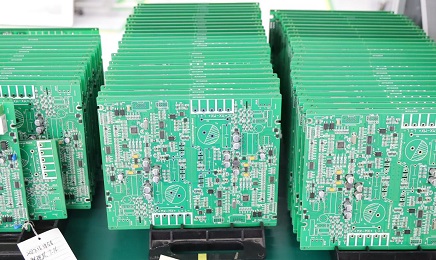
Common PCB Problems and Faults Guide
Printed circuit board (PCB) is the basic component of many electrical equipment today. Different components are connected with each other through complex circuit arrays. The global demand for PCB has grown rapidly. In the past eight years, the global total sales of printed circuit boards have increased by more than 3.7 billion US dollars annually on average, and more attention has been paid to reducing conflict minerals supply chain problems and improving technology. As of 2018, the global PCB sales were about $82 billion.
Due to the large amount of investment in PCB, and their important role in many electrical equipment and boxed components, PCB failure is the main concern of many companies. Next, you will learn the most common causes behind PCB faults in detail, so that your company can better effectively prevent and solve PCB faults.
What is a PCB fault?
PCB failure may occur for many reasons, and the final result is that PCB no longer works normally. Since pcba is manufactured for many electronic products, such as wearables, aircraft, satellites and medical devices, it is critical to quickly identify any faults and take appropriate measures. Any company that wants to keep its electronic equipment running smoothly can better solve PCB failures, and even prevent them by knowing more about their causes.
Causes of PCB failure
The complexity of PCBA design and manufacturing process means that there are many opportunities for PCB failure. Some of these failures are caused by the design negligence of the pcba manufacturer, such as insufficient clearance or incorrect measurement, which will have a negative impact on the function of the finished product. Others may be caused by problems in the manufacturing process, such as drilling errors or excessive etching, which is also disastrous.
Fortunately, most of these mistakes can be avoided by understanding and considering the manufacturing process and the more common problems in the pcba chip processing plant. In order to help you and your company better understand and avoid potential errors in PCB design, we have compiled a list of the most common problems in pcba processing. Their causes and how to prevent them are as follows:
1. Plating gap
2. Insufficient copper edge clearance
3. Poor welding
4. Slips
5. Lack of solder mask between pads
6. Acid trap
7. Components with poor manufacturing
8. Hungry calories
The root cause of this problem most often occurs in the manufacturing process. These hot connections are usually correctly connected to plane layers in computer aided design (CAD) systems, but in some way the connection to the rest of the plane is reduced. Manufacturing problems during hot forming or processing, such as excessive processing or improper forming, can cause this problem. To solve this problem, it is usually best to replace the heat sink.