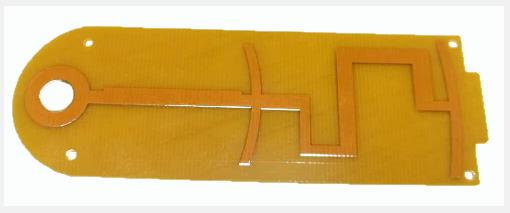
Precautions for stack design of mobile phone wireless charging circuit board
Circuit board manufacturing, circuit board design, PCBA manufacturers explain to you the matters needing attention in the laminated design of mobile phone wireless charging circuit boards
When designing the wireless charging circuit board for mobile phones, one of the most basic issues to consider is how many wiring layers, grounding planes and power planes are required to achieve the required functions of the circuit. The determination of the number of layers of wiring layers, grounding planes and power planes of the printed circuit board is related to the requirements of circuit functions, signal integrity, EMI, EMC, manufacturing costs, etc. For most designs, there are many conflicting requirements for factors such as performance requirements, target cost, manufacturing technology and system complexity of mobile phone wireless charging circuit board. The stack design of mobile phone wireless charging circuit board is usually a compromise after considering various factors. High speed digital circuit and transmitter circuit usually adopt multilayer board design. The following lists 8 principles for cascade design.
1. Layering
In multilayer mobile phone wireless charging circuit board, it usually includes signal layer (S), power (P) plane and ground (GND) plane. The power plane and ground plane are usually undivided solid planes, which will provide a good low impedance current return path for the current of adjacent signal lines. Most of the signal layers are located between these power or ground reference plane layers, forming symmetrical striplines or asymmetrical striplines. The top layer and bottom layer of multi-layer mobile phone wireless charging circuit board are usually used to place components and a small amount of cabling. These signal cabling should not be too long to reduce the direct radiation generated by cabling.
2. Determine the single power supply reference plane
Using decoupling capacitor is an important measure to solve the integrity of power supply. The decoupling capacitor can only be placed on the top and bottom layers of the mobile phone wireless charging circuit board. The wiring, bonding pad and via of decoupling capacitor will seriously affect the effect of decoupling capacitor, which requires that the wiring connecting decoupling capacitor should be as short and wide as possible, and the wire connected to via should also be as short as possible. For example, in a high-speed digital circuit, the decoupling capacitor can be placed on the top layer of the mobile phone wireless charging circuit board, the second layer can be assigned to the high-speed digital circuit (such as the processor) as the power layer, the third layer as the signal layer, and the fourth layer as the high-speed digital circuit ground. In addition, it is necessary to ensure that the signal wiring driven by the same high-speed digital device takes the same power supply layer as the reference plane, and this power supply layer is the power supply layer of high-speed digital devices.
3. Determine the multi power reference plane
The multi power reference plane will be divided into several solid regions with different voltages. If the signal layer is close to the multiple power supply layer, the signal current on the signal layer near it will encounter an undesirable return path, causing gaps in the return path. For high-speed digital signals, this unreasonable return path design may cause serious problems, so high-speed digital signal wiring should be far away from the multi power reference plane.
4. Determine multiple ground reference planes
Multiple ground reference planes (ground planes) can provide a good low impedance current return path, which can reduce the common mode EMl. The ground plane and the power plane should be closely coupled, and the signal layer should also be closely coupled with the adjacent reference plane. This can be achieved by reducing the thickness of the medium between layers.
5. Reasonably design wiring combination
The two layers crossed by a signal path are called a "wiring combination". The best wiring combination design is to avoid the return current flowing from one reference plane to another, but from one point (face) of one reference plane to another. In order to complete the complex cabling, the inter layer conversion of routing is inevitable. During signal layer to layer conversion, it is necessary to ensure that the return current can flow smoothly from one reference plane to another. In a design, it is reasonable to take the adjacent layer as a wiring combination. If a signal path needs to span multiple layers, it is usually not a reasonable design to take it as a wiring combination, because a path passing through multiple layers is not smooth for the return current. Although the ground spring can be reduced by placing decoupling capacitors near the vias or reducing the dielectric thickness between reference planes, it is not a good design.
6. Set wiring direction
On the same signal layer, it shall be ensured that the direction of most wiring is consistent and orthogonal to the wiring direction of adjacent signal layers. For example, you can set the wiring direction of one signal layer as the "Y axis" direction, and set the wiring direction of another adjacent signal layer as the "X axis" direction.
7. Even layer structure
It can be found from the stack of the designed mobile phone wireless charging circuit board that the classical stack design is almost all even layers, rather than odd layers. This phenomenon is caused by a variety of factors. It can be learned from the manufacturing process of the printed circuit board that all conductive layers in the circuit board are saved on the core layer. The core layer is generally made of double-sided cladding. When the core layer is fully used, the conductive layers of the printed circuit board are even. Even layer printed circuit board has cost advantage. The cost of raw materials of odd layer PCB is slightly lower than that of even layer PCB due to the lack of one layer of dielectric and copper coating. However, because the odd layer PCB needs to add non-standard laminated core bonding process on the basis of core structure process, the processing cost of odd layer PCB is significantly higher than that of even layer PCB. Compared with the ordinary core structure, adding copper coating outside the core structure will lead to the decline of production efficiency and the extension of production cycle. Before laminating and bonding, the outer core layer needs additional process treatment, which increases the risk of outer layer being scratched and wrongly etched. The additional coating treatment will greatly increase the manufacturing cost. PCB manufacturers, PCB designers and PCBA manufacturers will explain to you the matters that should be paid attention to in the stack design of mobile phone wireless charging PCB.