain additives can reduce the degree of side erosion The chemical composition of these additives is usually a trade secret, and their respective developers have not disclosed it to the public In many ways, etching quality exists long before the printed board enters the etching machine Because in various processes or PCB processing, there is no process that is not affected by other processes and does not affect other processes Many problems identified as etching quality actually exist in the process of removing films, even before As for the etching process of the outer pattern, because the "countercurrent" phenomenon it represents is more prominent than most PCB processes, it reflects many problems At the same time, this is also because etching is part of a series of processes starting from self adhesion and photosensitivity, after which the outer pattern is successfully transferred The more links, the greater the possibility of problems This can be regarded as a very special aspect of the PCB production process Theoretically, the printed circuit board will enter the etching stage later. During the processing, the printed circuit board will adopt the pattern electroplating method. The ideal state should be: the total thickness of copper and tin or copper and lead tin should not exceed the electroplating photosensitive film. The thickness of the electroplated pattern is completely blocked and embedded by the "walls" on both sides of the film However, in actual production, the electroplating pattern is much thicker than the photosensitive pattern around the world In the process of electroplating copper and lead tin, because the electroplating height is higher than the photosensitive film, there is a trend of horizontal accumulation, which leads to the problem The tin or lead tin anti-corrosive layer covering the line extends to both sides to form an "edge", under which a small part of the photosensitive film is covered The "edge" formed by tin or lead tin makes it impossible to completely remove the film when removing it, leaving a small part of "residual glue" under the "edge" The "residual glue" or "residual film" left under the "edge" of the resist will lead to incomplete etching After etching, the lines form "copper root" on both sides The copper root narrows the line spacing, resulting in the printed board not meeting the requirements of Party A, and may even be rejected Rejection will greatly increase the production cost of PCB products In addition, in many cases, due to the formation and dissolution of the reaction, in the printed circuit board industry, the residual film and copper may also form and accumulate in the corrosive liquid, and plug in the nozzle of the corrosion machine and acid resistant pump. It must be closed for treatment and cleaning Affect work efficiency
PCB board
3. Equipment adjustment and interaction with corrosion solution
In PCB medium plate processing, ammonia etching is a relatively fine and complex chemical reaction process On the other hand, it is an easy job Once the process is upgraded, production can continue The key is to keep working continuously after opening. It is not recommended to dry and stop The etching process depends to a large extent on the good working conditions of the equipment At present, no matter what kind of etching solution is used, high-pressure spray must be used. In order to obtain a cleaner line side and high-quality etching effect, nozzle structure and spraying method must be strictly selected In order to obtain good side effects, many different theories have emerged, forming different design methods and equipment structures These theories are usually very different However, all etching theories recognize the basic principle of keeping the metal surface in constant contact with fresh etching solution as soon as possible The chemical mechanism analysis of the etching process also confirmed the above viewpoint In ammonia etching, assuming that all other parameters remain unchanged, the etching rate is mainly determined by the ammonia (NH3) in the etching solution. Therefore, there are two main purposes for etching the surface with fresh solution: one is to wash the newly generated copper ions; The other is to continuously provide ammonia (NH3) required for the reaction. In traditional knowledge, the printed circuit board industry, especially the raw materials of suppliers' printed circuit boards, is well known that the lower the content of monovalent copper ions in ammonia etching solution, the faster the reaction speed This has been proved by experience In fact, many amino acid etching solution products contain special ligands (some complex solvents) of monovalent copper ions, which are used to reduce monovalent copper ions (these are the technical secrets of their highly reactive products). It can be seen that the influence of monovalent copper ions is not small Reducing the unit price of copper from 5000 ppm to 50 ppm will more than double the etching rate Because a large number of monovalent copper ions will be generated during the etching reaction, because monovalent copper ions are always closely bound with the complexing group of ammonia, it is difficult to keep its content close to zero The univalent copper tank converts univalent copper into bivalent copper through the role of oxygen in the atmosphere for removal. This can be achieved by spraying This is the functional reason for allowing air to enter the etch box However, if there is too much air, it will accelerate the loss of ammonia in the solution and reduce the pH value, leading to a reduction in the etching rate Ammonia in the solution is also a change that needs to be controlled Some users adopt the method of passing pure ammonia into the etching tank Therefore, it is necessary to add a set of pH meter control system When the pH value measured automatically is lower than the given value, the solution will be added automatically In the related chemical etching (called photochemical etching or PCH) field, research work has begun and has reached the stage of etching machine structure design In this method, the solution used is bivalent copper, non ammonia copper etching It can be used in the printed circuit board industry In the PCH industry, the typical thickness of etched copper foil is 5. to 10 mils, which in some cases is quite large Its requirements for etching parameters are generally higher than those of the printed circuit board industry
4. The etching state of the leading edge and the trailing edge is different for the upper and lower plate surfaces
A large number of problems related to the etching quality focus on the etching part of the upper plate surface. It is very important to understand this These problems are due to the influence of the colloid compaction produced by the etchant on the surface of the printed circuit board On the one hand, the colloidal plates gathered on the copper surface will affect the jet force; on the other hand, it prevents the supplement of fresh etching solution, which will reduce the etching speed It is due to the formation and accumulation of colloidal boards that the upper and lower patterns of circuit boards are etched to different degrees This also makes the first part of the circuit board in the etching machine easy to be completely etched or lead to excessive corrosion, because there is no accumulation at that time, and the etching speed is faster On the contrary, the part after entering the plate has formed at the time of entering and slows down its etching speed
5. Maintenance of etching equipment
The key factor in maintaining the etching equipment is to ensure that the nozzle is clean and free of obstacles so that the jet can flow freely. Under the action of jet pressure, blockage or slagging will affect the layout If the nozzle is not clean, it will lead to uneven etching, and the entire PCB will be damaged Obviously, equipment maintenance refers to the replacement of damaged and worn parts, including the replacement of nozzles The nozzle also has wear problems In addition, the more critical problem is to keep the etcher free of slagging In many cases, slagging will accumulate Excessive slagging may even affect the chemical balance of the etching solution Similarly, if there is excessive chemical imbalance in the etching solution, slagging will become more serious The problem of slag accumulation cannot be overemphasized Once a large amount of slagging suddenly appears in the etching solution, this is usually a signal indicating that there is a problem with the balance of the solution Strong hydrochloric acid shall be used for cleaning or replenishing the solution The residual film will also produce slagging, and a small amount of residual film will dissolve in the etching solution, and then form copper salt precipitation The slagging of the residual membrane indicates that the previous membrane removal process is incomplete Poor film removal is usually caused by excessive edge film and electroplating on PCB boards