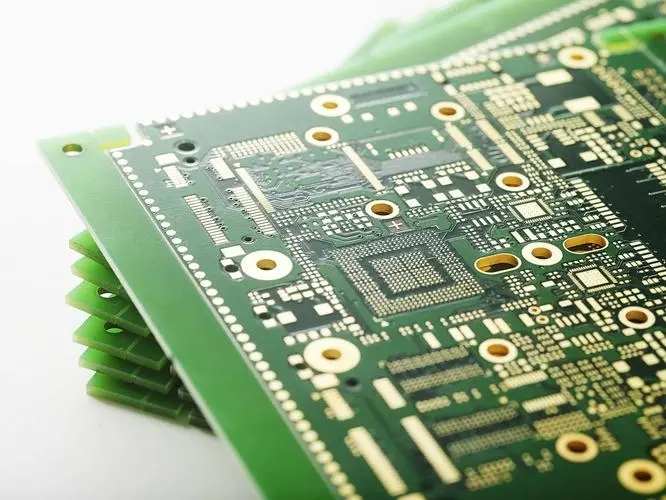
Circuit board factory explains common stack structure of HDI PCB
1. Simple once laminated printed board (once laminated 6 layers, laminated structure is (1+4+1))
This type of board is the simplest, that is, the inner multilayer board has no embedded holes, and the pressing is completed at one time. Although it is a one-time laminated board, its manufacturing is very similar to the conventional multilayer board, which is laminated at one time, but the subsequent process is different from the multilayer board, which requires multiple processes such as laser drilling blind holes. Since this laminated structure has no embedded holes, the second and third layers can be used to make a core plate, the fourth and fifth layers can be used as another core plate, the outer layer is added with a medium layer and copper foil, and the middle layer is added with a medium layer and then pressed together at one time. This is very simple, and the cost is lower than that of conventional one-time laminated plates.
2. Conventional once stacked HDI printed boards (once stacked HDI 6-layer boards, with a stacking structure of (1+4+1))
The structure of this type of panel is (1+N+1), (N ≥ 2, N even number). This structure is the mainstream design of primary laminates in the industry at present. The inner multilayer plates have embedded holes, which need secondary pressing. In addition to blind holes, this type of primary laminate also has embedded holes. If designers can convert this type of HDI into the first type of simple primary laminate, it will be beneficial to both the supply and demand. After our suggestion, we have many customers who prefer to change the stacking structure of the second type of conventional primary laminate to a simple primary laminate similar to the first type.
3. Conventional secondary stacking HDI printed board (secondary stacking HDI 8-layer board, with a stacking structure of (1++1+4+1+1))
The structure of this type of plate is (1+1+N+1+1), (N ≥ 2, N even number). This structure is the mainstream design of secondary lamination in the industry at present. The inner multilayer plate has embedded holes, which needs three times of pressing. The main reason is that there is no overlapping hole design, and the manufacturing difficulty is normal. If we can change the buried holes of (3-6) layers to those of (2-7) layers as mentioned above, we can reduce one pressing, optimize the process and achieve the effect of reducing costs. This type is like the following example.
4. Another conventional secondary stacking HDI printed board (secondary stacking HDI 8-layer board, with a stacking structure of (1+1+4+1+1))
Although the structure of such plates (1+1+N+1+1), (N ≥ 2, N even number) is the structure of secondary laminates, because the location of the buried holes is not between (3-6) layers, but between (2-7) layers, this design can also reduce the pressing once, so that the HDI plates of secondary laminates need three pressing processes, which are optimized to be two pressing processes. However, there is another difficulty in making such plates. There are (1-3) layers of blind holes, which are divided into (1-2) layers and (2-3) layers of blind holes. The inner blind holes of (2-3) layers need to be made by filling holes, that is, the inner blind holes of the secondary laminate are made by filling holes. Generally, the HDI cost of the prepared hole filling process is higher than that of the non prepared hole filling process, and the difficulty is also obvious. Therefore, in the design process of conventional secondary laminate, It is recommended not to adopt the overlapping hole design as far as possible, and try to convert (1-3) blind holes into staggered (1-2) blind holes and (2-3) buried (blind) holes. Some experienced designers can adopt this simple design or optimization to reduce the manufacturing cost of their products.
5. Another unconventional secondary stacking HDI printed board (secondary stacking HDI 6-layer board, with a stacking structure of (1+1+2+1+1))
Although this type of panel structure (1+1+N+1+1), (N ≥ 2, N even number) is a secondary laminate structure, there are also cross layer blind holes, and the depth capacity of blind holes is significantly increased. The depth of blind holes in (1-3) layers is twice that of the conventional (1-2) layers. Customers of this design have their own unique requirements, and it is not allowed to make (1-3) cross layer blind holes into stacked blind holes (1-2) (2-3) blind holes, In addition to the difficulty of laser drilling, the subsequent copper deposition (PTH) and electroplating are also difficult. Generally, PCB manufacturers without a certain level of technology are difficult to make such boards, which are significantly more difficult than conventional secondary laminates. This design is not recommended unless there are special requirements.
6. HDI of secondary stack for blind hole stacking design, and blind hole stacking above buried hole (2-7) layer. (Secondary laminated HDI 8-layer board, laminated structure is (1+1+4+1+1))
The structure of this type of plate is (1+1+N+1+1), (N ≥ 2, N even number). This structure is the design of some secondary laminated plates in the industry at present. The inner multilayer plates have embedded holes, which need secondary pressing. The main feature of this design is that there is a stacked hole design, which replaces the cross layer blind hole design in point 5 above. The main feature of this design is that the blind hole needs to be stacked above the (2-7) buried hole, which makes it more difficult to make. The embedded hole design is in the (2-7) layer, which can reduce a lamination, optimize the process and achieve the effect of reducing costs.
7. HDI of secondary stack designed by cross layer blind hole (secondary stack HDI 8-layer board, the stack structure is (1+1+4+1+1))
The structure of this type of plate is (1+1+N+1+1), (N ≥ 2, N even number). This structure is a secondary laminated plate which is difficult to make in the industry at present. In this design, the inner multilayer plate has embedded holes in (3-6) layers, which requires three times of pressing. This is mainly due to the cross layer blind hole design, which is difficult to make. HDI PCB manufacturers without certain technical capabilities are difficult to make such secondary laminated boards. If such cross layer blind holes (1-3) are optimally split into (1-2) and (2-3) blind holes, this method of splitting blind holes is not the stacking and splitting method described in points 4 and 6 above, but the splitting method of stagger blind holes, It will greatly reduce the production cost and optimize the production process.
8. Optimization of HDI boards with other laminated structures
Three times laminated printed boards or PCB boards with more than three times laminated can also be optimized according to the design concept provided above. For complete three times laminated HDI boards, the entire complete production process requires four times of lamination. If you can consider the design idea similar to the previous one or two times laminated boards, you can completely reduce the production process of one time laminated, thus improving the yield of boards. In many of our customers, there is no shortage of such examples. The stack structure designed at the beginning requires four times of lamination. After the optimization of the stack structure design, PCB production requires only three times of lamination to meet the functions required for three times of lamination. The circuit board assembly, circuit board design, and circuit board processing manufacturers explain the common stack structure of HDI PCB.