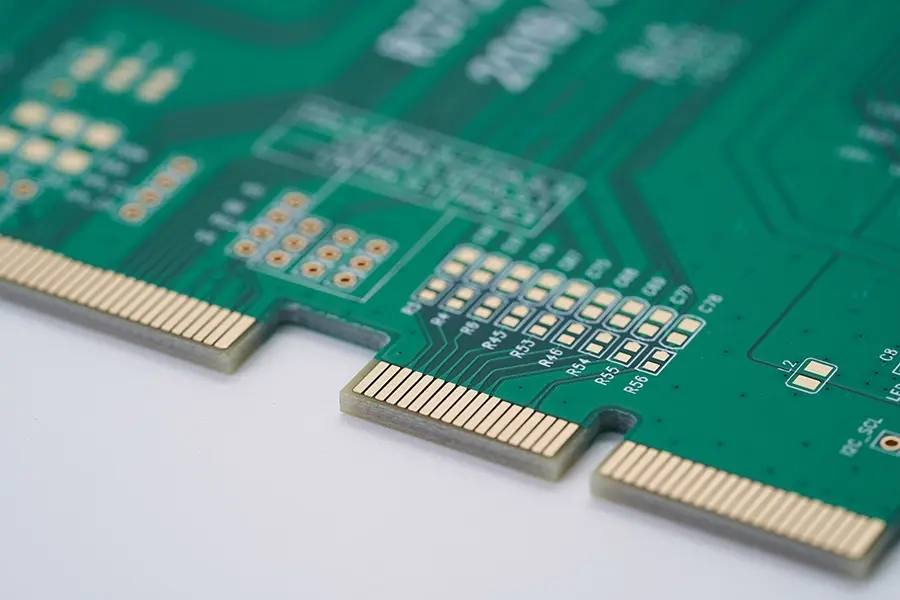
Expert solutions to high-speed circuit board design methods Part 4
29. Circuit board design and EMC! If EMC is considered in circuit board design, it will definitely increase the cost. How can I answer EMC requirements as much as possible without too much cost pressure? thank you.
Expert answer:
The increased cost of EMC on PCB is usually due to the increase of the number of layers to enhance the shielding effect and the addition of high-frequency harmonic suppression devices such as ferrite beam and choke. In addition, the shielding structure of other institutions is usually required to make the whole system pass the EMC requirements. Here are just a few ways to reduce the electromagnetic radiation effects generated by circuits based on PCB design techniques.
1. Devices with slow signal slope rate shall be selected as far as possible to reduce the high-frequency components generated by the signal.
2. Pay attention to the placement of high-frequency components, and do not be too close to external connectors.
3. Pay attention to the impedance matching of high-speed signals, the routing layer and its return current path to reduce high-frequency reflection and radiation.
4. Place enough and appropriate decoupling capacitors on the power supply pins of each device to mitigate the noise on the power supply layer and stratum. Pay special attention to whether the frequency response and temperature characteristics of the capacitor meet the design requirements.
5. The ground near the external connector can be properly separated from the stratum, and the ground near the connector can be connected to the chassis ground.
6. The ground guard/hunt traces can be properly used beside some signals with high speed. However, we should pay attention to the influence of guard/hunt traces on the characteristic impedance of the wiring.
7. The power layer is 20H smaller than the formation, and H is the distance between the power layer and the formation.
30. Multiple digital/analog ground connection. When there are multiple digital/analog function blocks in a PCB, the conventional practice is to separate the digital/analog ground and connect them at one point. In this way, the ground on a PCB will be divided into multiple pieces, and how to connect each other is also a big problem. However, someone has adopted another method, that is, under the condition of ensuring that the digital/analog signals are laid out separately and the digital/analog signal wiring is not crossed, the entire PCB floor is not divided, and the digital/analog floor is connected to this ground plane. What is the reason for this? Please consult the experts.
Expert answer:
The reason for separating D/A from ground is that the digital circuit will generate noise in the power supply and ground when switching between high and low potentials. The size of the noise is related to the speed and current of the signal. If the ground plane is not divided and the noise generated by the digital area circuit is large and the analog area circuit is very close, the analog signal will still be interfered by the ground noise even if the digital and analog signals do not intersect. That is to say, the digital analog ground undivided mode can only be used when the analog circuit area is far away from the digital circuit area that generates large noise. In addition, the requirement that the routing of digital and analog signals cannot cross is that the return current path of a faster digital signal will return to the source of the digital signal as far as possible along the ground near the lower part of the routing. If the routing of digital and analog signals crosses, the noise generated by the return current will appear in the analog circuit area.
31. Please introduce the EDA software for making PCB Usually Protel is popular and there are many books on the market. Please introduce the advantages and disadvantages of Protel, PowerPCB, orCAD and other software and their application occasions. thank you.
Expert answer:
I don't have much experience in using these software. Here are just a few directions for comparison:
1. Whether the user's interface is easy to operate;
2. The ability to push the wire (this item relates to the strength of the winding engine);
3. The difficulty of laying copper foil and editing copper foil;
4. Whether the setting of routing rules meets the design requirements;
5. Type of organization chart interface;
6. Whether it is easy to create, manage and call the part library;
7. Check whether the ability of design error is perfect;
32. Impedance matching in PCB design In the design of high-speed PCB, impedance matching must be considered in order to prevent reflection. However, because PCB processing technology limits the continuity of impedance, simulation cannot be imitated. How to consider this problem in schematic design? In addition, I do not know where to provide a more accurate IBIS model library. Most of the libraries we downloaded from the Internet are not accurate, which greatly affects the reference of the simulation.
