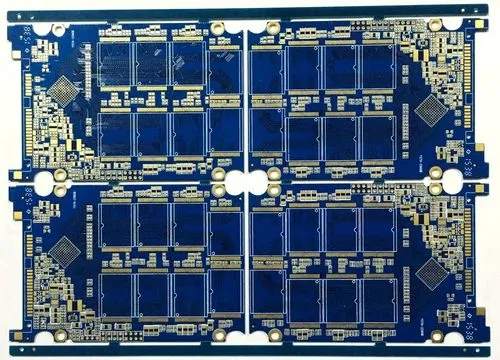
The circuit board manufacturer explains that the performance of DC-DC switching power supply is closely related to PCB layout
The performance of DC-DC switching power supply is closely related to the layout of PCB. Because switching DC-DC has the consideration of fast switching, power supply passing current and heat dissipation, unreasonable layout and wiring will greatly affect the power supply performance, and will form a serious noise source.
Layout:
In the layout of switching regulators, the layout of the AC path is extremely important, while the DC path can be considered secondary, but the feedback signal strength is the only key signal of the entire DC-DC power supply.
As we all know, Trace on PCB has inductance, which is about 20nH/inch. As long as there is current flowing through Trace, it will generate induced voltage, but the voltage value depends not on the size of current but on the change rate of current, V=L * (dI/dt). Therefore, the AC path is very important in PCB design, especially for DC-DC integrated circuits using high-speed switch tubes, the dI/dt will be very high. NS (National Semiconductor of the United States) gave a rough figure: "For a typical step-down converter, the current change of the AC part is 1.2 times of the load current during the switch off process and 0.8 times of the load current during the switch on process." Here, the trace of the AC path must be as short as possible, including the trace of the GND pin. Although the current flowing through the GND pin is very small, the switch switch process will refresh the current through the GND pin, and the current will become very steep. This means that the input capacitor and bypass capacitor should be placed as close to the IC as possible, especially for the step-down IC.
The space around the IC is limited, so the input capacitance and bypass capacitance cannot be placed close to the IC at the same time, especially the input capacitance is relatively large.
First of all, understand the role of the input capacitor, which is to make the input voltage to the IC as stable as possible and reduce the voltage fluctuation. In fact, it should be said that the large input capacitor can be regarded as the total power supply on the board. At the same time, the equivalent series resistance (ESR) and equivalent series inductance (ESL) of the input capacitor may be very high, which will cause high-frequency input voltage ripple at the input power supply pin of the IC. Therefore, the input capacitor can be placed within about 1 inch from the IC.
The bypass capacitor must be as close as possible to the input power supply pin of the IC. The bypass flashlight with short pin or no pin generally uses a ceramic capacitor of 0.1uF to 0.47uF, which has a good effect on filtering high-frequency ripple. Short pin or no pin will reduce the parasitic inductance (ESL) of the capacitor. At the same time, 1206 and X7R packages are generally used. If a small package size is used, the ESL and ESR of the capacitor will increase. Generally, such bypass capacitors should be placed beside the power supply pins of ICs.
There will be a clamping diode in the DC-DC switching power supply, and its placement is also critical. Since one end of the clamping diode is a SW pin connected to the IC, the signal of this pin is a rectangular wave. If the Trace is too long, its inductance will easily pick up the noise and add it to the SW signal to form a noise spike. The basic point of the clamping diode layout is to place it close to the IC, and use a short and wide Trace to directly connect the SW pin and GND pin of the IC.
When the input bypass capacitor and clamping diode are positioned properly, other devices can be laid out. The Trace connecting the input bypass capacitor and clamping diode should be as short and wide as possible, and there should be no through-hole in the path connected to the IC, which means they need to be on the same layer with the IC for the SMT PCB. The absence of vias here only means that VIA should not be activated in the Trace between the IC and the input bypass capacitor and clamping diode. However, if a double-sided or multilayer board needs to be connected to GND and Power Layers through VIA, VIA can be activated next to the PAD near the input bypass capacitor and clamping diode instead of in the connected Trace.
Wiring:
In many cases, copper coating is misused. Copper coating on GND plane or VCC plane is no problem. It can reduce the current loop impedance and serve as a reference for key signals to reduce interference. However, the clamping diode wiring mentioned in the layout just now should be short and wide, but not the wider the better. It is easy to understand that Trace is short. Everyone will realize that the rule of thumb of "20nH/inch" is that Trace inductance is proportional to the length. But isn't Trace inductance inversely proportional to the width? Usually many people will intuitively think yes. According to Trace inductance formula:
L = 2l * [ln(2l/w) - 0.5 + 0.2235 * (w/l)]
It can be seen that the inductance value and Trace width are nonlinear. To reduce the effect of parasitic inductance, widening Trace should be the last resort. The first step should be to reduce Trace length. In particular, since the clamping diode is connected to the SW pin, the voltage itself is a switching waveform. If the trace is replaced by an excessively wide copper coating, it will be considered as an antenna and an EMI problem will be introduced. For the switch node, the best choice is to control the size of the copper foil around it within the minimum range of actual requirements.
It is a common phenomenon in Layout that the power cord is replaced by copper coating. It is believed that the greater the copper laying is, the greater the current can be carried. In fact, the larger the cross-sectional area (width * thickness) of copper is, the smaller the Trace resistance per unit length is, and the smaller the heat generation is. The essence of current processing capacity is the temperature rise of Trace. We should determine the size of Trace in the power supply part through quantitative calculation, and should not lay too much copper. Generally, the temperature rise of 30 ℃~40 ℃ is acceptable, and it is also affected by the surrounding heating devices. It must not exceed the rated temperature of the epoxy resin board (FR4 should be kept below 120 ℃).
A rule of thumb: for moderate temperature rise (below 30 ℃) and current less than 5A
For 1oz copper, at least 12mil wide copper foil shall be used for 1A current
For 2oz copper, at least 7mil copper foil shall be used for 1A current
GND plane, try to keep the integrity of the ground plane, do not split or route on the ground plane, but double-sided boards are difficult to do this. This principle must be observed for multilayer boards. However, sometimes when it is necessary to divide the digital ground plane, analog ground plane or high and low voltage ground plane, it is necessary to divide the ground plane, but finally the two separated ground planes must be connected through magnetic beads or 0 ohm resistors to maintain electrical connection and consistency. The complete ground plane is important for the control of anti-interference and impedance of PCB, because it is a reference and return path of signal.
The feedback line in DC-DC switching power supply is the only key signal in the signal line. There are two solutions: 1. Use short feedback Trace as far as possible to minimize the picked up noise; 2. Keep away from noise sources, such as inductors or diodes. Sometimes it is necessary for Trace to walk longer to avoid noise sources. The circuit board manufacturer explains that the performance of DC-DC switching power supply is closely related to PCB layout and wiring.