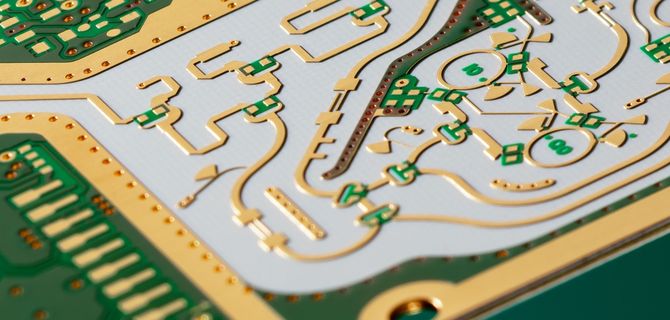
DFM Requirements for Installing SMD/SMC Devices on FPC
1. Process requirements for FPC design
SMT processing practice has proved that the installation size of FPC should not be too large, and the normal position is 2.50mm * 200mm (for small devices with only capacitors, resistors, and inductances) If the FPC is equipped with an integrated circuit and headphones For motors, USB ports, and connectors with large number of pins, it â S best to control the position size within 250mm * 150mm, because the larger the board, the greater the expansion and contraction of FPC FPC will not be printed for SMT processing and printing solder paste On the mat In consideration of efficiency and quality output, SMT processing and production should pay attention to the following issues
1.1. The overall production efficiency must be fully considered for the size and quantity of plates.
1.2. Design requirements for locating holes and optical identification points on FPC.
The positioning hole (SMT positioning hole) and optical identification alignment point (SMT alignment identification point) on FPC need to meet the precision requirements of solder paste printing and placement. Because they directly affect the quality and placement of FPC printing pastes. The positioning difference shall be controlled within 0.1mm. At the same time, the positioning holes and alignment points of each plate must be consistent.
Circuit board
1.3. The key point of the evaluation is the selection of the structure of the reinforced flexible circuit board
The number and structure of FPC base plate, the data selection and thickness requirements of stiffening plate, and the connection point process is an important part of SMT process evaluation They greatly affect the yield of FPC chip assembly and the reliability of FPC components after welding
1. Surface treatment process requirements of FPC device pad.
2.1 ENEG process of nickel gold electroplating.
2.2. Study ENIG technology insurance. The influence of nickel gold pad abnormality on SMT processing and welding can refer to the analysis and rework method of abnormal welding caused by ENIG pad in "Modern Surface Mount Information"
2.3. Organic protective film (OSP) process.
The above three processes are common pad processing processes of FPC, each with advantages and disadvantages.
The choice of pad surface treatment process also determines the reliability of welding. For example, nickel gold is easy to produce "black pad", which directly affects the solderability of SMT. OSP process has high requirements for FPC production before SMT. The film is easy to oxidize, which is fatal to SMT welding. For more information, please refer to the study on the weldability of BGA with different surface treatments in SMT process in the 6th issue of "Modern SMT Information" in December 2012. 3. Soldering resistance design requirements for FPC pads.
The solder mask on the FPC (SolderMask) is similar to the "green oil" on the PCB. The difference is that the green oil on the PCB is Silk screened, while the solver mask on the FPC is made by the following two methods: This is a polyimide film as the material The windowing system is formed by drilling and punching the die The other one is the same as the green oil on PCB No matter what "window opening" method is used For SMD/SMC equipment pads, ensure that the pads are uniform and symmetrical, and the pads cannot be covered by solder mask
During the welding process, the bad pads on the welding mask will reduce the solderable area of SMT, which will lead to the reliability failure after welding.
In the SMD/SMC pad design, there are two main channels for opening windows: one is SMD (defined solder mask) solder mask limitation, and the other is NSMD (defined non solder mask) non solder mask.
The above are the four windowing methods for SMD/MSC pads. It now uses NSMDPAD and NSMD to open windows. For these two window opening methods, it is necessary to align the cover film and the green solder mask.
4. The design rationality of SMD/SMC pad affects SMT processing.
4.1. The design of the equipment pad is based on the customer's original window opening, which may be defective during SMT processing.
4.2. The matching between the pad on the FPC and the solder leg of SMD/SMC devices has an impact on SMT processing and welding.
4.2.1. The bonding pad on the FPC is smaller than the SMD soldering pin/SMC equipment, and SMT cannot be soldered
4.2.2. The internal distance of pads on FPC is too large. The internal distance of the pad on the FPC is too large, which causes the SMD/SMC device's solder legs cannot be placed on the pad, which directly causes the SMT cannot be welded.
4.3. Whether SMD solder pins/SMC devices match with corresponding SMD pads/whether SMC FPC devices match
In the design process of FPC, it is necessary to consider the matching of SMD/SMC device solder pins with corresponding SMD/SMC devices on FPC. For example, FPC needs to install 0402 equipment, but the pad design on FPC conforms to 0603 pad specification. This makes it impossible to weld in the SMT. Replace 0603 equipment, or adjust the pad design on FPC.
The above is the explanation given by the editor of pcb circuit board company.
If you want to know more about PCBA, you can go to our company's home page to learn about it.
In addition, our company also sells various circuit boards,
High frequency circuit board and SMT chip are waiting for your presence again.