Expert answer:
When designing high-speed PCB circuits, impedance matching is one of the elements of design. The impedance value has an absolute relationship with the routing method. For example, when walking on the surface layer (microstrip) or the inner layer (stripe/double stripe), the distance from the reference layer (power layer or stratum), the routing width, PCB material, etc. will affect the characteristic impedance value of the routing. That is to say, the impedance value can be determined only after wiring. General simulation software can't take into account some discontinuous impedance wiring due to the limitation of line model or mathematical algorithm used. At this time, only some terminators (such as series resistance) can be reserved on the schematic diagram to mitigate the effect of discontinuous impedance wiring. The real fundamental solution to the problem is to avoid impedance discontinuity when wiring.
The accuracy of IBIS model directly affects the simulation results. Basically IBIS can be regarded as the electrical characteristics data of the actual chip I/O buffer equivalent circuit, which can generally be converted from the SPICE model (measurement can also be used, but there are many restrictions). The SPICE data has an absolute relationship with the chip manufacturing, so the SPICE data of the same device provided by different chip manufacturers are different, and the data in the converted IBIS model will also vary accordingly. That is to say, if manufacturer A's devices are used, only they can provide accurate model data of their devices, because no one knows better than them what process their devices are made by. If the IBIS provided by the manufacturer is inaccurate, the fundamental solution is to constantly require the manufacturer to improve.
33. EMC and EMI problems in high-speed PCB design When designing high-speed PCB, the software we use is just to check the set EMC and EMI rules. What aspects should designers consider? How to set the rules? I use the software from CADENCE.
Expert answer:
Generally, radiation and conducted shall be considered simultaneously in EMI/EMC design The former belongs to the part with higher frequency (>30MHz) and the latter belongs to the part with lower frequency (<30MHz) Therefore, we should not only pay attention to the high frequency and ignore the low frequency
A good EMI/EMC design must take into account the position of components, the arrangement of PCB stacks, the way of important online connections, and the selection of components at the beginning of the layout. If there is no better arrangement in advance, it will take twice the effort and increase the cost if it is resolved afterwards For example, the position of the clock generator should not be close to the external connector as far as possible, the high-speed signal should go through the inner layer as far as possible and pay attention to the characteristic impedance matching and the continuity of the reference layer to reduce reflection, the slope rate of the signal pushed by the device should be as small as possible to reduce the high-frequency component, and when selecting the decoupling/bypass capacitor, pay attention to whether its frequency response meets the requirements to reduce the power layer noise In addition, pay attention to the return path of high-frequency signal current to minimize the loop area (that is, the loop impedance is as small as possible) to reduce radiation
The range of high-frequency noise can also be controlled by dividing the stratum Finally, properly select the chassis ground between PCB and housing.
34. How to select EDA tools?
I hope PCB:
1. Make automatic wiring of PCB.
2. (1)+thermal analysis
3. (1)+Time series analysis
4. (1)+impedance analysis
5.(1)+(2)+(3)
6.(1)+(3)+(4)
7.(1)+(2)+(3)+(4)
How should I choose to get the best cost performance. I hope that in terms of PLD: VHDL programming -->Simulation -->Synthesis -->Download and other steps, I should use independent tools separately? Or is it better to use the integrated environment provided by PLD chip manufacturers?
Expert answer:
In the current pcb design software, thermal analysis is not a strong point, so it is not recommended to use it. Other functions 1.3.4 can choose PADS or Cadence with good performance price ratio.
Beginners of PLD design can use the integrated environment provided by PLD chip manufacturers, and can choose a single point tool when designing millions of gates or more.
35. Circuit board design and EMC If EMC is considered in circuit board design, it will definitely increase the cost. How can I answer EMC requirements as much as possible without too much cost pressure? thank you.
Expert answer:
In practical application, it is impossible to fundamentally solve the problem only by relying on PCB design, but we can improve it through PCB:
Reasonable device layout mainly refers to the placement of inductive devices, the shortest possible wiring connection, and the reasonable grounding distribution. When possible, the Chassis ground of all devices on the board is connected together with a special layer, and special junction points are designed which are closely connected with the equipment shell. When selecting devices, the principle of "low or high" should be followed.
36. Comparison of PCB design tools In your personal opinion, for analog circuits (microwave, high-frequency, low-frequency), digital circuits (microwave, high-frequency, low-frequency), analog and digital mixed circuits (microwave, high-frequency, low-frequency), which EDA tool designed for PCB has a better performance price ratio (including simulation)? Can you explain separately.
Expert answer:
Due to my understanding of the application, I can't compare the performance price ratio of EDA tools in depth. The software should be selected according to the application scope. The principle I advocate is that it is sufficient.
For the conventional circuit design, INNOVEDA's PADS is very good, and there is a simulation software for coordination. However, this kind of design often occupies 70% of the application occasions. In high-speed circuit design, analog and digital hybrid circuits, Cadence's solution should be a software with good performance and price. Of course, Mentor's performance is very good, especially in its design process management. Circuit board assembly, circuit board design, circuit board processing manufacturers explain high-speed circuit board design methods Expert answers Part 4.